3 stress factor calibration – Checkline TI-MINIMAX User Manual
Page 95
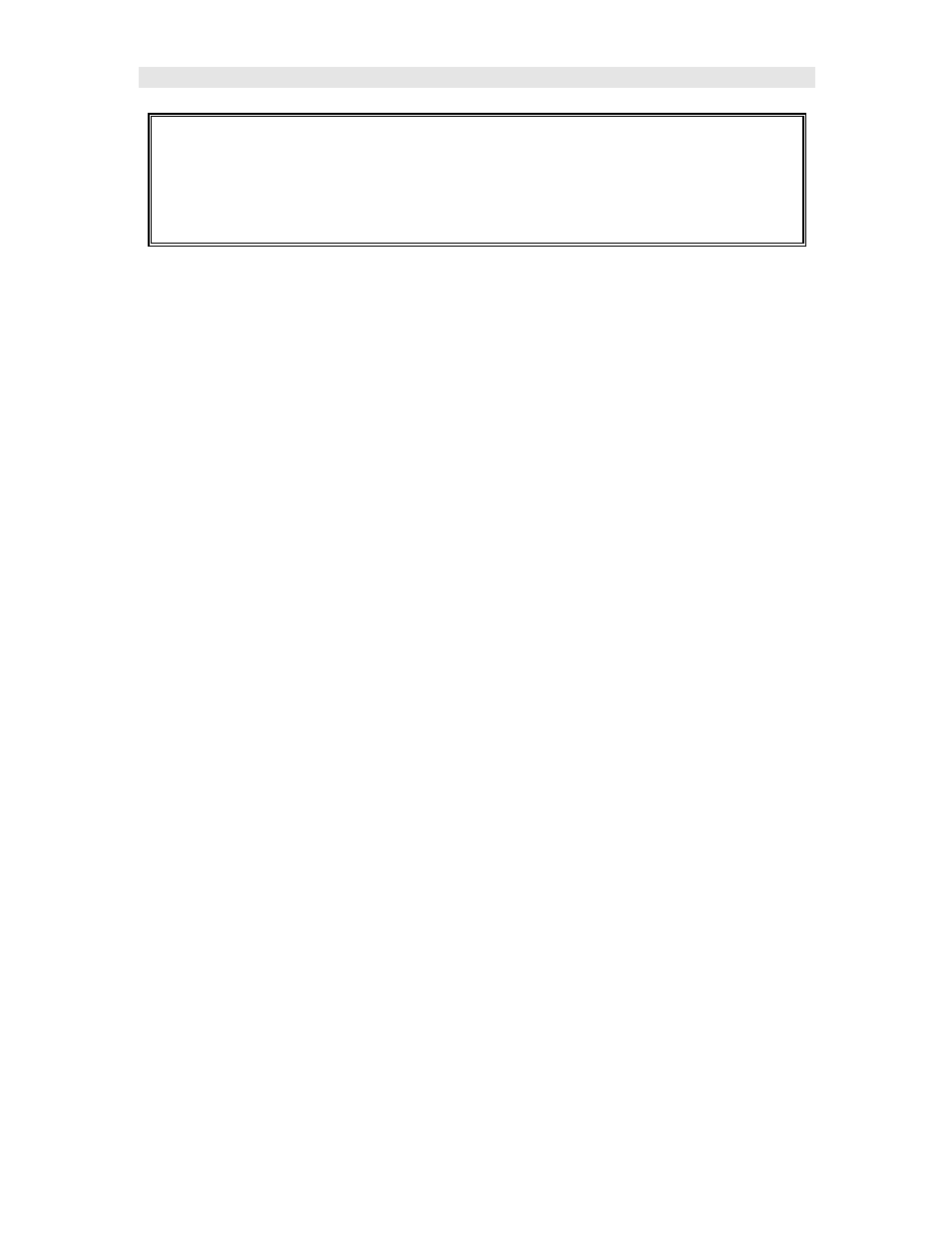
MINI-MAX Ultrasonic Bolt Tension Monitor
25) Finally, press the
MEAS key to return to the measurement screen. The
ultrasonic length displayed should now match the known physical
length.
10.3 Stress factor calibration
The sonic stress factor is an empirically determined value for the bolt material or
type of bolt being measured. It expresses the ratio of the actual elongation, or
stretch, of the bolt, to the apparent ultrasonic change in length. Since the change
in ultrasonic length is approximately 3 times the change in physical length, due to
the change in velocity, a stress factor must be applied to correct the ultrasonic
length in the MINI-MAX.
Following steps determine the Sonic Stress Factor for bolts of a specific bolt
material and specific geometry by measurement of the actual change in bolt
length.
Required Equipment:
•
A laboratory or room in which the temperature can be maintained at
between 66
°
to 70
°
F.
•
A means of applying load to the bolt. Ideally this would be a tensile
load machine, capable of measuring the applied load to within 100
lbs. However, since the actual value of the applied load is not used in
calculating the stress factor, any means of applying an approximate
load to the bolt will suffice. This includes tightening the bolt against a
fixture that simulates the actual joint. A mechanical means of
traceable measurement of the physical length of the sample fasteners
at various tensile loads to an accuracy of plus or minus 0.0001 inch.
Examples of such devices include the following
•
Length measurement function of sophisticated tensile test
machine
•
Mechanical or electronic height gages
•
Averaged values of length measurement with mechanical and
electric micrometers.
•
A Dakota Ultrasonics MINI-MAX Ultrasonic Bolt Tension Monitor.