Rockwell Automation MinPak Plus DC Drives Kits User Manual
Page 42
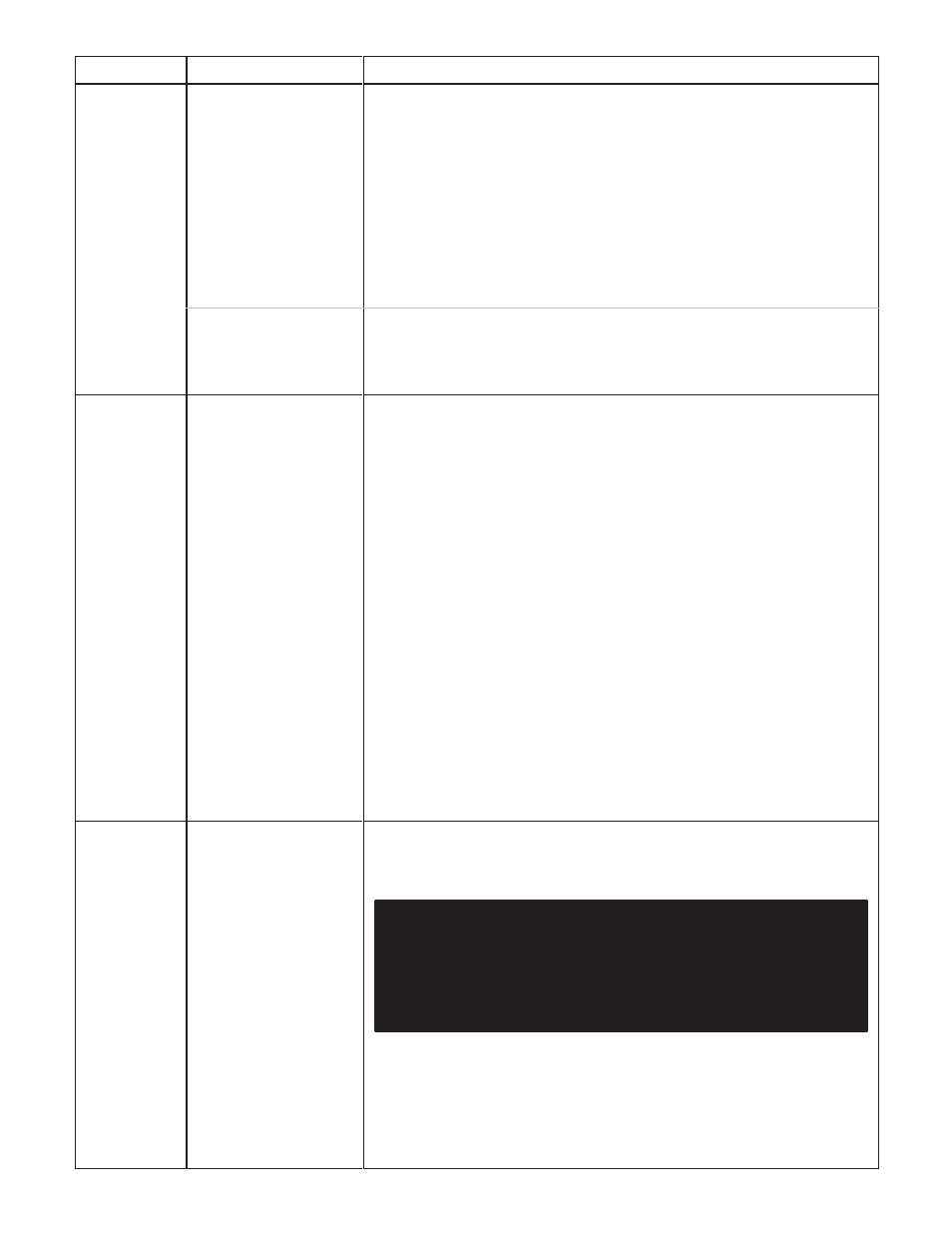
41
SYMPTOM
PROBABLE CAUSE
RECOMMENDED PROCEDURES
6. Drive motor
does not
run, but M
contactor
and CR pull
up.
(Use this
procedure
only if conĆ
troller does
not have
optional
Test Meter
Adapter Kit.)
No input signal from
SPEED pot on Control
Station, local or remote.
V If the controller does not have an optional AUTO/MANUAL switch, inspect the
Regulator Module to determine that jumper J4 is inplace. (The jumper is
removed when the AUTO/MANUAL switch is installed.)
V Check the SPEED pot on the Control Station or Faceplate. First place the
POWER ON/OFF circuit breaker in the OFF position. Then open the main aĆc
line disconnect.
V Connect a voltĆohmmeter to the Regulator Module pin connectors Operator
Station inputs. Connect one lead to pin 20 (yellow). Connect the other pin to
28 (green). (Refer to Figure 7.1 for a Local Station and to Figure 3.8 for a
Remote Station.)
V For proper operation, the reading should be 5K ohms.
V Disconnect the VOM lead from pin 28 (green). Connect it to wire 26 (black).
V Turn the SPEED pot from 10 to 0. The resistance should vary from 5K to 10
ohms. If it does not, replace the pot.
FORWARD/REVERSE
switch malfunction.
V Examine Remote Operator Kit on Regulator Module, if used, for firm seating
and proper wiring and pin connections. (Refer to Figure 4.1.)
V Test FORWARD/REVERSE switch. Use basic technique outlined just above
for the START/STOP switch. Here test 67 (purple) against 56 (blue) and 71
(white) against 67 (gray).
7. Drive motor
does not
run, but M
contactor
and CR pull
up.
(Use this
procedure
only if conĆ
troller has
optional
Test Meter
Adapter Kit.)
No input signal from
SPEED pot.
V First check the main power supplies. This must be done with power applied
to the MinPak Plus controller.
V Connect one lead of voltĆohmmeter to test pin 357 on the Test Meter Adapter
Module.
V Connect the second lead to test pin 356 on the Module.
V The reading should be within the range of 10.8 to 11.5 VDC for normal
operation. a Next, remove the lead from pin 356. Place it on pin 456.
V The reading should be within the range of +16 to +28 VDC for normal
operation. a Next, remove the lead from pin 456. Place it on pin 471.
V The reading should be within the range of -16 to -28 VDC for normal
operation.
V If the proper readings are obtained, the power supplies may be assumed to
be operating correctly.
V If incorrect readings are obtained, replace the Regulator Module.
V Next, check the reference voltage input signal. (This changes in direct propĆ
ortion to an increase of SPEED pot voltage caused by a turning of the dial.)
V Connect one lead of a voltĆohmmeter to pin 357 on the Test Meter Adapter
Module.
V Connect the other lead to pin 826. Readings vary from 0 to +8.2 VDC,
depending on the set point of the SPEED pot dial and the position of the
FORWARD/REVERSE switch.
V If no voltage is noted between pins 357 and 826, check to see if jumper J4 on
the Regulator Module is properly placed/removed for the specific controller. (It
is to be in place, as factoryĆshipped, if there is no AUTO/MANUAL switch. It is
to be removed if there is an AUTO/MANUAL switch.)
V If the SPEED pot is functioning normally, and if the J4 jumper is placed/reĆ
moved, as necessary, replace the Regulator Module.
8. Drive motor
does not
run with M
contactor
picked up
and SPEED
pot properly
operating.
(Use this
procedure
only if conĆ
troller does
not have
optional
Test Meter
Adapter Kit.)
No output from Power
Cube.
V Examine armature wiring. First turn POWER ON/OFF circuit breaker to OFF
position. Then open main disconnect switch.
V Check armature wiring for loose connections.
V Turn aĆc power on again.
V Connect a voltĆohmmeter to terminals A1 and A2 on 2TB. (Refer to Figure 3.8.)
V Place the START/STOP switch in the START position.
V Increase the speed reference by turning the SPEED dial in the direction of 10.
V The reading across A1 and A2 should be 0 to 90 VDC for 115 VAC
controllers. It should be 0 to 180 for 230 VAC controllers.
V It no reading is obtained across A1 and A2, it may be necessary to replace
the Power Cube and/or the Regulator Module. In order to determine which,
read on.
DANGER
THE PROCEDURE DESCRIBED HERE IS PERFORMED WITH LIVE AĆC
VOLTAGE APPLIED TO THE CONTROLLER. USE ONLY ONE HAND TO
APPLY VOM LEADS/PROBES. KEEP YOUR OTHER HAND BEHIND YOU
AT ALL TIMES. DO NOT HOLD ONTO THE CONTROLLER FOR SUPĆ
PORT. PERSONAL INJURY MAY RESULT IF THESE PRECAUTIONS ARE
NOT TAKEN.