Rockwell Automation MinPak Plus DC Drives Kits User Manual
Page 10
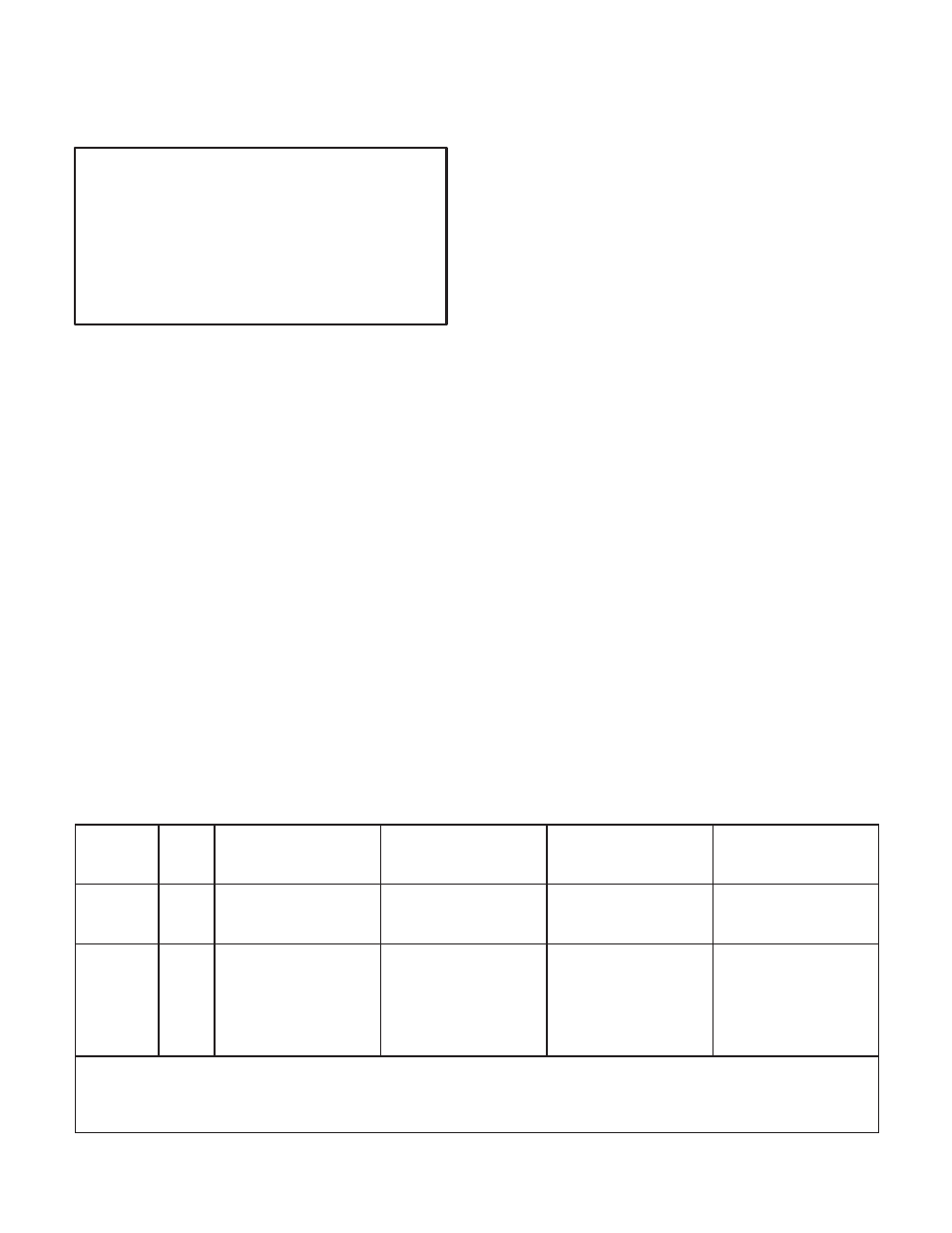
9
Guideline 11 Ċ The controller requires a singleĆphase
power supply that provides either 115 VAC or 230 VAC
at 50/60 Hz. If correct voltage is not available, it will be
necessary to install a transformer between the power
supply and the controller.
WARNING
DO NOT OPERATE THE REGENERATIVE MINĆ
PAK PLUS CONTROLLER ON POWER SUPĆ
PLIES WITH AVAILABLE SHORTĆCIRCUIT CURĆ
RENTS IN EXCESS OF 1000 AMPERES FOR
RATINGS OF 1 HP, OR LESS, AND 5000 AMĆ
PERES FOR RATINGS GREATER THAN 1 HP.
DAMAGE TO EQUIPMENT AND PERSONAL INĆ
JURY MAY OCCUR.
Guideline 12 Ċ Although autoĆtransformers may step
up and step down aĆc power supply voltage, they do not
isolate the drive system from the aĆc line. Users should
consider using an isolation transformer if the application
conditions warrant it.
Guideline 13 Ċ The plant power supply must be of suffiĆ
cient current capacity to support input current requireĆ
ments of the controller. (Refer to the drive's nameplate for
correct input power information.)
Guideline 14 ĊThe National Electrical Code requires
that a 2Ćpole, fused disconnect switch be installed on the
incoming aĆc line ahead of the controller to provide
branch circuit protection.
Fuses for this disconnect switch should be chosen from
Table 3.A. They should be dualĆelement. slow blow type,
or Class K5 or RK5.
Note that the standard POWER ON/OFF circuit breaker
is a doubleĆpole circuit breaker designed to provide
overcurrent protection for the internal Power Cubes conĆ
taining the power semiconductors. In addition, it is an
electrical disconnect. However, the N.E.C. or local codes
may still require that a fused disconnect device be used.
An existing branch switch may provide adequate protecĆ
tion.
It is recommended that the disconnect switch be placed
within easy reach of operating and maintenance personĆ
nel. Do not place it inside a surrounding enclosure since
cabinet doors may be locked. (Consult your local codes.)
Guideline 15 Ċ If an isolation or autoĆtransformer is
used ahead of the controller, the disconnect switch
should be placed on the aĆc power line between the powĆ
er source and the transformer primary. Again, use a
fused disconnect switch. (Do not use a circuit breaker
type switch because of the high inrush of transformer
equipment.) Refer to Table 3.A for sizes and types.
Guideline 16 Ċ An isolation transformer is not necesĆ
sary unless the application conditions require one. HowĆ
ever, its use provides distinct advantages. With an isolaĆ
tion transformer:
D Personal injury is guarded against should accidenĆ
tal contact be made with an electrical conductor
from the drive.
D AĆc power line disturbances, or transients, are miniĆ
mized by an isolation transformer, thereby reducing or
eliminating damage to other solidĆstate equipment
powerĆconversion components in the controller and
other userĆequipment on the same aĆc line.
D The transformer provides electrical isolation beĆ
tween the aĆc power lines and the drive motor.
Damaging currents may be eliminated in instances
where a dĆc output accidentally becomes
grounded in a unit where the aĆc electrical system
is grounded.
For detailed information, refer to Paragraph 3.10.
Guideline 17 Ċ If a threeĆconductor incoming aĆc line is
being used. it is necessary to connect the GND (green/
ground) wire to the terminal provided on the Chassis.
Ring type connectors are recommended. The user must
be sure that the ground wire is connected to the plant
ground at the source.
Guideline 18 Ċ If the controller is mounted in an encloĆ
sure that is not grounded, it is necessary to provide for
a ground. (Personal injury may result if this practice is not
followed.)
Table 3.A - TYPICAL WIRE. FUSE SIZES➀
HP
VAC
AĆC POWER
(min. size/insul.)
DĆC ARMATURE
(min. size/insul.)
DĆC DRIVE➁
(min. size/insul.)
DISCONNECT
FUSE SIZE➂
(amps)
1/4
1/3-1/2
3/4
115
115
115
No. 14 AWG 75
°
C
No. 14 AWG 75
°
C
No. 12 AWG 75
°
C
No. 14 AWG 75
°
C
No. 14 AWG 75
°
C
No. 12 AWG 75
°
C
No. 14 AWG 75
°
C
No. 14 AWG 75
°
C
No. 14 AWG 75
°
C
ă8
15
20
1/2
3/4-1
1Ć1/2
2
3
5
230
230
230
230
230
230
No. 14 AWG 75
°
C
No. 14 AWG 75
°
C
No. 12 AWG 75
°
C
No. 12 AWG 75
°
C
No. 10 AWG 75
°
C
No. ă8 AWG 90
°
C
No. 14 AWG 75
°
C
No. 14 AWG 75
°
C
No. 12 AWG 75
°
C
No. 12 AWG 75
°
C
No. 10 AWG 75
°
C
No. ă8 AWG 90
°
C
No. 14 AWG 75
°
C
No. 14 AWG 75
°
C
No. 14 AWG 75
°
C
No. 14 AWG 75
°
C
No. 14 AWG 75
°
C
No. 12 AWG 90
°
C
ă8
15
20
25
35
60
➀
Copper wire recommended.
➁
Permanent magnet motors do not require field supply.
➂
Fuses must be dualĆelement, timeĆdelay (slowĆblow) type, or U.L. Class K5 or RK5