Rockwell Automation MinPak Plus DC Drives Kits User Manual
Page 40
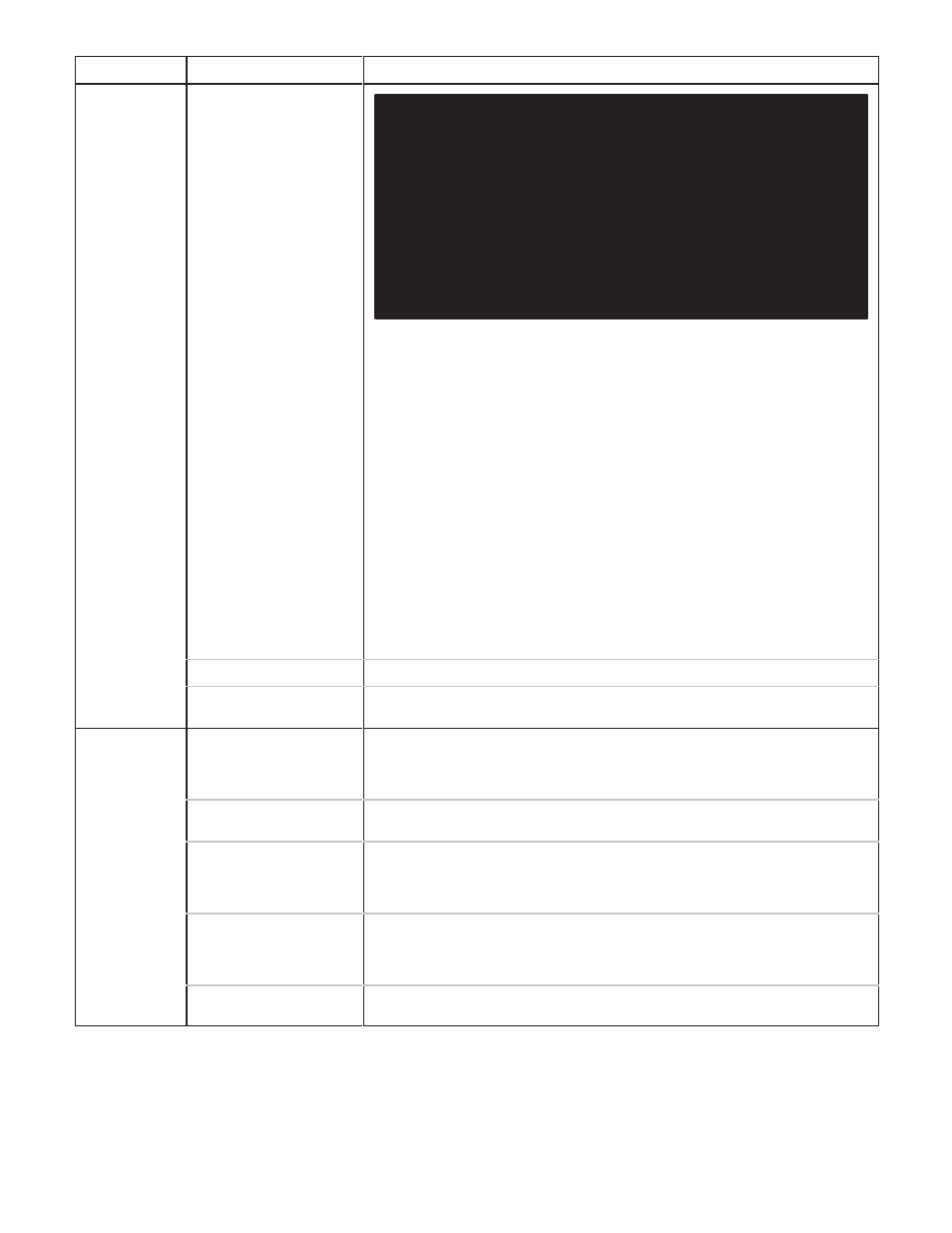
39
SYMPTOM
PROBABLE CAUSE
RECOMMENDED PROCEDURES
1. POWER
ON/OFF
circuit
breaker on
controller
trips when
power is
Applied.
Incorrect wiring connecĆ
tions to controller, from
controller to motor. in moĆ
tor.
V Remove aĆc power at disconnect breaker.
V Remove leads to L1, L2, A1, A2 and. if used, F1, F2, on incoming side of
controller's 1TB, 2TB and 3TB. (Refer to Figure 3.8.)
V Put POWER ON/OFF circuit breaker in ON position.
V Check for a ground condition at L1/181, L2/182, A1, A2, F1 and F2. Do this at
controller (internal side of 1TB, 2TB and 3TB. If a ground is discovered,
check wiring connections on POWER ON/OFF circuit breaker. Also check
connection to Power Cube and motor field terminals F1 and F2.
V If no ground exists, examine the controller Chassis and Cover for loose wires
and/or foreign objects.
V If no ground exists and if no foreign objects are discovered, reconnect the
incoming conductors A1, A2 and, if used, F1 and F2. Then check for grounds
at these terminals.
V If a ground is found, it is in the conductors to the motor or in the motor itself.
V Disconnect the motor from the conductors at the drive motor.
V Test A1, A2, F1 and F2 conductors for a ground. (If one exists, examine
connections and insulation for areas where shorts could occur.)
V If no grounds are found in the conductors, check the motor for a ground
condition. If a ground is located here, examine and/or replace the motor, as
necessary.
Short in Power Cube.
V Replace Power Cube.
Short in Field
Supply Kit.
V Replace Diode Bridge in Field Supply Kit. Inspect wires and connections to
Field Supply Kit. Replace all damaged wires and connectors.
2. Drive motor
does not
start
Main aĆc line disconnect
not closed or fuse blown
or no power applied
ahead of disconnect
V Check disconnect switch, fuses in it, and voltage on line.
Drive interlocks preventing
operation.
V Verify that all userĆinstalled interlocks are in a state (physical condition and
wiring connections) to allow a start.
Drive motor thermostat
wires not connected on
controller terminals 32 and
132 on 2TB
V Check connections to thermostat: at drive motor P1, P2; at controller 32, 132.
V Check for open thermostat inside motor. Make a resistance check of
thermostat. (It should read a short, or low resistance, if it is closed.)
External overload wires
not connected on controlĆ
ler terminals 32 and 132
on 2TB.
V Check connections to external overload.
V Check for open overload. Make a resistance check to overload. (It should
read a short, or low resistance, if it is closed.)
DĆC circuit breaker (3CB)
open.
V Must open Cover to reset Check for motor ground conditions before
resetting.
DANGER
IF CIRCUIT BREAKER HAS TRIPPED, USER MUST REMOVE THE COVĆ
ER FROM THE DRIVE AND DETERMINE IF A FIELD SUPPLY KIT IS
PRESENT. (SEE FIGURE 4.5.) IF FIELD SUPPLY KIT IS PRESENT, THE
FIELD SUPPLY KITAND ITS WIRING MUSTBE INSPECTED FOR DAMĆ
AGE. AFTER CLOSING THE COVER AND REĆAPPLYING POWER TO THE
DRIVE, THE FIELD VOLTAGE MUST BE REĆCHECKED FOR PROPER
VOLTAGE AT MOTOR TERMINALS F1, F2. IF THIS VOLTAGE IS BELOW
90% OF THE FIELD VOLTAGE SPECIFIED ON THE MOTOR NAMEĆ
PLATE, THE DRIVE MUST NOT BE STARTED UNTIL PROPER VOLTAGE
IS OBTAINED. FAILURE TO FOLLOW THIS PROCEDURE COULD REĆ
SULT IN OVERSPEEDING THE MOTOR AND/OR THE MACHINERY
COUPLED TO THE MOTOR SHAFT AND POSSIBLE FATAL INJURY.