Rockwell Automation MinPak Plus DC Drives Kits User Manual
Page 38
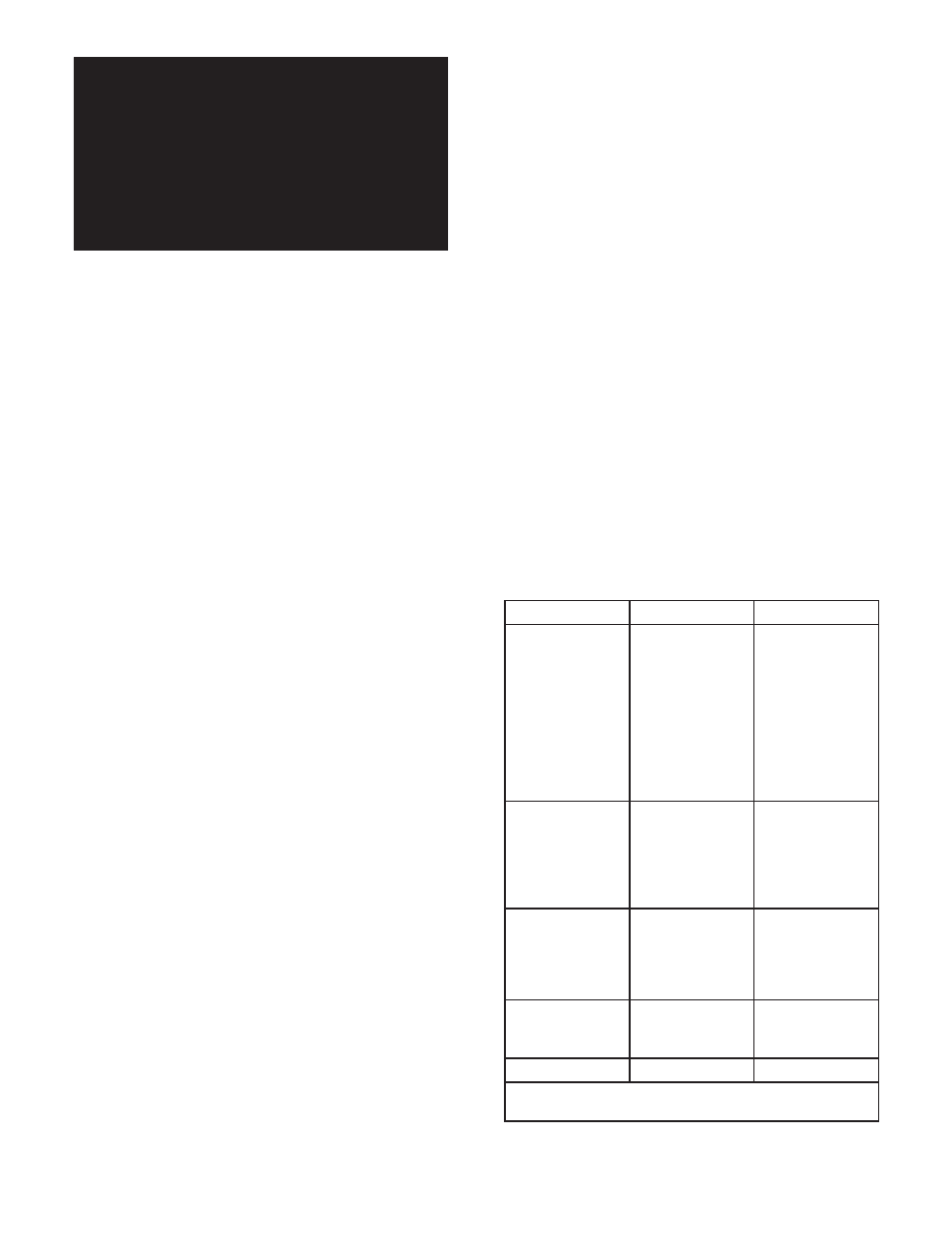
37
DANGER
CONTROLLER EQUIPMENT IS AT LINE VOLTĆ
AGE WHEN AĆC POWER IS CONNECTED TO
THE POWER UNIT IN THE REGENERATIVE MINĆ
PAK PLUS CONTROLLER. THUS AĆC POWER
MUST BE REMOVED FROM THE UNIT BEFORE
IT IS SAFE TO TOUCH THE INTERNAL PARTS
OF THE REGENERATIVE MINPAK PLUS. PERĆ
SONAL INJURY MAY RESULT UNLESS POWER
IS REMOVED.
In addition to stepĆbyĆstep troubleshooting procedures,
there are some generalized comments that should be
kept in mind at all times. These may be divided into wirĆ
ing errors (Par. 7.1), incoming aĆc line problems (Par.
7.2), motor problems (Par. 7.3) and mechanical probĆ
lems (Par. 7.4).
7.1 Wiring Errors Ċ The single most common problem
preventing normal dĆc drive operation is incorrect wiring
within a system. A maintenance person should spend at
least 5 minutes carefully looking over the wiring before
taking active steps involving tests and replacement. ReĆ
member that a loose or grounded wire can occur in a
controller that had previously been functioning correctly
if initial wiring techniques were poorly performed.
For those not familiar with proper Regenerative MinPak
Plus controller wiring, other Sections in this manual may
be consulted. For more complex problems, Section 6
may be used to uncover wiring problems in the optional
Modification Kits.
7.2 AĆC Line Problems Ċ The following are typical
problems located on the incoming aĆc line:
D AĆc line voltage incorrect for the specific controller,
which may operate on 115 or 230 VAC.
D Main disconnect switch contains fuses improperly
rated for the drive. (The fuses must be large enough
to prevent nuisance tripping yet small enough to
protect the circuit and equipment on the circuit.)
Refer to Table 3.A.
D AĆc conductors must be of adequate size for the
application. Refer to Table 3.A.
D If an isolation transformer is used, it must be sized
according to the requirements of the drive system.
The transformer itself must be wired for the correct
output voltage (115/230VAC) in relation to the
Regenerative MinPak Plus controller.
7.3 Motor Problems Ċ Do not overlook the possibility
that the malfunction may be located in the drive motor.
The following steps should become part of a troubleĆ
shooting routine:
D Recheck all motor connections for firmness and
correct identification.
D Check that no obvious grounds have occurred on
any of the wires. However, do not use a megger
when checking for grounds unless the motor wiring
to the Regenerative MinPak Plus controller is
completely disconnected.
D A voltĆohmmeter (VOM) may be used for ground
checking without disconnecting conductors to the
Regenerative MinPak Plus controller.
D Check the field windings for open or short condiĆ
tions.
D Check continuity through the armature and
brushes. Use the A1 and A2 wires at the controller
as test points.
7.4 Mechanical Ċ It may be that the malfunction is a
simple mechanical problem. The load on the drive motor
may be too large, or it may have too high an inertia. The
results are long stopping times and currentĆlimit starting
demands. Thus, the freedom of motion of the load device
should be considered.
7.5 Controller Malfunctions Ċ The following lists presĆ
ent an organized troubleshooting sequence based on a
symptom/probable cause/suggested procedure apĆ
proach. It develops from the most simple, obvious malĆ
function to more complex ones.
Note that Reliance Electric color codes the wires to aid
the identification of pin numbers, that is. locations. Table
7.A is a listing of these numberĆcolor combinations.
These colors will be helpful in the following troubleshootĆ
ing procedures. They may also be used with Figure 7.1,
where the wiring diagram for a Local Operator Control
station is shown. Since the insulation colors a user
chooses for a Remote Station cannot be predicted, only
pin numbers are shown in Figure 7.4. However, the colĆ
ors are valuable when consulting schematics in this
manual.
Table 7.A - COLOR CODING SYSTEM
COMPONENTS
NO. ➀
COLOR
Local Operator
Switches
32
38
35
326
126
26
65(71)
66(56)
39(67)
67
RED
BROWN
ORANGE
GREEN
YELLOW
BLACK
WHITE
BLUE
PURPLE
GRAY
Potentiometer
28
26
20
57
71
99
GREEN
BLACK
YELLOW
READ
BROWN
ORANGE
Wire Harness
M Contactor
-
38
38
40
36
BLUE
GRAY
BROWN
ORANGE
GREEN
Thermostat
Harness
32
132
232
RED
ORANGE
BLACK
Auxiliary M
39(38)
YELLOW
➀
Numbers in parentheses are for the Regenerative
MinPak Plus when they are different from the MinPak Plus.