Rockwell Automation MinPak Plus DC Drives Kits User Manual
Page 13
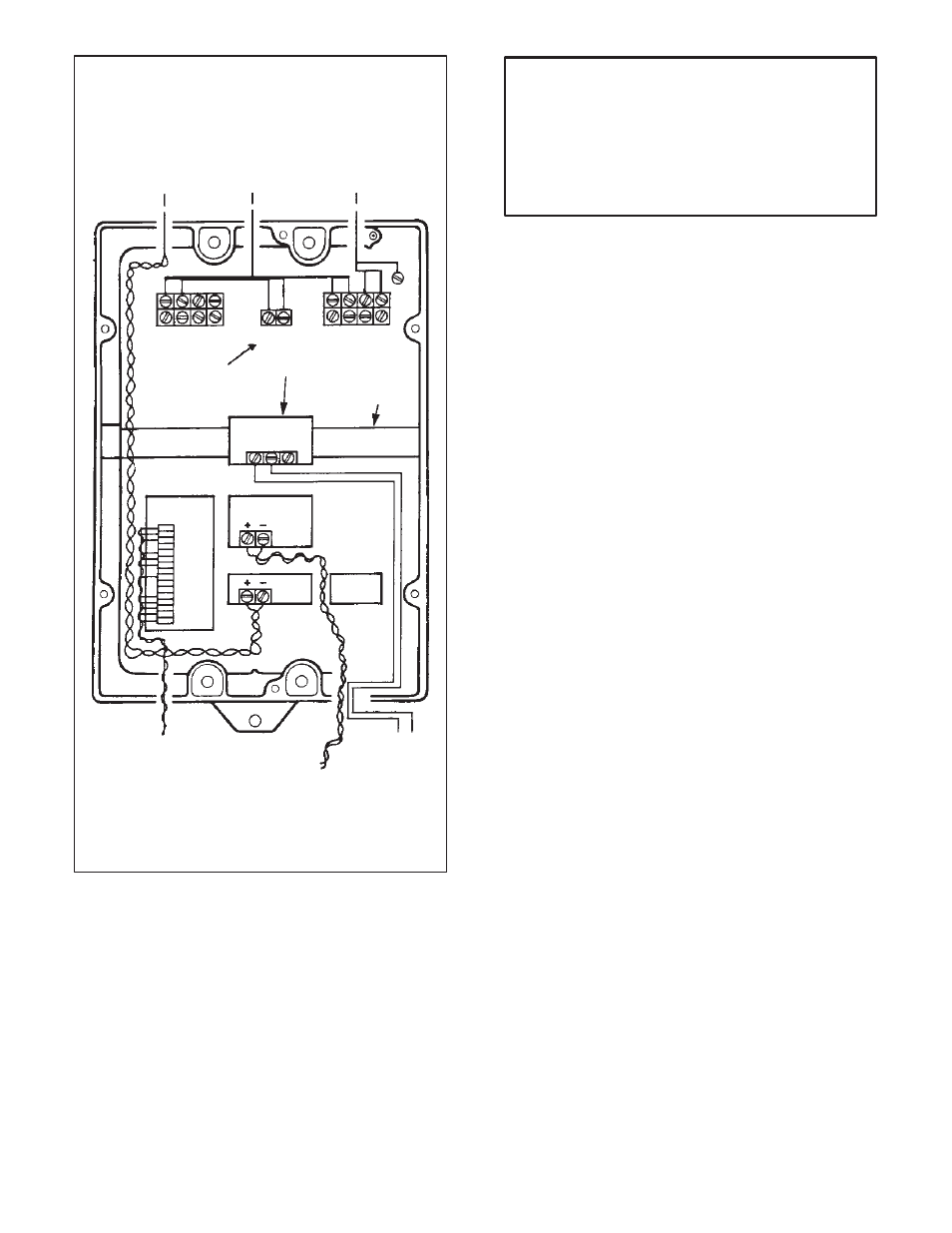
12
1/2"-14 thread
3/4"-14 thread
3/4"-14 thread
1/2"-14 thread
1/2"-14 thread
Remote Operator
Station
input wires
Input
for
Process Control
or
Auto Reference
Output
from
Auxiliary
M
Conductor
Tach
Feedback
Auxiliary
Bracket
Auxiliary M
Module
Field wiring
only if Kit
used.
Tach
input
wires
DĆc
output
conductors
AĆc
output
conductors
Figure 3.7 - Chassis Wells, Wire Routing
3.5.2 DĆC Wiring Ċ The next wires to be drawn into the
controller's Chassis are the dĆc armature control conducĆ
tors. If the optional Field Supply Kit is being used, the
field wiring conductors will also be drawn in. The motor
thermostat conductors are to be drawn in, too. All use the
same conduit.
Make sure that Guideline 10 has been considered. Wire
according to Figure 3.8.
WARNING
DO NOT ALLOWCONDUCTORS TO GROUND
ON THE CHASSIS OR CONDUITS. CHECK INĆ
TEGRITY OF ALL WIRE INSULATION BEFORE
DRAWING. REMOVE ONLY ENOUGH INSULAĆ
TION TO MAKE A FIRM TERMINAL CONNECĆ
TION. PERSONAL INJURY COULD RESULT IF A
BARE WIRE TOUCHES THE CHASSIS.
Field Supply wiring should also be performed now. It is
standard on 2, 3 and 5 hp controllers and optional on
lower ratings. A Field Supply Kit must be installed in the
controller to accept this wiring.
Motors with dualĆvoltage shunt fields should be conĆ
nected for the higher voltage. Connect:
D 90Ćvolt armature/100Ćvolt field
D 180Ćvolt armature/200Ćvolt field
D For half wave connections, refer to Figure 6.12
After wiring, examine all connections to determine that
they are correctly made at both ends. Confirm wire idenĆ
tification. Examine the firmness of the connections.
3.6 Thermal Overload Wiring Ċ The controller is
shipped without a jumper between terminals 32 and 132.
The motor thermostat or an external overload must be
connected to these terminals to meet local code requireĆ
ments.
NOTE: An external overload device must be connected
between terminals 32 and 132. The drive will not start
without it.
3.7 Tachometer Feedback Ċ The Regenerative MinĆ
Pak Plus controller may be connected to a dĆc tachomeĆ
ter. An aĆc tachometer cannot be used.
Not all drives require the use of a tachometer. This ParaĆ
graph should be read and followed only if the specific
system requires one. If your drive system does not use
a tachometer, proceed to Paragraph 3.8.
The following procedures assume that Guideline 10 has
been considered. These procedures are limited to preĆ
paring the incoming signal wires and wiring them at
the tachometer.
Note that a twisted pair signal wire must be used for the
tachometer feedback circuit. It is specified in Table 6.C.
The cable run between the motor and the controller must
be through a dedicated conduit. Under no circumĆ
stances attempt to use the aĆc or dĆc conduits.
Wire according to Figure 3.8 and the following proceĆ
dure.
Step 1 Ċ Connect the tachometer wires to the terminal
strip on the Module Plus (+) is the left side, minus (-) the
right. Do not strip off more than 1/8 inch (3 mm) of insulaĆ
tion since shorts occur at exposed points. Maintain the
twist as long as possible.
Step 2 Ċ Locate the black pigĆtail jumper on the
Tachometer Module. It is to be placed on one of eight
pins on the Module. Exactly which depends on the voltĆ
age scaling factor. On the motor's nameplate, find the
base speed (rpm). On the tachometer's nameplate,find
the output voltage per 1000 rpm.