Rockwell Automation 1771-QC , D17716.5.25 SER/B SERVO POS User Manual
Page 98
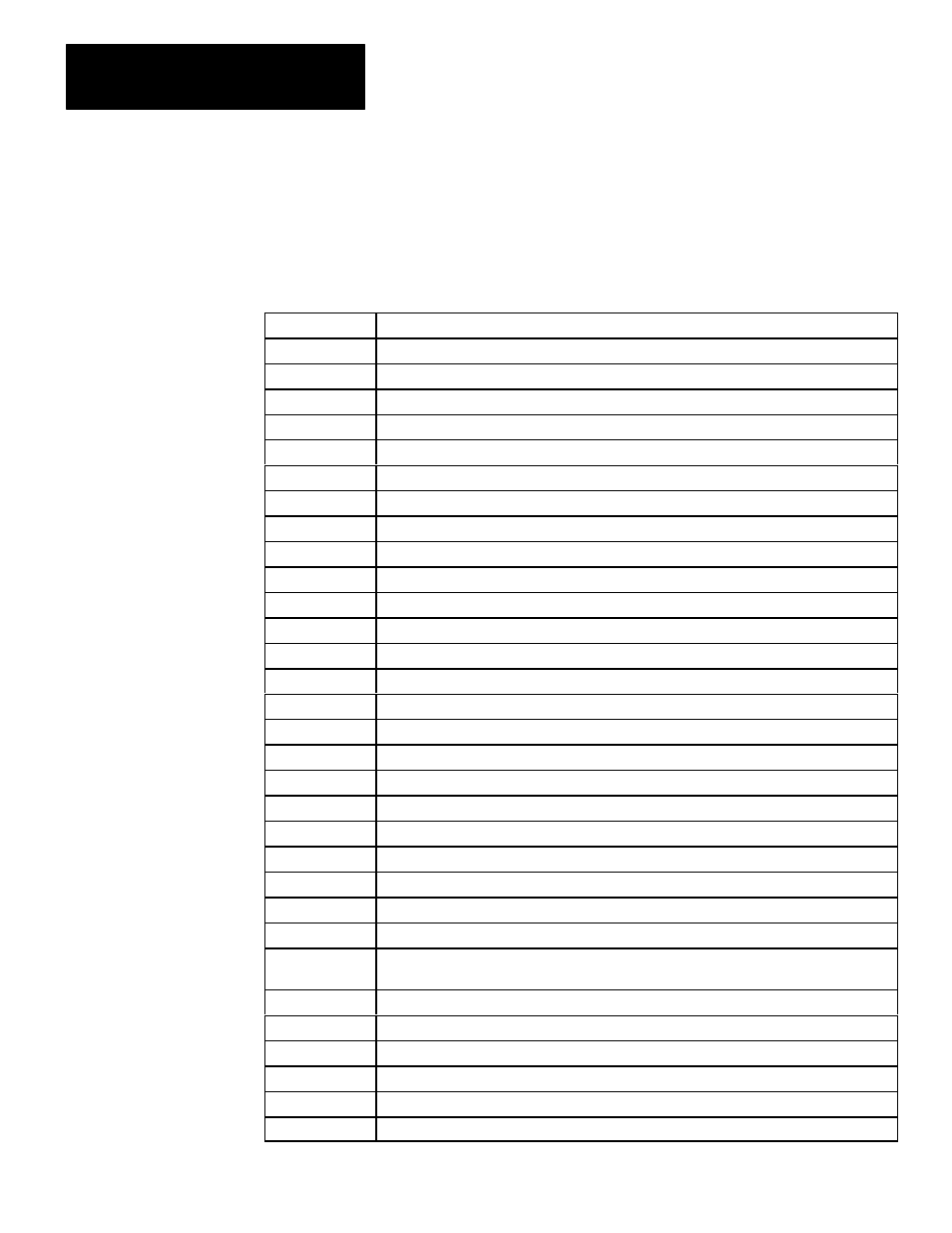
Formatting and Interpreting Data Blocks
Chapter 7
7Ć16
Use the block pointer and word pointer to identify the location of the
problem. Then use the error code to determine the nature of the problem.
Table 7.A
Diagnostic Code Definitions
Code
Definition
01
Invalid block identifier.
02
NonĆBCD number entered.
03
Invalid bit setting unused bits must be zero.
04
MS metric only" bit set in inch format.
05
Overflow: Converted data is too large for internal registers.
06
Can only change feedback multiplier from a powerĆup rest.
07
Invalid axes used" programmed.
08
Invalid write block address points.
09
Invalid feedback resolution (<0.00001 in. or 0.0001 mm).
10
Invalid feedback multiplier bit setting.
11
(Counts per rev) x (feedback mult) x (encoder lines mult)>32767 decimal.
12
D/A voltage too small for selected rapid rate.
13
Initial gain too small for selected rapid rate.
14
Rapid rate entered exceeds 250 kHz maximum input frequency.
15
Rapid rate entered exceeds 1/2 revolution of encoder/2.4ms.
16
Programmed velocity >rapid rate.
17
Invalid velocity exponent programmed.
18
Entered speed is too small for selected feedback resolution.
19
Accel velocity or decel value is too small for selected feedback resolution
20
Not as many valid SMCWs as there were moves declared in the MCW.
21
Local parameters or run at velocity not allowed for a preset or dwell.
22
Invalid preset position (must be an absolute position).
23
Invalid dwell time (must be
≥
20ms).
24
Escape move block can only have 1 move declared.
25
Invalid escape move block; only moveset blocks identified in the parameter block can be
escape move blocks.
26
Cannot program a preset or dwell as an escape move.
27
A valid nextĆmoveset pointer could not be found.
28
Command results in overflow of offset accumulator.
29
Attempted context switch with dual meaning bits on.
30
Attempted context switch while axis is commanding motion.
31
Manual mode only bit(s) on while in auto mode.