24 description of operation – Rockwell Automation 1557 MEDIUM VOLTAGE AC DRIVE User Manual
Page 42
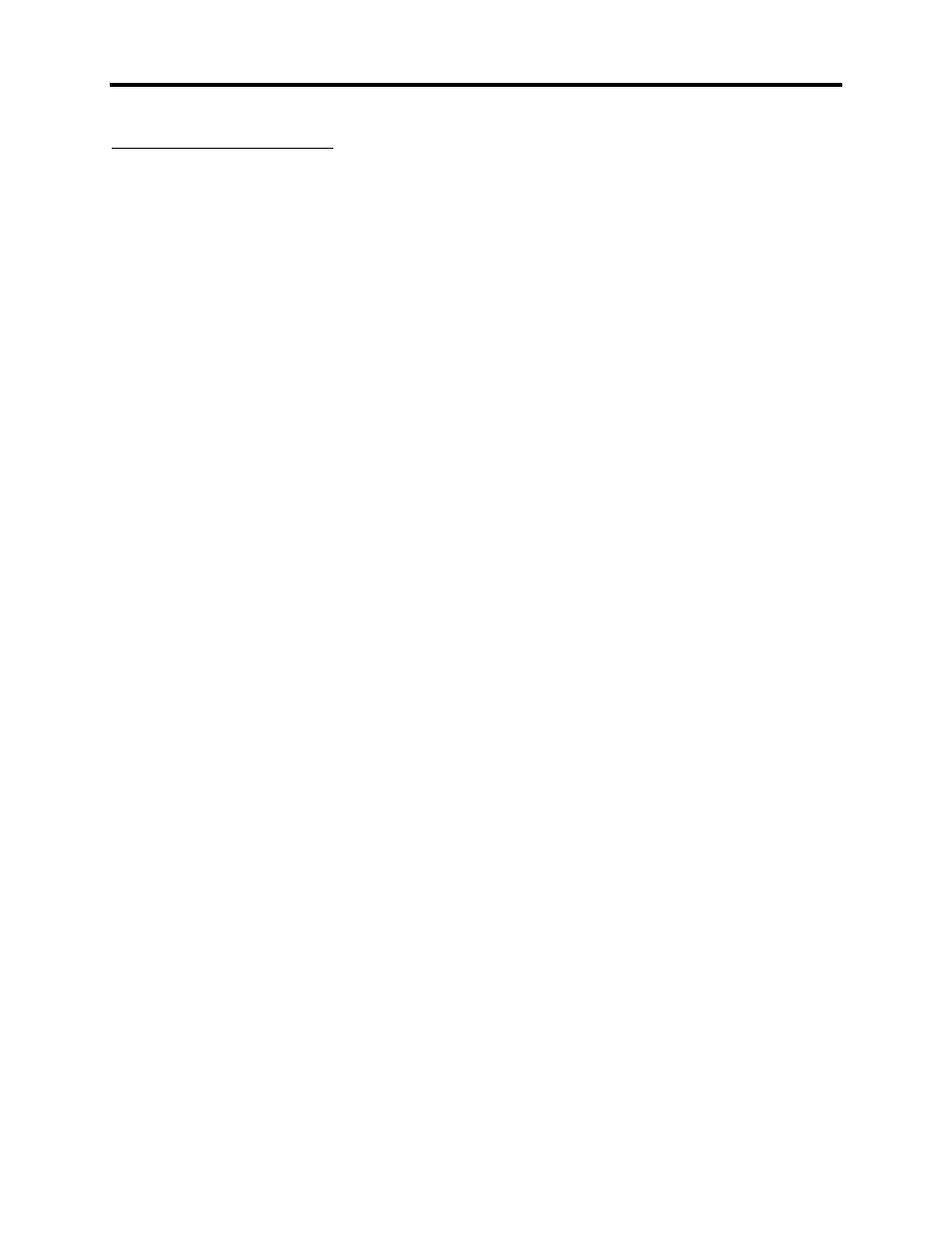
5-24
DESCRIPTION OF OPERATION
1557-UM050F-EN-P – June 2013
Machine Converter Protection
Except for the hardware overcurrent and dc link overvoltage detection, the machine converter protection
is implemented entirely in software. Adjustable parameters specifying the trip level and time delay are
provided for each fault. The motor current and voltage feedback are obtained as described in the motor
model section. The motor speed feedback is derived by measuring the stator frequency and adding the
calculated slip frequency as described in the section on speed control.
For all faults except motor overload, if the measured voltage, current, or speed exceeds the specified trip
level for the specified time interval, the corresponding fault bit is set in one of the fault words and the
master fault bit is set in Logic Status. For the detection of overload faults, the amount by which the
square of the motor current exceeds a threshold level is integrated with time. An overload fault is
declared if the output of the integrator exceeds the trip level calculated from the specified overload trip
level and time. An overload warning is issued when the I
2
t level reaches half the trip level.
The response to a machine converter fault is exactly the same as the response to a line converter fault.
The hardware overcurrent and dc link overvoltage are special cases in that the fault detection is
performed by hardware but the time delay is performed by software. The detection of the dc link
overvoltage is implemented in hardware because a very fast response is required. The hardware fault
detection responds to instantaneous values rather than average values as the software fault detection
does. The hardware motor overcurrent detection is provided because it is required for dc link overcurrent
detection on the line converter, and both converters use identical Drive Control Boards.