54 troubleshooting – Rockwell Automation 1557 MEDIUM VOLTAGE AC DRIVE User Manual
Page 296
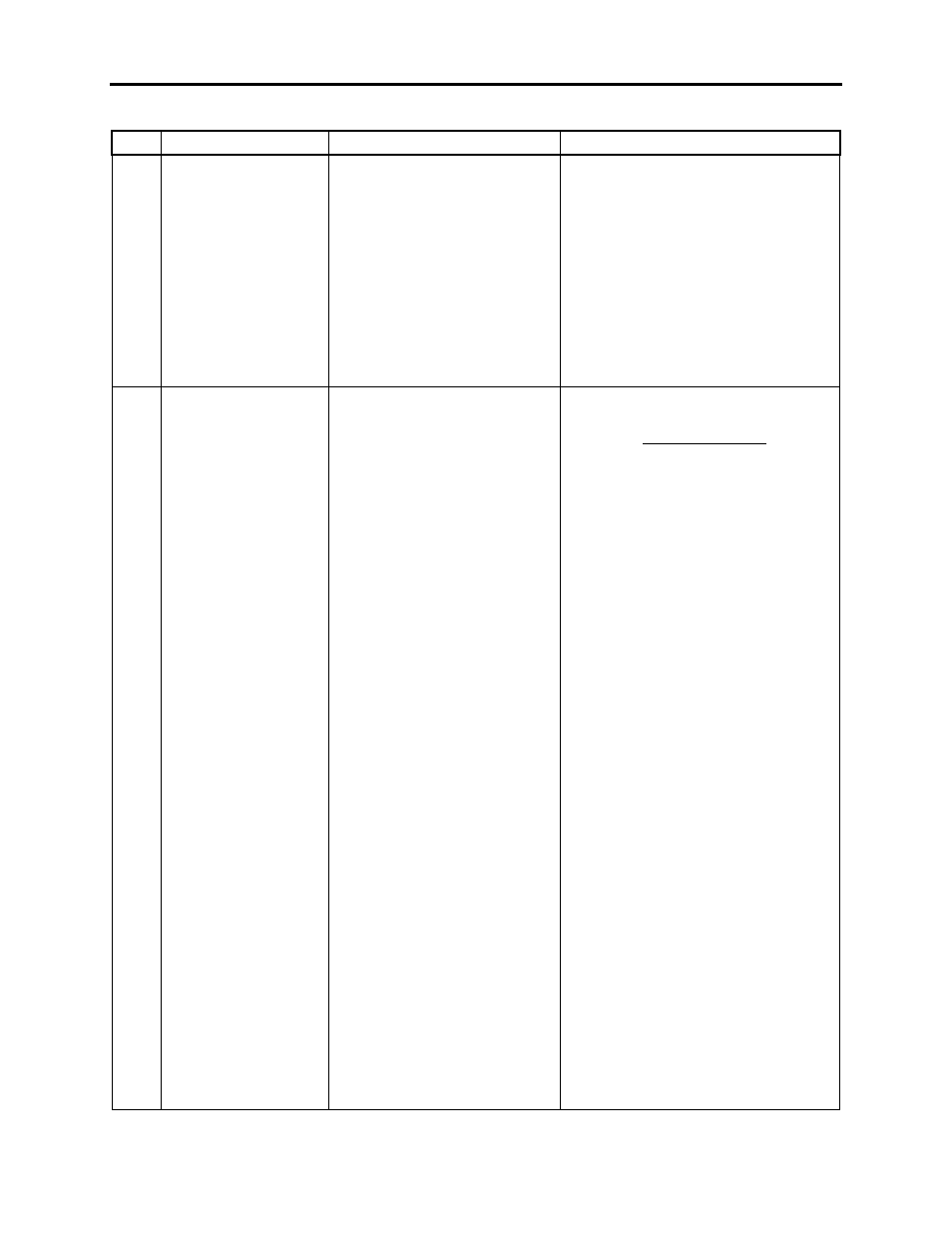
10-54
TROUBLESHOOTING
1557-UM050F-EN-P – June 2013
#
FAULT / ALARM
PROBABLE CAUSE
RECOMMENDED ACTION
33
NO V
DC
FEEDBACK
1. HARDWARE
1A.
CHECK THE FUSES ON THE MOV‟S OF
DC LINK SURGE SUPPRESSOR
NETWORK (IF PRESENT)
B. CHECK THE LINE SIDE VOLTAGE FEED
BACK BOARDS FOR ANY DAMAGED
COMPONENTS AND REPLACE IF
NECESSARY
C. CHECK THE CABLING ON THE
VOLTAGE FEEDBACK BOARDS FROM
THE DC LINK
D. CHECK THE RIBBON CABLES FROM
THE DRIVE CONTROL BOARD LINE-
SIDE TO THE VOLTAGE FEED BACK
BOARDS
E. DISABLE THE NO VDC FDBK ALARM
34
STALL FAULT
1. MOTOR/LOAD IS JAMMED
2. MOTOR IS FREE
1A. CLEAR THE JAM
2A. CHECK WHETHER THE DRIVE IS
FITTED WITH TACHOMETER OPTION
OR NOT. WITHOUT TACHOMETER,
THE STALL FAULT IS DETECTED
WHEN THE DRIVE REACHES THE
COMMANDED SPEED AND THE
MOTOR FLUX REMAINS BELOW THE
LEVEL SPECIFIED BY PARAMETER
FLUX MINIMUM. ENSURE THAT THE
MOTOR IS NOT SPINNING AT A HIGHER
SPEED THAN THE COMMANDED
SPEED OR THE MOTOR IS ROTATING
IN THE OPPOSITE DIRECTION.
IF THE STALL FAULT OCCURS DURING
START UP, THEN THE TORQUE
COMMAND MIGHT HAVE BEEN SET
TOO LOW. CHECK THE VALUE IN THE
PARAMETER TABLE AND INCREASE
THE VALUE (APPLICABLE FOR CASES
WITHOUT A TACHOMETER).
B. WITH THE TACHOMETER OPTION, THE
STALL FAULT IS INDICATED ONLY
WHEN THE SPEED IS ZERO AND THE
DRIVE REACHES THE TORQUE LIMIT,
AND IS BELOW 1 HZ AND THE STALL
TIME HAS EXPIRED, ENSURE THAT
THE TACHOMETER IS FUNCTIONAL.
C. CHECK THE MACHINE SIDE
CONVERTER CIRCUIT FOR ANY
FAILED DEVICES (GTO).
D. IF THE STALL FAULT OCCURS DURING
START UP, THEN THE TORQUE
COMMAND 0 OR 1 MIGHT HAVE BEEN
SET TOO LOW. CHECK THE VALUE IN
THE PARAMETER TABLE AND
INCREASE THE VALUE (APPLICABLE
FOR CASES WITHOUT A
TACHOMETER).
E. IF THE STALL FAULT OCCURS DURING
RUNNING, THEN THE TORQUE LIMIT
MOTORING MIGHT BE LOW, CHECK
AND INCREASE THE VALUE TO SUIT
THE APPLICATION.
F. EXCITATION LIMIT PARAMETER SET
TOO LOW.
G. INCREASE THE MOTOR STALL DELAY.
H. CHECK THE OUTPUT CAPACITORS.