12 installation – Rockwell Automation 1557 MEDIUM VOLTAGE AC DRIVE User Manual
Page 198
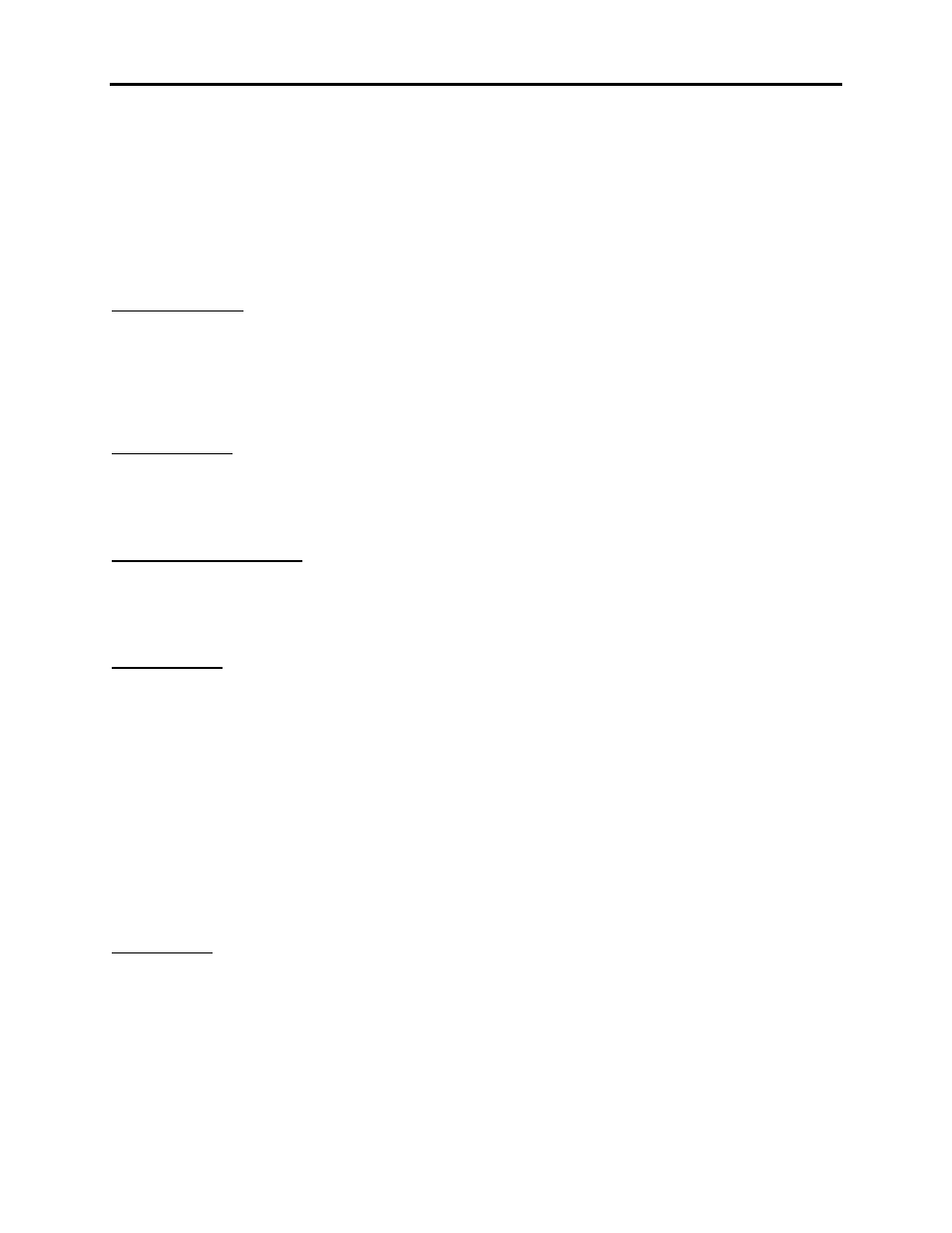
8-12
INSTALLATION
1557-UM050E-EN-P – June 2013
The wire sizes must be selected individually, observing all applicable safety and CEC or NEC regulations.
The minimum permissible wire size does not necessarily result in the best operating economy. The
minimum recommended size for the wires between the drive and the motor is the same as that used if a
main voltage source connection to the motor was used. The distance between the drive and motor may
affect the size of the conductors used.
Consult the wiring diagrams and appropriate CEC or NEC regulations to determine correct power wiring.
If assistance is needed, contact your local Rockwell Automation Sales Office.
Physical Location
The drive is designed for front access and should be installed with adequate and safe clearance to allow
for total door opening. The back of the unit may be placed against a wall and several units may be set
end to end. In special cases where floor space is limited and the unit is not against a wall, certain cabinet
sections may be placed back to back. This requirement must be stated in the specifications in order to
mechanically alter the drive.
Ground Bus-Bar
Drives which are delivered in two or more sections for ease of handling will require that the ground bus-
bar which runs the entire length of the drive on the inner back side, to be re-connected. When the
sections are brought together the ground bus-bar's from each section are to be bolted together.
Power and Control Wiring
Drives which are delivered in two or more sections, for ease of handling, will require that the power and
control wiring be re-connected. After the sections are brought together, the power and control wiring is to
be re-connected as per the schematic drawings provided.
Control Cables
Control cable entry/exit should be located near the terminal block 'TBC' -the customer's connections are to
be routed along the empty side of the TBC terminals. These terminals are sized to accept a maximum
AWG #14 wire gauge. The low voltage signals (includes 4-20mA) are to be connected using twisted
shielded cable, with a minimum AWG #18 wire gauge.
Of special concern is the tachometer signal. Two tachometer inputs are provided to accommodate a
quadrature tachometer (senses motor direction). The tachometer power supply is isolated and provides
+15 Volts and a ground reference. Many tachometer outputs have an open collector output, in which case
a pull-up resistor must be added to ensure that proper signals are fed to the system logic.
IMPORTANT: Low voltage signals are to be connected using twisted shielded cable with the shield
connected at the signal source end only. The shield at the other end is to be wrapped with electrical tape
and isolated. Connections are to be as shown on the drawings provided.
Drive Cooling
Proper fan operation is essential to the performance of the drive. At installation, ambient temperature must
not exceed 40 degrees Celsius. Check that all drive fans are operating and that there are no external
hindrances to airflow.