Vicor VI-J00 Family DC-DC Converters and Configurable Power Supplies User Manual
Page 85
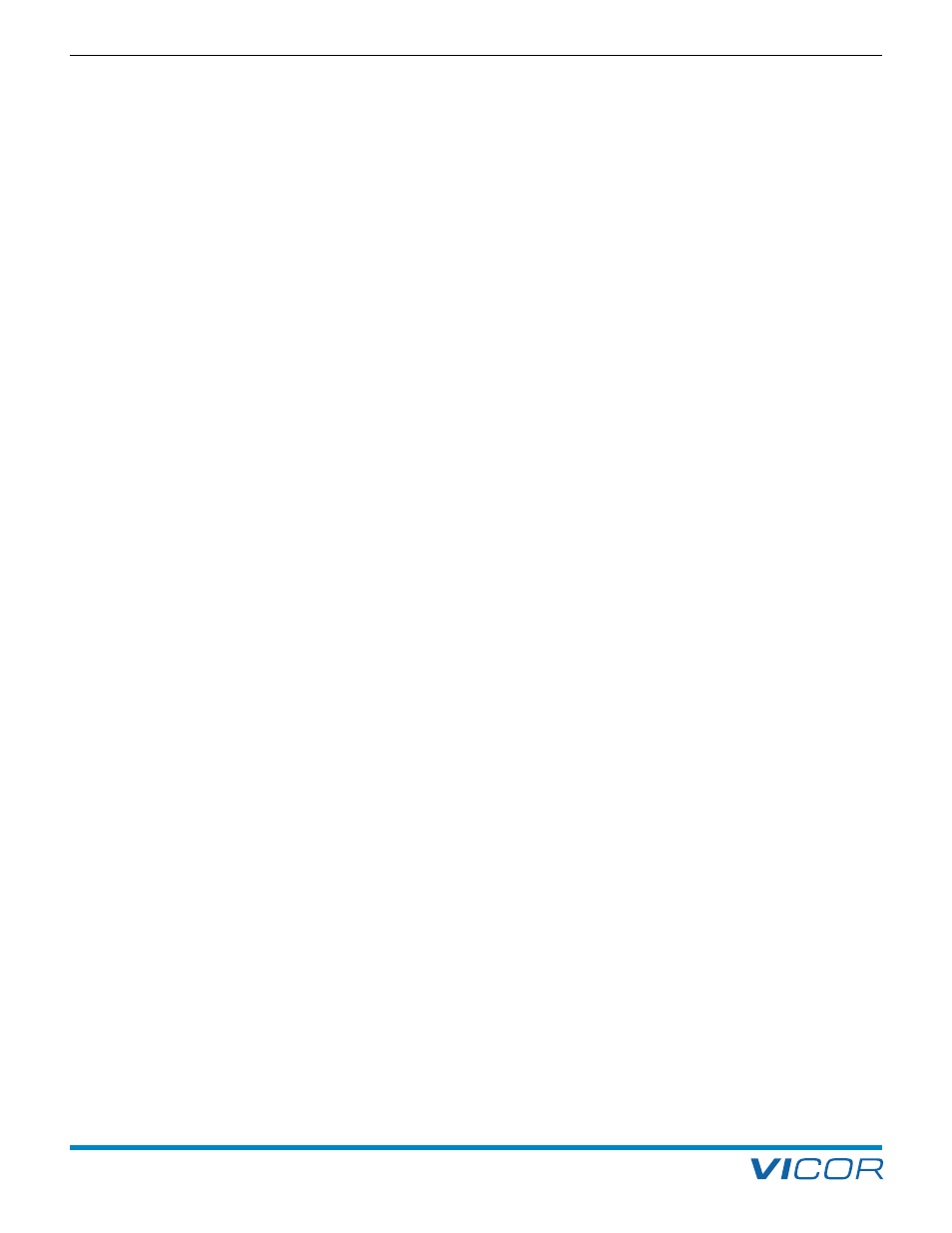
Design Guide & Applications Manual
For VI-200 and VI-J00 Family DC-DC Converters and Configurable Power Supplies
VI-200 and VI-J00 Family Design Guide
Rev 3.5
vicorpower.com
Page 84 of 98
Apps. Eng. 800 927.9474
800 735.6200
23. Recommended Soldering Methods,
Tin Lead Pins, and InMate Sockets
Hand Soldering. Before soldering, make sure that the
PCB is clean and free of debris, chemical residue, or liquid.
It is not recommended that additional flux other than
what is contained in the solder be used during soldering
as it potentially leaves a residue that cannot be removed
without potentially damaging or compromising the power
module. Also, the presence of these residues themselves
on the modules may cause harm or improper operation.
The pins on Vicor modules are optimized in design for
providing a low-resistance electrical connection. The final
mounting scheme for any module should be designed so
as to minimize any potential mechanical stress on the pins
and solder joints. Modules with heat sinks or modules used
in systems that are subject to shock or vibration should
use standoffs to minimize stress on the pins. Tin / lead
pins are specifically designed for soldering applications
while gold pin options are specified for socketed
applications (see SurfMate or InMate mounting systems).
It is not recommended that discrete wires or connectors
be soldered directly onto a module.
Also necessary for a good solder connection is pin
protrusion from the PCB. It is not possible to create a
good solder joint without some protrusion of module pins
from the PCB. If the PCB is too thick to allow good pin
protrusion, consider using Vicor module accessories such
as sockets to allow proper mounting.
Before soldering, the module should be mechanically
affixed or immobilized with respect to the PCB to ensure
no movement during the soldering process. The standoffs
can be used for this process.
Vicor power modules contain two types of pins: power
pins (which deliver the power to the load and are typically
sized according to the rated output current) and signal
pins (which typically carry very little current and are of a
uniform size across a given product family). The larger the
pin, the more soldering time required to form an
adequate connection. In addition to the sizing of the pin
the time required to create a robust connection will vary
depending on several parameters:
1. PCB Thickness. The thicker the printed circuit board is,
the more heat it is able to dissipate, and thus it will
require more soldering time.
2. Copper Trace Area. Power pins require large copper
traces to minimize resistive power losses in carrying
the power to the load. Since the copper tends to
conduct heat rather well, the actual size of these
copper traces directly affect the amount of time
necessary to heat the PCB socket.
3. Copper Trace Thickness. As above, the thickness of
the copper trace is a function of output current of the
module, and has a direct impact on the amount of
soldering time. Typically, PCB copper thickness is
specified in terms of weight per square foot, typically
2 oz. or 3 oz. copper for current-carrying planes.
4. Soldering Iron Power. A higher power soldering iron
can source more heat and thus take less time to heat
a PCB trace. When a soldering iron is heating a point
on the board, everything that is adjacent to this point
is being heated as well, including the Vicor power
module. A large copper trace, because it conducts
heat very well, will exhibit less of a thermal gradient
and thus a low-power soldering iron will have to heat
the whole trace to a higher temperature before the
area close to the iron is hot enough to flow solder.
Because the trace and board are both dissipating and
conducting thermal energy, some irons may not have
enough power to heat a trace to the temperature that
will allow proper soldering.
5. Tip Temperature. Typical 63 / 37 solder melts at 392°F
(200°C). A higher tip temperature will bring the barrel
and pin above the melting point of solder faster.
However, a higher tip temperature may cause damage
to the pad, printed circuit board, or module pin.
6. Type of Solder. The actual melting point of the solder
varies depending on the type of solder used and
affects the necessary temperature of the pad and pin
for flow. Vicor recommends 63 / 37 SnPb solder for
use on Vicor power modules.
7. Tip Size. A larger tip will be able to heat a larger
surface area, thus lowering soldering time.
SOLDERING PROCEDURES