Thermal and module mounting considerations – Vicor VI-J00 Family DC-DC Converters and Configurable Power Supplies User Manual
Page 63
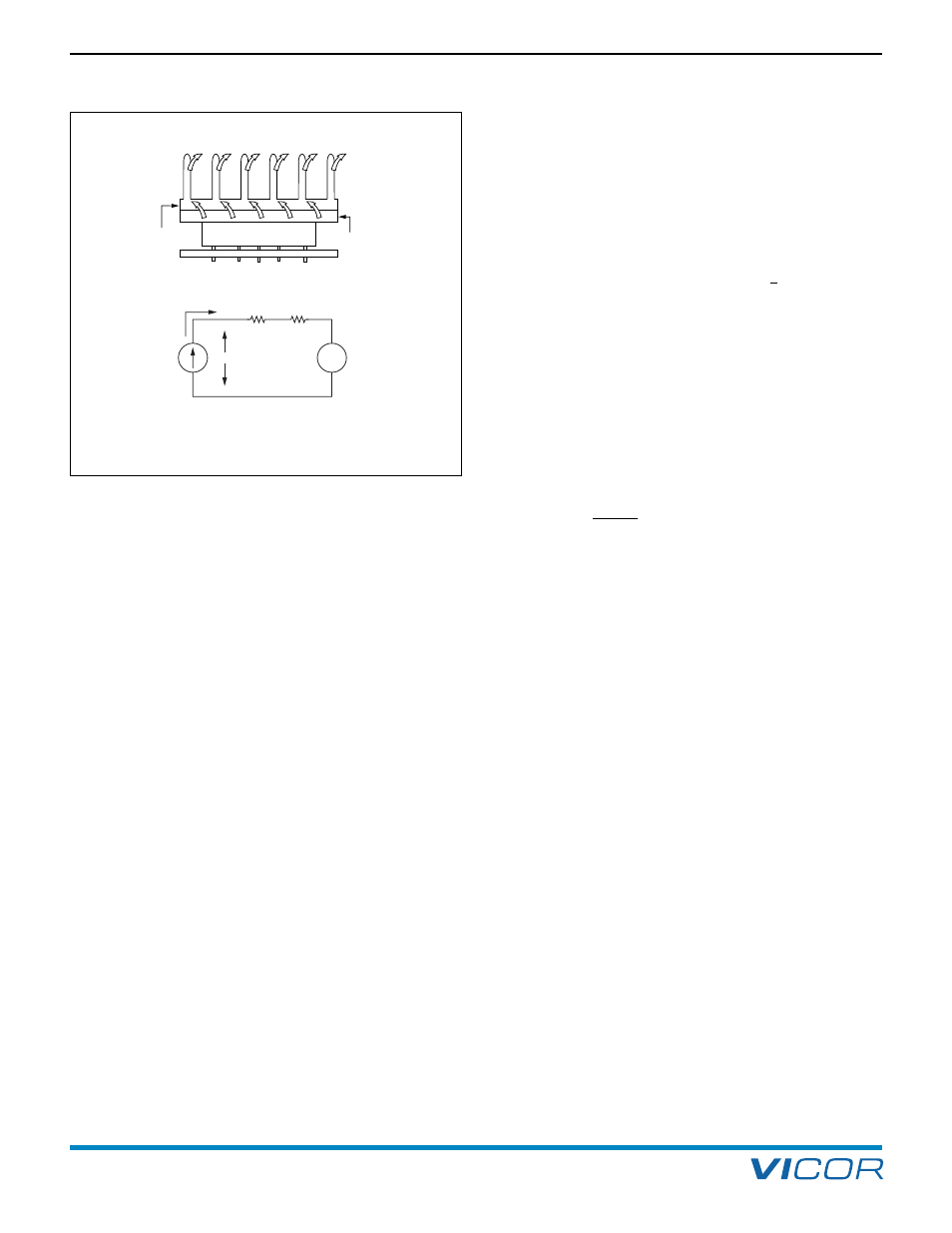
Design Guide & Applications Manual
For VI-200 and VI-J00 Family DC-DC Converters and Configurable Power Supplies
VI-200 and VI-J00 Family Design Guide
Rev 3.5
vicorpower.com
Page 62 of 98
Apps. Eng. 800 927.9474
800 735.6200
CONVECTION
Convective heat transfer into air is a common method for
cooling Vicor converters. “Free” or “natural” convection
refers to heat transfer from a dissipative surface into a
cooler surrounding mass of otherwise still air; forced
convection refers to heat transfer into a moving air stream.
The convection cooling model is shown in Figure 20-4.
Baseplate temperature depends on the temperature of the
air, total dissipated power and the values of two thermal
resistances; the thermal resistance of the surface interface
between the baseplate and the heat sink, and the heat
sink-to-air thermal resistance. Surface interface resistance
can be minimized as discussed under Conduction. The
heat sink-to-air resistance is dependent on a variety of
factors including heat sink material and geometry, air
temperature, air density and air flow rate. Fortunately,
thermal resistance data is available for a very wide range
of standard heat sinks for use in both free and forced
convection applications. The following sections will
provide guidelines for both free and forced convection
cooling of Vicor converters and configurables.
FREE CONVECTION
The benefits of free convection include low cost of
implementation, no need for fans, and the inherent
reliability of the cooling process. Compared to forced air
cooling, however, free convection will require more heat
sink volume to achieve an equivalent baseplate temperature.
To select a suitable heat sink for free convection cooling,
follow these steps:
1. Determine the power to be dissipated by the heat sink.
This should be based upon converter efficiency and
worst-case converter power output using the formula
given in the section on Module Efficiency and Dissipated
Power. (Figures 20–1a and 20–1b)
Power Dissipated = Power Output X
(
1
– 1
)
n
2. Estimate or experimentally determine the surface
interface thermal resistance. Use of thermal compound
or a thermal pad is recommended to minimize this
resistance. An estimate of 0.2˚C / Watt should provide
an adequate safety margin.
3. Referencing Figure 20–4, we can derive the following
formula for heat sink-to-air thermal resistance:
θ
sa
=
(
T
b
– T
a
)
–
θ
bs
P
diss
T
a
= Worst case anticipated operating ambient
air temperature.
θ
bs
= Surface interface thermal resistance, from Step 2.
P
diss
= Worst-case power dissipation, from Step 1.
T
b
= Baseplate temperature.
Start with a value of Tb = 85˚C (or 100˚C, VI-J00) to
determine the maximum acceptable heat sink-to-air
thermal resistance.
4. Select several heat sinks that appear physically
acceptable for the application. Using data provided,
obtain values for their free convection thermal
resistance, preferably at worst-case ambient
temperature, Ta. If values obtained are less than the
value calculated in Step 3, go on to Step 5. If the
values are greater, then either a physically larger heat
sink will be required or a different cooling method will
need to be used (i.e., forced air, etc.).
5. Select the heat sink with the lowest available thermal
resistance consistent with space and cost limits. Keep
in mind that small reductions in baseplate temperature
produce dramatic improvements in MTBF.
6. Baseplate temperature can be estimated by using the
following formula:
T
b
= T
a
+ P
diss
x (
θ
bs
+
θ
sa
)
7. Test to verify that performance is in line with expectations.
20. Thermal and Module Mounting Considerations
Figure 20–4 — Heat sink thermal considerations
(+)
Tb
(–)
Pdiss
Power
Dissipated
by Converter
(Watts)
Tb = Baseplate Temperature
bs = Baseplate – Heatsink Interface Resistance
sa = Heatsink-to-Air Thermal Resistance
Tb = Ta + ( bs + sa) x Pdiss
Ambient Air
Temperature
+
Ta
–
bs
sa
θ
θ
θ
θ
θ
θ
Surrounding Air Temperature (Ta)
Heat Flow
Heatsink
Baseplate