Thermal and module mounting considerations – Vicor VI-J00 Family DC-DC Converters and Configurable Power Supplies User Manual
Page 64
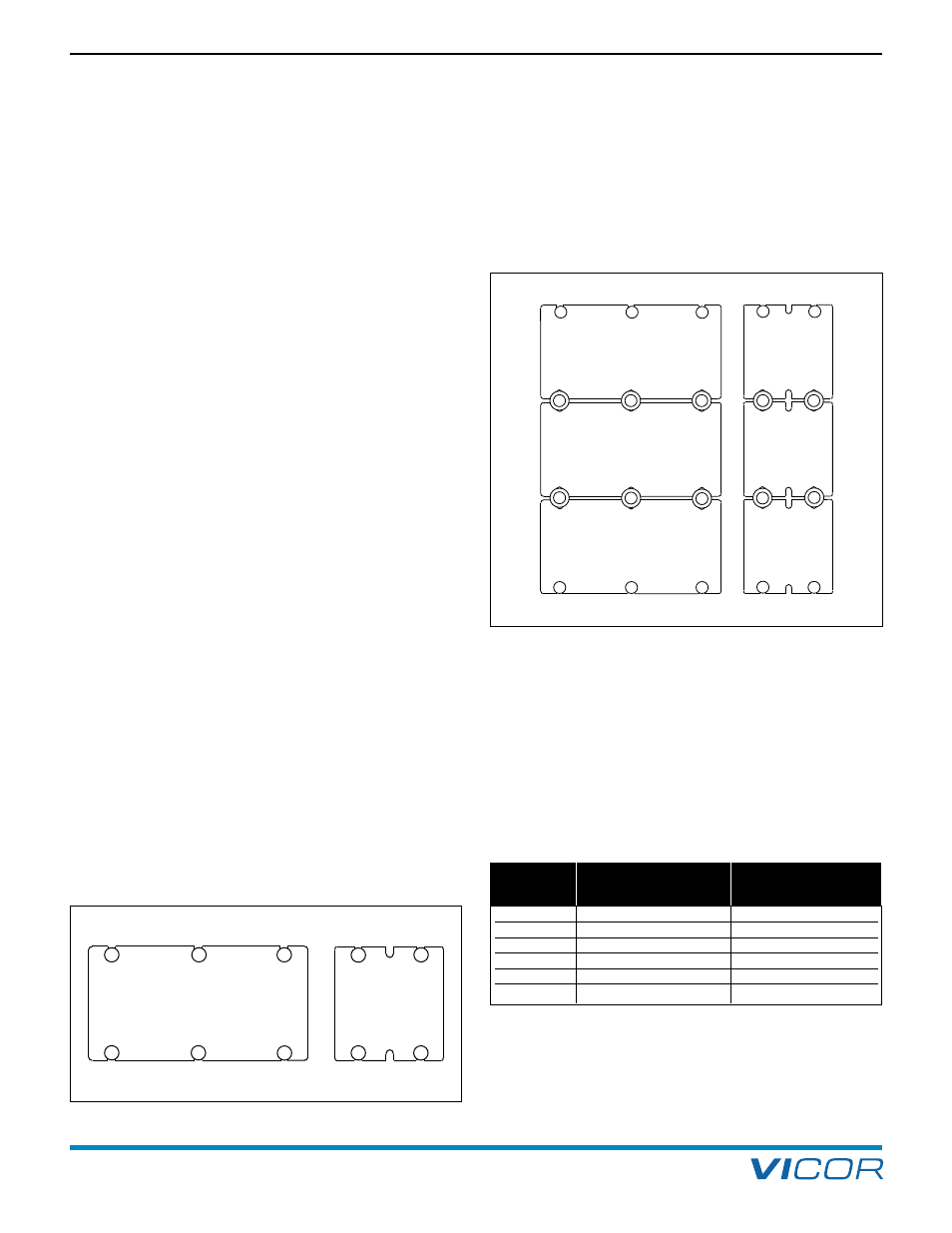
Design Guide & Applications Manual
For VI-200 and VI-J00 Family DC-DC Converters and Configurable Power Supplies
VI-200 and VI-J00 Family Design Guide
Rev 3.5
vicorpower.com
Page 63 of 98
Apps. Eng. 800 927.9474
800 735.6200
Heat sink data is almost always given for vertical fin
orientation. Orienting the fins horizontally will reduce
cooling effectiveness. If horizontal mounting is mandatory,
obtain relevant heat sink performance data or use forced
convection cooling.
Free convection depends on air movement caused by
heat-induced density changes. Thermal resistance data is
dependent on the heat sink fins being completely exposed
to the ambient air without any significant interference to
air flow at the ends of or along the length of the fins. If
packaging will tend to block or baffle air movement over
the fins, a larger heat sink might be required. In the worst
case, free convection may be ineffective. Make sure that
the fins are well exposed to ambient air.
It is not necessary to limit the size of the heat sink to the
size of the baseplate. Heat sinks with footprints larger
than the baseplate area can often be used to advantage.
In the latter case, heat must be conducted along the base
surface of the heat sink to get to the outer fins, so don’t
count on achieving full cooling capability. Also, several
modules can be mounted to a common heat sink, but
cooling calculations must now take into account total
power dissipation with consideration given to possible
localized overheating if worst-case converter power
dissipations are greatly imbalanced. When securing a PC
board containing two or more converters to a heat sink,
it is good practice to use sockets on the converter pins
to allow for mechanical alignment. If sockets are not
used, be sure to mount the converters first mechanically,
then solder the units in place. A fixture should be used
to maintain alignment if soldering must be performed
before attachment.
When mounting heat sinks to Vicor modules, use #6 or
M3.5 screws torqued uniformly through the mounting
slots provided. The following tightening sequence should
be used:
• Lightly finger-tighten all screws
• Torque screws to 6 in-lbs (0.7 N – m) per Figure 20–5.
Multiple Modules Using Common Fasteners. The
following mounting scheme should be used to attach
modules to a heat sink for two or more modules. A large,
heavy washer should be used on the common fasteners to
distribute the mounting force equally between modules.
The torquing sequence shown in Figure 20–6 can easily
be expanded from two to any number of modules. An
array of three is shown.
FORCED CONVECTION
Forced air can make a great difference in cooling
effectiveness. Heat sink-to-air thermal resistance can be
improved by as much as an order of magnitude when
compared to free convection performance, by using
suitable heat sinks. Consider the following data for
baseplate-to-air thermal resistance (no heat sink) of a
VI-200 or VI-J00 module at various airflow rates:
Forced air implies the use of fans. Many applications
require that fans be used to achieve some desired
combination of overall system reliability and packaging
density. Industrial environments will require filters that must
20. Thermal and Module Mounting Considerations
4
2
5
3
1
6
4
2
3
1
Figure 20–5 — Heat sink torquing sequence VI-200 / VI-J00
8
4
12
5
1
9
1
8
5
4
3
11
6
2
10
7
2
3
6
7
Figure 20–6 — Torquing sequence, multiple VI-200 / VI-J00 converters
Free Air
5.1˚C/W
8.1˚C/W
200 LFM
2.8˚C/W
5.1˚C/W
400 LFM
1.8˚C/W
2.7˚C/W
600 LFM
1.4˚C/W
2.3˚C/W
800 LFM
1.2˚C/W
1.7˚C/W
1,000 LFM
1.0˚C/W
1.4˚C/W
VI-200
VI-J00
Airflow
Baseplate to Air
Baseplate to Air
Thermal Resistance
Thermal Resistance
Table 20–1 — Baseplate-to-airflow thermal resistance (no heat sink)