Thermal and module mounting considerations – Vicor VI-J00 Family DC-DC Converters and Configurable Power Supplies User Manual
Page 65
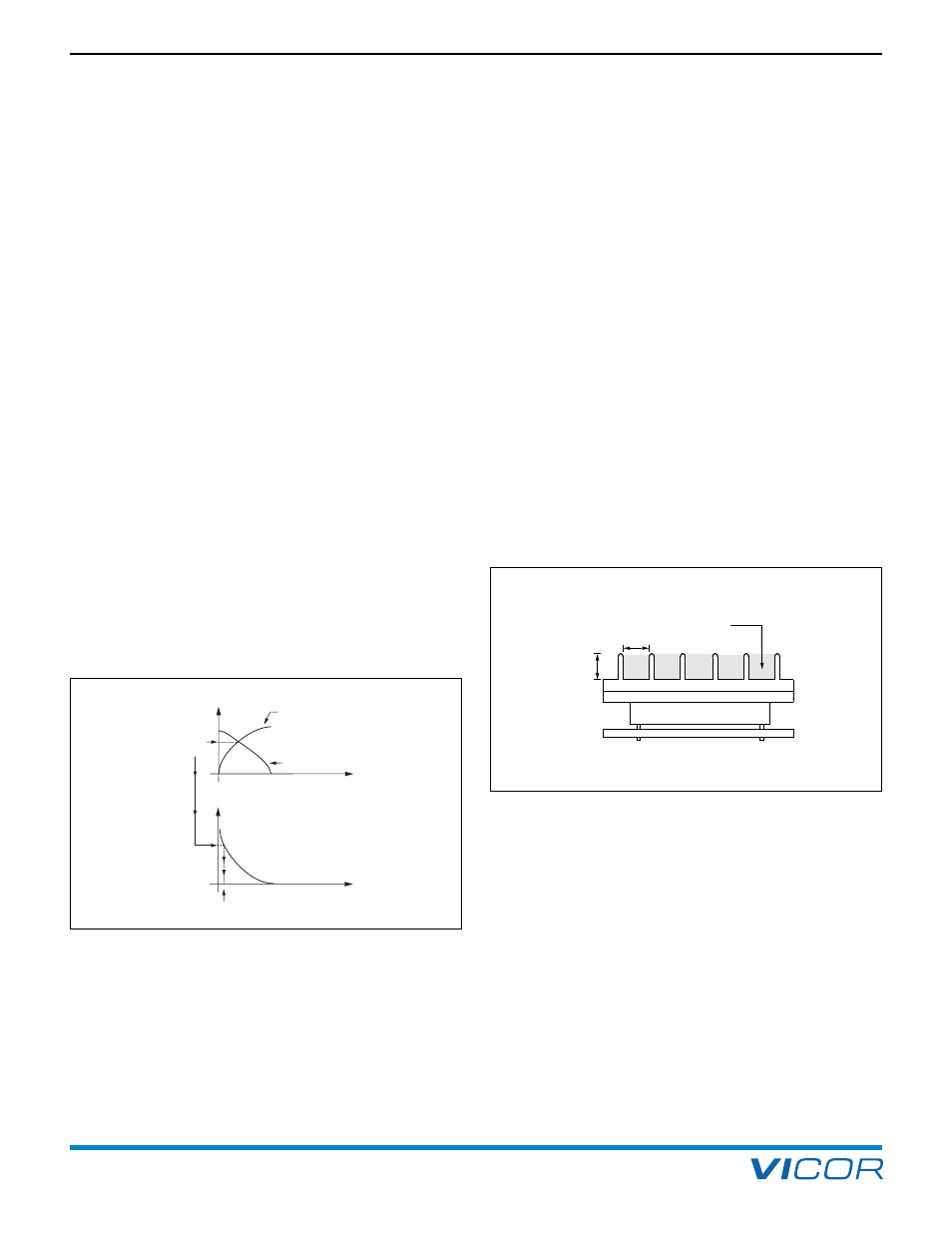
Design Guide & Applications Manual
For VI-200 and VI-J00 Family DC-DC Converters and Configurable Power Supplies
VI-200 and VI-J00 Family Design Guide
Rev 3.5
vicorpower.com
Page 64 of 98
Apps. Eng. 800 927.9474
800 735.6200
be changed regularly to maintain cooling efficiency, and
neglecting to change a filter or the failure of the fan could
cause the system to shut down or malfunction.
The steps involved in selecting a heat sink / fan
combination for forced convection are essentially the
same as those followed for free convection, with the
additional requirement that the heat sink and fan be
matched to achieve desired heat sink-to-air thermal
resistance. Attention must also be paid to proper
channeling of fan airflow so that maximum utilization of
its cooling capability is realized. Selection of a heat sink /
fan combination involves the following three steps:
1. Determine maximum acceptable heat sink-to-air
thermal resistance by following the first three steps
of the heat sink selection procedure given in the
Free Convection section.
2. Selection of a heat sink / fan combination requires that
forced convection data for both the heat sink and fan
be available. Forced convection characteristics for heat
sinks define both heat sink-to-air thermal resistance
and pressure drop through the heat sink as a function
of airflow. Fan characteristics define airflow as a function
of pressure drop. The intersection point of the airflow
versus pressure curves for the fan and heat sink will
define the operating airflow through the heat sink.
(Figure 20–7) The heat sink-to-air thermal resistance
for this airflow may be read directly off the airflow
versus resistance curve for the heat sink.
Finding and interpreting the operating point requires
consideration of the following:
Units of pressure drop are generally given in inches of
water. Units of fan airflow are in cubic feet per minute
(CFM). Occasionally metric units are used, but conversion
is straightforward.
Heat sink airflows may be given either in CFM or LFM
(linear feet per minute). The conversion between LFM
and CFM is dependent on the cross-sectional area
through which air is flowing: CFM = LFM X Area
The cross-sectional area between the fins is the area
through which the total airflow must pass. (Figure 20–8)
Correct interpretation of heat sink data requires that
only the airflow through this area be considered.
Simply pointing a fan at a heat sink will clearly not
result in all of the flow going through the cooling
cross-section of the sink; some channeling of air is
usually required to get the full benefit of fan output.
The fan curves give output in CFM versus pressure
drop. Fan pressure drop is the total of all drops
encountered by the fan airflow. The heat sink, any
ducting that is used, and air entry and exit channels all
contribute to pressure drop. Pressure drop represents
the work done by the fan in moving air through a
region, so care should be taken to minimize unproductive
pressure losses. Ensure that air entry and exit locations
and internal air channels are not unduly constricted,
and avoid sharp turns in airflow paths.
The thermal resistance that was determined by
overlapping the fan and heat sink curves will represent
an optimistic estimate since it assumes that all the fan
output flows through the heat sink cooling cross section,
and that all the pressure drop occurs along the heat
sink. If the estimated thermal resistance is close to the
minimum value determined in Step 1, then it is likely
that a larger fan or different heat sink is required. This
will not be a problem in most cases; relatively modest
heat sinks and fans usually provide ample cooling.
Careful channeling and ducting of airflow as a means
of both maximizing flow through the cooling cross-
section of the heat sink and minimizing extraneous
flow of air around the sink is well worth the small
extra design effort required. Every degree of
20. Thermal and Module Mounting Considerations
Airflow
(CFM)
Heatsink
Curve
Fan
Curve
Operating
Airflow
Airflow
(CFM)
Thermal Resistance
at Operating Airflow
Heatsink to Air
Thermal Resistance
(˚C/Watt)
X
Pressure
(in. H O)
2
Figure 20–7 — Airflow vs. resistance
Cooling Airflow is Air Which
Flows Through the Shaded
Cooling Cross-Sectional Area
Area = (N - 1) x H x S
S
H
S = Fin Spacing
H = Fin Height
N = No. of Fins
Figure 20–8 — Heat sink cross section