Sect. 20, Thermal and module mounting considerations – Vicor VI-J00 Family DC-DC Converters and Configurable Power Supplies User Manual
Page 61
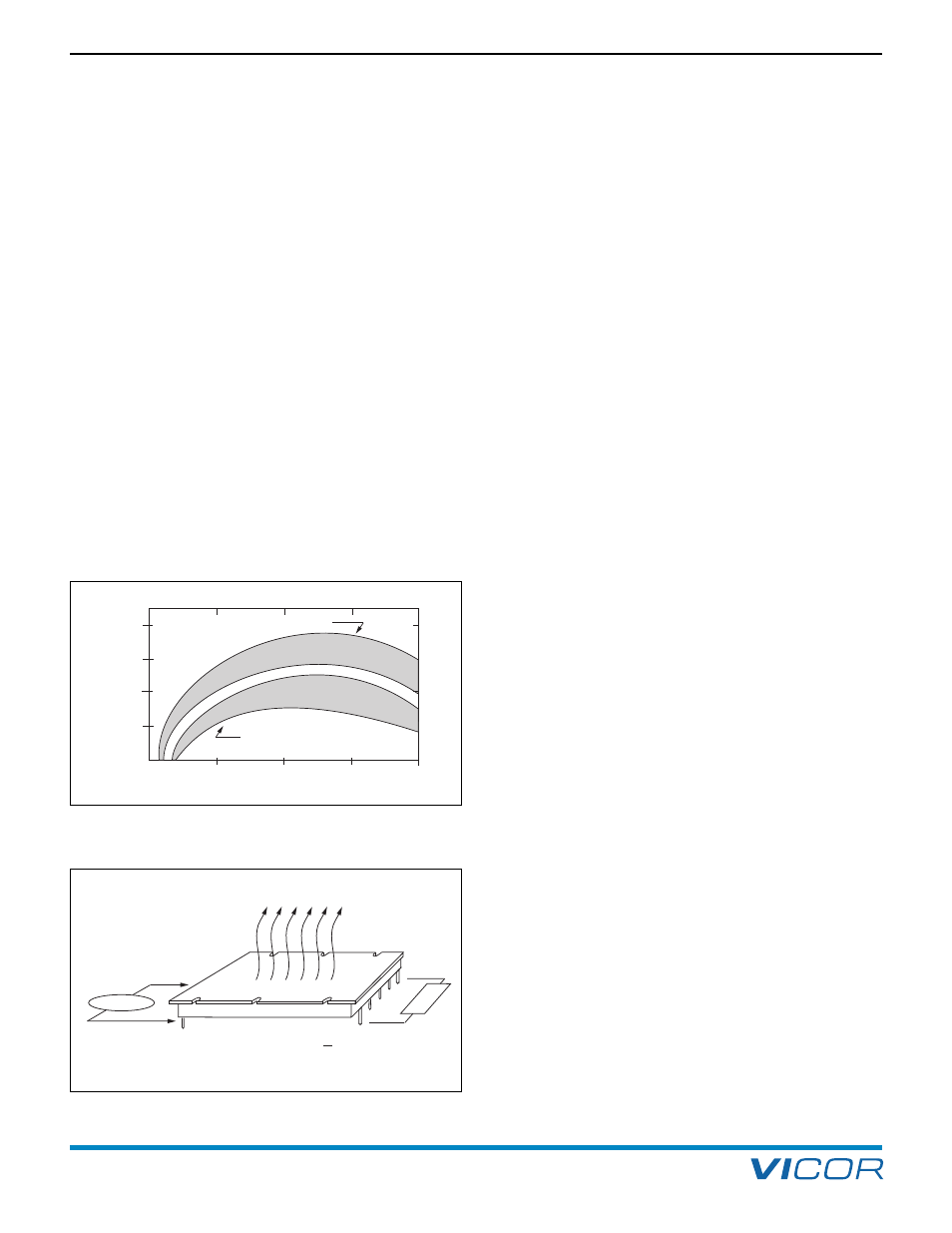
Design Guide & Applications Manual
For VI-200 and VI-J00 Family DC-DC Converters and Configurable Power Supplies
VI-200 and VI-J00 Family Design Guide
Rev 3.5
vicorpower.com
Page 60 of 98
Apps. Eng. 800 927.9474
800 735.6200
OVERVIEW
Simplified thermal management is one of the benefits of
using Vicor converters. High operating efficiency minimizes
heat loss, and the low profile package features an easily
accessible, electrically isolated thermal interface surface.
Proper thermal management pays dividends in terms of
improved converter and system MTBFs, smaller size and
lower product life-cycle costs. The following pages provide
guidelines for achieving effective thermal management of
Vicor converters.
EFFICIENCY AND DISSIPATED POWER
A DC-DC converter takes power from an input source and
converts it into regulated output power for delivery to a
load. Not all of the input power is converted to output
power however; some is dissipated as heat within the
converter. The ratio of delivered output power to
converter input power is defined as the converter’s
efficiency. Efficiency is a basic figure of merit that can be
used to relate power dissipation directly to converter
output power, as illustrated in Figures 20–1a and 20–1b.
The first step in evaluating cooling requirements is to
calculate worst-case dissipation based on converter
efficiency and worst-case anticipated load power. Clearly,
higher efficiency will translate into lower power dissipation
and simplify the cooling problem. Vicor converters are
among the most efficient converters available, with full
load efficiencies typically in excess of 80%.
REMOVING HEAT FROM VICOR CONVERTERS
Heat is removed from Vicor converters through the flat
metal baseplate on top of the module. The baseplate is
thermally coupled to, but electrically isolated from, all
internal heat-generating components. The basic thermal
design problem is to transfer heat from the baseplate into
the surrounding environment as a means of maintaining
baseplate temperature at or below rated maximum.
Heat energy is transferred from regions of high temperature
to regions of low temperature via three basic mechanisms;
radiation, conduction and convection.
Radiation. Electromagnetic transfer of heat between
masses at different temperatures.
Conduction. Transfer of heat through a solid medium.
Convection. Transfer of heat through the medium of a
fluid; typically air.
All three of these heat transfer mechanisms are active to
some degree in every application. Convection will be the
dominant heat transfer mechanism in most applications.
Nondominant effects will provide an added contribution
to cooling; in some cases, however, they may result in
undesirable and unanticipated thermal interactions
between components and subassemblies.
All three of these mechanisms should be given consideration
when developing a successful cooling strategy.
RADIATION
Radiant heat transfer occurs continuously between objects
at different temperatures that are exposed to each other.
The net effect on the temperature of an individual part is
dependent on a great many factors, including its temperature
relative to other parts, relative part orientations, surface
finishes and spacing. The difficulty in quantifying many of
these factors, combined with the universal presence of
radiant energy exchange, makes calculation of radiational
temperature effects both a complex and generally
imprecise task.
92%
88%
84%
80%
20%
50%
75%
100%
12 V, 15 V, 24 V and 48 V Models
5 V Models
Percentage of Load
Efficiency
Load
+
–
Input
Source
Power Input = Power Dissipated as Heat + Power Output
Power Dissipated = Power Output X
Power Input x Efficiency (η) = Power Output
1
n
)
)
–1
20. Thermal and Module Mounting Considerations
Figure 20–1a — Module efficiency
Figure 20–1b — Dissipated power