2 block mode, Block mode -2 – Yokogawa EJX930A User Manual
Page 43
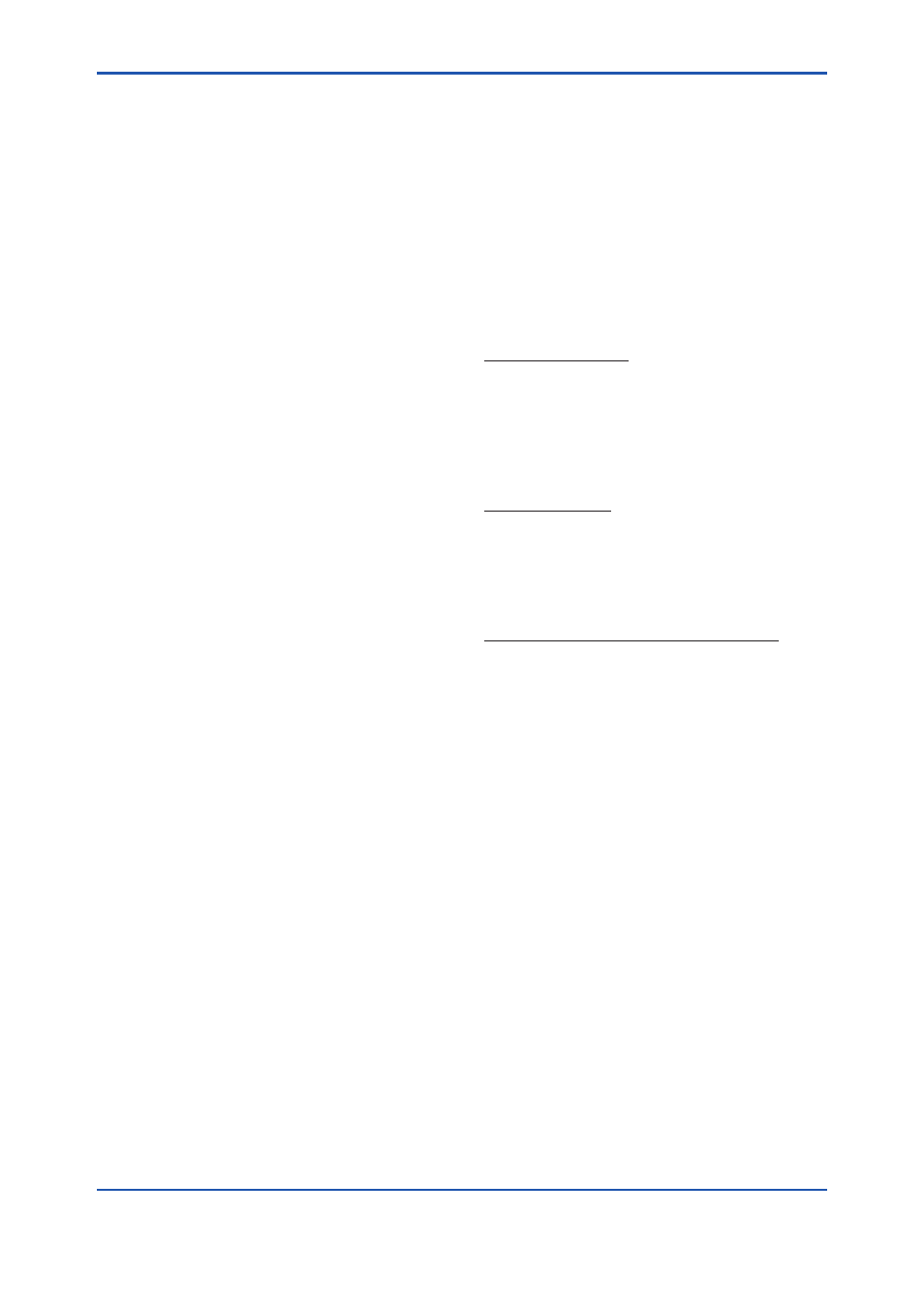
<6. Explanation of Basic Items>
6-2
IM 01C25T02-01E
6.3.2 Block Mode
The Block modes permitted for the SENSOR
transducer block are Automatic (Auto) and Out of
Service (O/S). The mode must be set to Auto under
normal operating conditions, and to O/S when
making changes to an important parameter. For
parameters that can only be changed in the Auto
and O/S modes, refer to the parameter list for the
SENSOR Transducer block in Chapter 9.
6.3.3 Functions Relating to Pressure/
Differential Pressure
Reference to pressure/differential pressure
value:
By accessing PRIMARY_VALUE, it is possible to
refer to the pressure/differential pressure value
and status. The update period of this value is 100
mseconds. The pressure unit is selected by XD_
SCALE.unit of the AI block, in which PRIMARY_
VALUE is selected. The status is normally Good-
Non Specific. However, in the case of a sensor
failure or out of measurement range, it turns to Bad
or Uncertain. For details, refer to Table 8.9.
Setting of signal damping for pressure/
differential pressure:
When the pressure/differential pressure signal
fluctuates greatly, the fluctuation can be reduced
by increasing the time constant for signal damping.
PRIMARY_VALUE_FTIME is the parameter for
setting the signal damping for pressure/differential
pressure. The unit of signal damping is second.
Determination of the range limit of pressure/
differential pressure signal:
When the pressure/differential pressure signal
deviates more than 10% from the capsule
measurement range shown in PRIMARY_VALUE_
RANGE, set the status of PRIMARY_VALUE to
Uncertain-Sensor Conversion not Accurate.
Adjustment of pressure/differential pressure
signal:
EJX Series Pressure/Differential Pressure
Transmitters have been accurately adjusted
according to the specifications at factory setting.
Minimal errors can occur due to the environment
where the transmitter is installed and the mounting
position. To fine-tune any errors, three zero/span
adjustment functions can be used: automatic and
manual zero/span adjustment by communication
terminals, and zero-point adjustment by means of
the external adjustment screw on the transmitter.
Automatic adjustment
The value of the pressure exerted on the point
where the adjustment is to be made is assigned
to parameters (CAL_POINT_LO, CAL_POINT_
HI). After this assignment is set, the amount of
adjustment is calculated by the transmitter and
automatically updated.
Manual adjustment
From the exerted pressure and the output of the
transmitter, calculate the amount of zero/span
adjustment manually, and assign the calculated
value to parameters (CAL_DEVIATION_LO,
CAL_DEVIATION_HI).
Zero-point adjustment by the external screw.
With pressure being exerted on the point where
the adjustment is to be made, zero adjustment
needs to be performed. To do this, adjust the
calculated value by turning the external Zero-point
adjustment screw, so that it agrees with the actual
input pressure (true value). The output value
increases when the screw is rotated to the right. It
decreases when the screw is rotated to the left. The
adjustment width is small when the rotation speed
is low and large when fast.
When performing zero-point adjustment by the
external screw, EXTERNAL_ZERO_TRIM needs to
be set to “Enable.”