About fieldbus, 1 outline, 2 internal structure of dpharp – Yokogawa EJX930A User Manual
Page 25: 1 system/network management vfd, 2 function block vfd, 3 logical structure of each block, 4 wiring system configuration, About fieldbus -1, Outline -1, Internal structure of dpharp -1 3.2.1
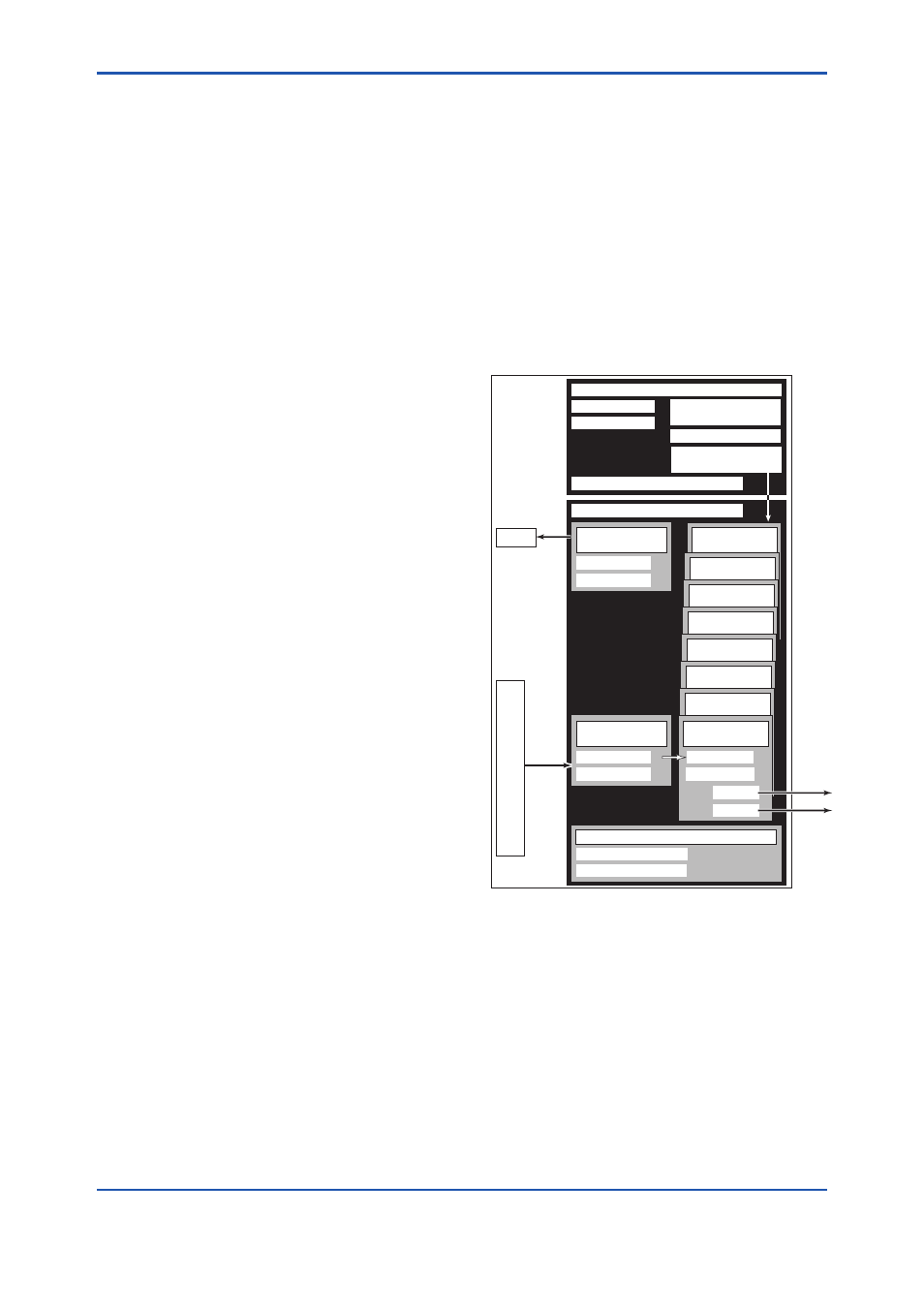
<3. About Fieldbus>
3-1
IM 01C25T02-01E
3. About Fieldbus
3.1 Outline
Fieldbus is a widely used bi-directional digital
communication protocol for field devices that
enable the simultaneous output to many types of
data to the process control system.
The transmitter of Fieldbus communication type
employs the specification standardized by The
Fieldbus Foundation, and provides interoperability
between Yokogawa devices and those produced by
other manufacturers. Fieldbus comes with software
consisting of three AI function blocks that enable the
flexible implementation of systems.
For information on other features, engineering,
design, construction work, startup and maintenance
of Fieldbus, refer to “Fieldbus Technical Information”
(TI 38K03A01-01E).
3.2 Internal Structure of DPharp
The transmitter contains two virtual field devices
(VFD) that share the following functions.
3.2.1 System/network Management VFD
• Sets node addresses and Physical Device tags
(PD Tag) necessary for communication.
• Controls the execution of function blocks.
• Manages operation parameters and
communication resources (Virtual
Communication Relationship: VCR).
3.2.2 Function Block VFD
(1) Resource block
• Manages the status of transmitter hardware.
• Automatically informs the host of any detected
faults or other problems.
(2) SENSOR Transducer block
• Converts sensor output to pressure, static
pressure, and capsule temperature signals, and
transfers to the AI function blocks.
(3) LCD Transducer block
• Controls the display of the integral indicator.
(4) AI1 function block
• Condition raw data from the Transducer block.
• Output differential pressure, static pressure and
capsule temperature signals.
• Carry out scaling, damping and square root
extraction.
(5) PID function block
• Performs the PID control computation based on
the deviation of the measured value from the
setpoint.
3.3 Logical Structure of Each
Block
PID function
block
F0301.ai
DPharp
Fieldbus
System/network management VFD
Function block VFD
Link Master
PD Tag
Resource block
Block tag
Parameters
Communication
parameters
VCR
Node address
Function block
execution schedule
LCD
Transducer block
Block tag
Parameters
LCD
AR function
block
IS function
block
IT function
block
SC function
block
AI function
block
AI function
block
Sensor
input
Output
SENSOR
Transducer block
Block tag
Parameters
AI function
block
Block tag
OUT
Parameters
OUT_D
Sensor
Figure 3.1
Logical Structure of Each Block
Setting of various parameters, node addresses,
and PD Tags shown in Figure 3.1 is required before
starting operation.
3.4 Wiring System Configuration
The number of devices that can be connected to
a single bus and the cable length vary depending
on system design. When constructing systems,
both the basic and overall design must be carefully
considered to achieve optimal performance.