1 load sharing, Load sharing -13 – KEPCO KLP Series User Manual, Rev 4 User Manual
Page 39
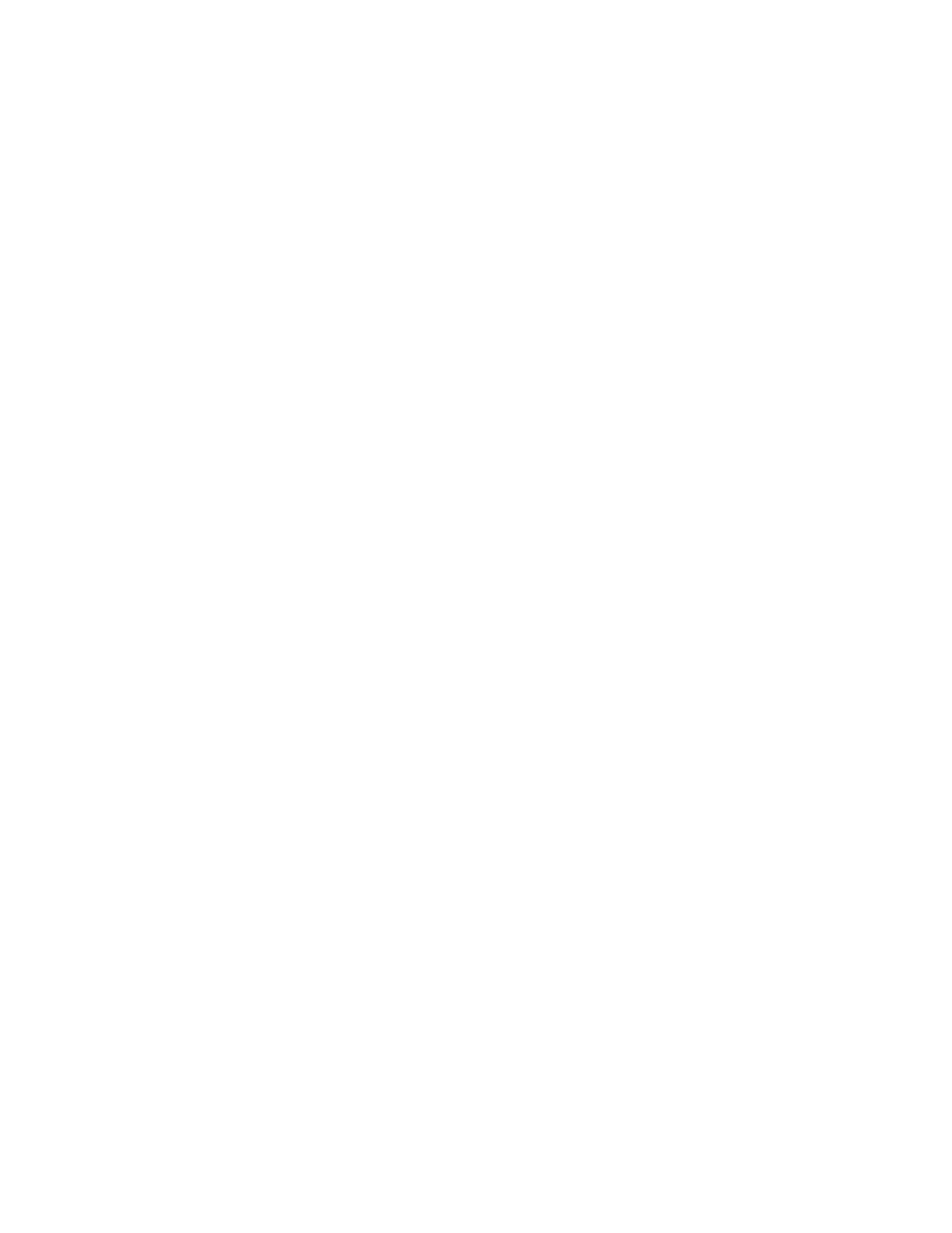
KLP-HV 091313
2-13
2.7.7.1
LOAD SHARING
When operating two or more power supplies in parallel, either for capacity or redundancy, it is
desirable to distribute the load equally among all of the power supplies in order to improve per-
formance, reduce stress and increase reliability. KLP power supplies incorporate active circuitry
which forces multiple power supplies wired in parallel to share load current, both in voltage- and
current-mode regulation. The KLP employs a single wire connection between paralleled power
supplies, forming a master-slave relationship as follows: the highest voltage unit becomes the
master, and all of the remaining units are slaved to it via the current share signal (CS, available
at the rear panel terminal A3TB3, Figure 2-2), which boosts the slave outputs in order to
increase load share. A maximum boost limit prevents the slave units from following a defective
master into an overvoltage condition, or from creating a load hazard if either the slave itself or
the load sharing system is defective.
When implementing load sharing, the user must ensure that all power supplies are attempting to
regulate to the same voltage at the same location, and must minimize the possibility of load
share signal corruption; the power supplies should, as nearly as possible, emulate a single large
power supply. To this end, the following rules apply:
a. All error sense connections must terminate to the same physical point, whether the feedback
is configured as local or remote sensing.
For local error sensing, select one power supply as output regulation point and leave
the local error sense jumpers in place. Remove the local error sense jumpers from all other
units and use tightly-twisted wire triplets to daisy-chain the S+, CS and S- terminals to the
first power supply.
For remote error sensing the same procedure is followed as for local sensing, except
that the local error sense jumpers are removed from the first power supply as well, and a
tightly-twisted wire pair is connected from the S+ and S- terminals of the first power supply to
the load regulation point. Install the HF bypass network indicated in Figure 2-5 across the
error sense termination points.
b. The power supplies should be located as near to each other as possible, preferably in verti-
cally adjacent (stacked) positions. Power terminations must be bussed together using ade-
quately-sized interconnecting conductors, both between the paralleled outputs and from the
power supply assembly to the load. Current rating of the conductors must accommodate the
total maximum current contribution based on the programmed current regulation points of all
power supplies. For the low-voltage models (10V, 20V, 36V) Kepco advises the use of bus
bar conductors where possible; for higher voltage models (75V - 600V), appropriately sized
twisted conductor pairs terminated with wire ferrules are recommended (contact Kepco
Applications Engineering for details).
c. For local error sensing, the power outputs should be daisy-chained to the power supply out-
put terminals serving as the regulation point, and from there to a connection run to the load.
For remote sensing, load connections may be run directly from each power supply's output
terminals to the error sense regulation point, or daisy-chained as for remote sensing connec-
tions. In each case, the connections from the power supply outputs to the load must be prop-
erly sized for maximum current and configured to minimize inductance and noise, either
through twisted wires, power coaxial cabling or parallel or laminated bus bars. For guidance
on wire sizing see the nomograph at www.kepcopower.com/nomomax.htm.