Datum shift (cycle 7), 12 coor dinat e t ransf or mation cy cles – HEIDENHAIN iTNC 530 (340 49x-04) User Manual
Page 514
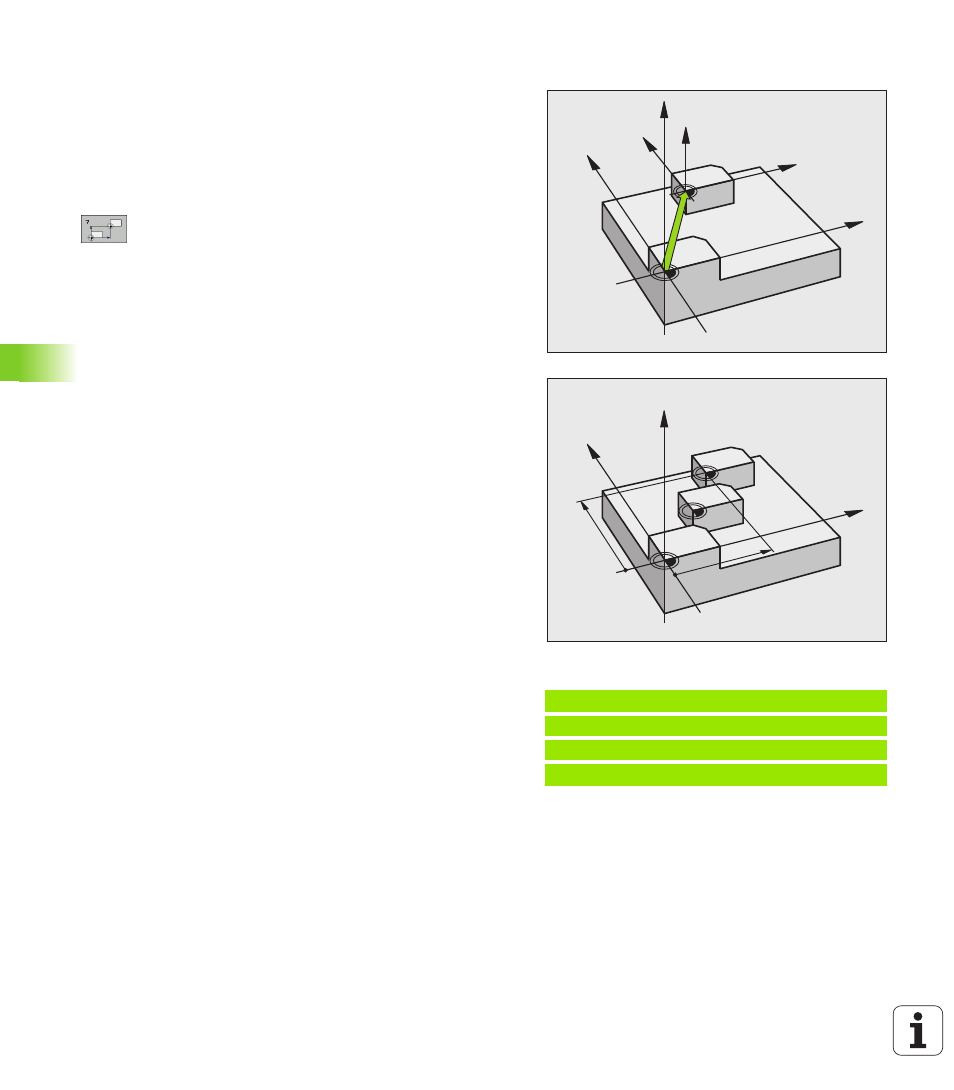
514
8 Programming: Cycles
8.12 Coor
dinat
e
T
ransf
or
mation Cy
cles
DATUM SHIFT (Cycle 7)
A DATUM SHIFT allows machining operations to be repeated at
various locations on the workpiece.
Effect
When the DATUM SHIFT cycle is defined, all coordinate data is based
on the new datum. The TNC displays the datum shift in each axis in
the additional status display. Input of rotary axes is also permitted.
Datum shift:
Enter the coordinates of the new
datum. Absolute values are referenced to the
manually set workpiece datum. Incremental values
are always referenced to the datum which was last
valid—this can be a datum which has already been
shifted.
Cancellation
A datum shift is canceled by entering the datum shift coordinates X=0,
Y=0 and Z=0. Alternately, you can use the TRANS DATUM RESET function
(see “TRANS DATUM RESET” on page 578).
Graphics
If you program a new BLK FORM after a datum shift, you can use
MP7310 to determine whether the BLK FORM is referenced to the
current datum or to the original datum. Referencing a new BLK FORM
to the current datum enables you to display each part in a program in
which several pallets are machined.
Status displays
The actual position values are referenced to the active (shifted)
datum.
All of the position values shown in the additional status display are
referenced to the manually set datum.
Example: NC blocks
13 CYCL DEF 7.0 DATUM SHIFT
14 CYCL DEF 7.1 X+60
16 CYCL DEF 7.3 Z-5
15 CYCL DEF 7.2 Y+40
Z
Z
X
X
Y
Y
Z
X
Y
X
Y