Hypertherm HTA Rev 6.00 Install Guide User Manual
Page 114
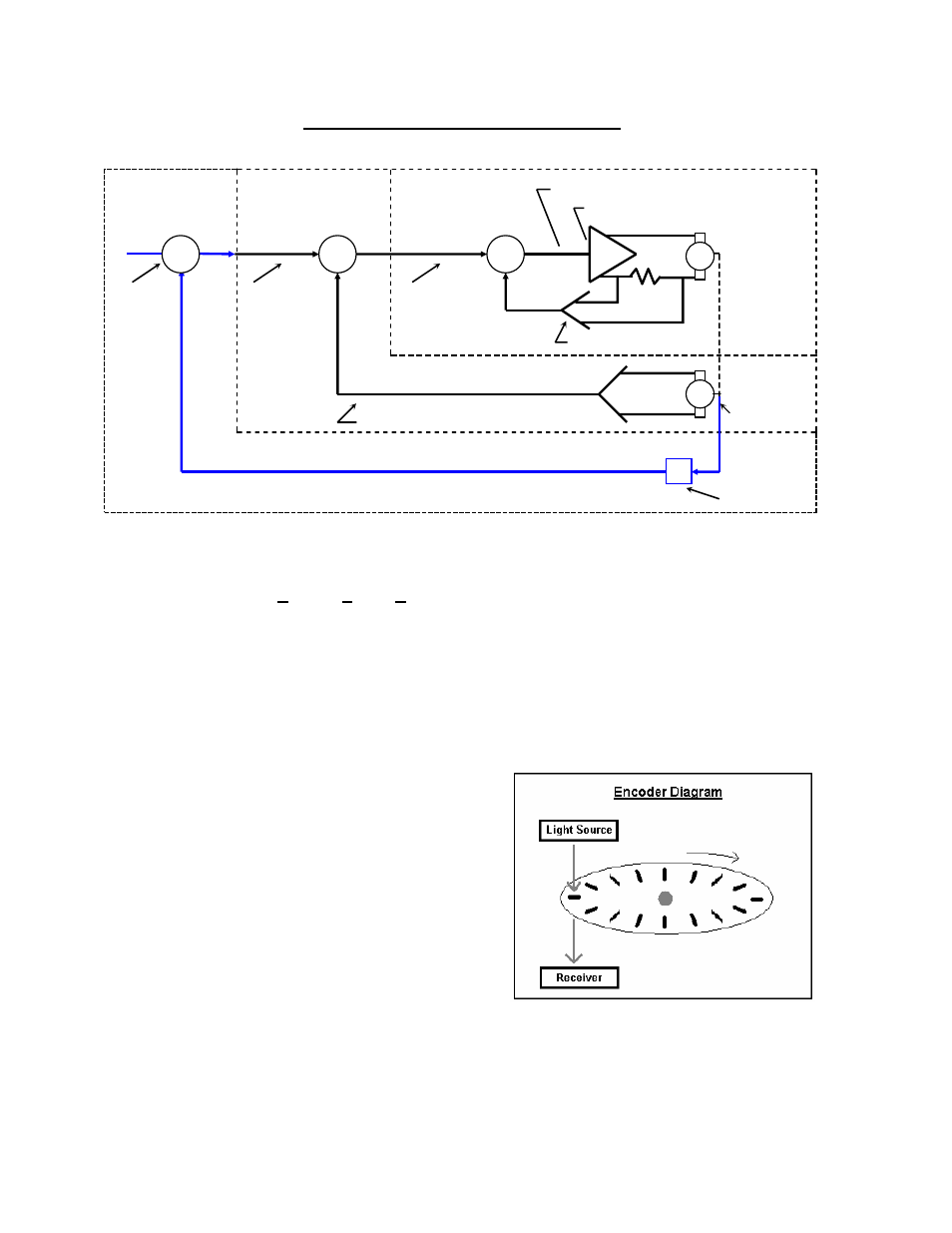
102
Installation & Setup Guide
Typical Velocity and Position Loop System
The Motion Command starts as Digital Output within the control and then is converted to a +/- 10VDC
Analog Output for use by the motors. This conversion of the Motion Command within the control is
referred to as the DAC (Digital to Analog Converter) Output and is performed by the Motion Control
Card. The Analog Output when it comes out of the control is sent to a drive amplifier that then steps
up the voltage output to the motor and creates motion. Also, there is usually a linear relationship
between the voltage sent and the machine speed ( i.e. 10 volts = maximum machine speed, 5 volts =
half max machine speed). Additionally, the polarity of the output (DAC Polarity +/-) to the amplifier
will dictate the direction of the motor rotation. In most applications and in the following application
description the feedback device is an Encoder.
1a) What is an Encoder?
Essentially, an Encoder is a feedback device that
provides signal pulses as the motor turns. The diagram
at the right illustrates the basic concept of an Encoder.
Although this does not represent all Encoder / feedback
device technology, this illustration provides a visual aid
to help understand the process.
The illustration shows a disk with small holes cut out
along the outer edge. The light source provides a
beam of light projected downward through the holes in
the disk. As the disk turns on the end of the motor
shaft, the light passes through the disk creating pulses.
The Receiver below the disk picks up the pulsed light
source and sends that feedback to the control.
Current
Command or
Velocity Error
Signal
Velocity
Command
Signal
Servo
Motor
Current Amplifier
Current Error Signal
Current
Feedback
Tachometer
Velocity
Loop
Current
Loop
Position
Loop
E
Position
Command
Encoder
+
-
Velocity Feedback Signal
+ +
-
-
∑
∑
∑
M
T
R
S