5 probe error, 6 power failure and backup battery error – EVCO EPD4DF3 Installer manual User Manual
Page 52
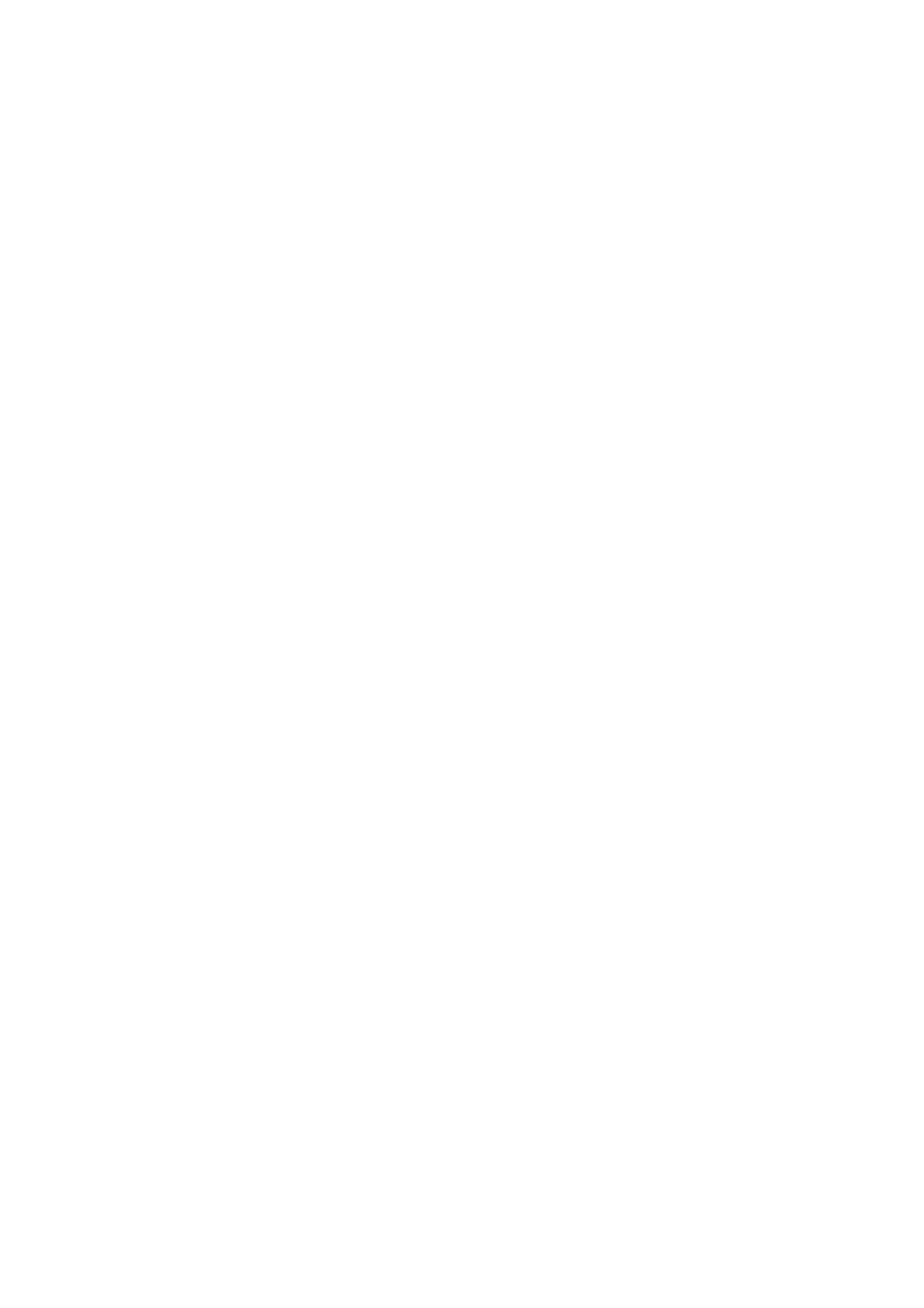
EVCO S.p.A.
EVDRIVE03 | User manual ver. 3.4 | Code 144EPDE344
page 52 of 70
9.5
Probe error
The probe alarm state is monitored every main cycle and is shown in bits 4÷7 of Alarm status (AlSt) and also signalled
by the relay, if configured.
Each bit is associated with a single analog input:
-
bit 4: error state for probe connected to analog input AI1
-
bit 5: error state for probe connected to analog input AI2
-
bit 6: error state for probe connected to analog input AI3
-
bit 7: error state for probe connected to analog input AI4
A probe error state is signalled and, if necessary, managed, only when the respective probe is in use.
Be aware that the measurements are valid only in operation modes in which the valve is enabled (FSM status ≥ 30); in
other states, the analog inputs might not be configured correctly.
When the state machine enter the Stand-by off, after the parameters check, it is possible to determine which probes
will be used: for example, if an analog positioner is set using setting Pcty = 1, only an error on probe 1 will generate
an alarm. If, on the other hand, an algorithm (Pcty ≥ 6) is selected, both the selected primary probes (and, eventually,
those chosen as secondary probes) will be able to set an alarm. The signalling of the alarms is thus active after the
first entry into the Stand-by off.
In states where it is really necessary that the values from analog inputs are reliable, i.e. in analog positioner and SH-
algorithm mode, a more complete probe error management system is activated.
When the analog positioner function is selected (Analog positioner (30)), a probe error on a probe currently in use will
trigger a positioning move to the value Probe alarm position (Pr05), and the system is changed to Probe alarm (3),
where it will then wait for the clearing of the alarm from the relevant probe.
If a SH-algorithm is active, the probe errors monitored are those related to pressure and temperature measures. Any
probe error will be handled as follows:
if the alarm relates to the primary probe (temperature or pressure), and another analog input has been configured as
a backup probe (for temperature or pressure respectively), the measurement is automatically read from the backup
probe; the corresponding Alarm status (AlSt) bit is set to signal a malfunction on the primary probe. Once the primary
probe's alarm state has been cleared, the readings are taken from the primary probe once more.
if no backup probe is defined, or if also the backup probe goes in alarm, the algorithm is disabled; the valve is
positioned at Probe alarm position (Pr05), and the FSM enters the Probe alarm (3), where it awaits the clearing of the
alarm state.
In each case, positioner or SH-algorithm, when the probe alarm is cleared, the state is automatically changed to
Stand-by off.
If the valve is disabled while is in Probe alarm (3), there is a positioning to Stand-by position (Pr20) and then it enter
Stand-by off.
9.6
Power failure and backup battery error
The EVDRIVE03 supports connection to a backup battery in order to allow a complete closure of the valve in the case
of power supply failure.
There are two alarms: one for the power supply failure (bit 8), the other for a malfunction of the backup battery (bit 9).
Clearly, both these alarms make sense only if a backup battery is present (parameter Backup battery (Pb01 = 1).
The backup battery alarm also requires the configuration of DI2 (DI2 logic (PH20) and DI2 function (PH21)).
Note that the backup battery alarm only signalize the malfunction of the battery.
However, if the power fail alarm occurs, in addition to reporting, a valve safety shutdown procedure is started.
Once the alarm is cleared, the system is reset.
An alternative to the backup battery, a solenoid valve connected to the relay may be used to block the flow of the
refrigerant.