Vicor Micro Family of DC-DC Converter User Manual
Page 46
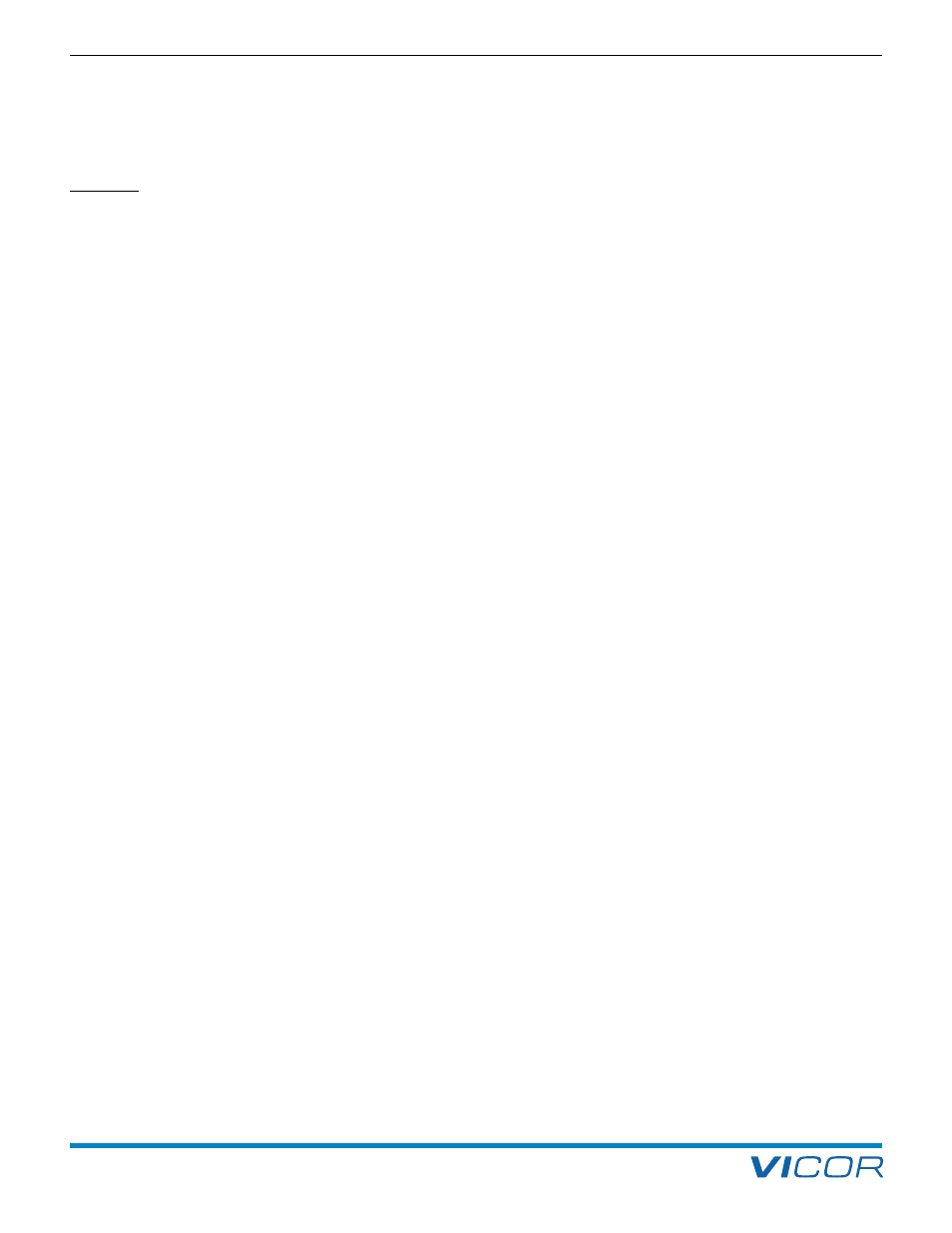
Design Guide & Applications Manual
For Maxi, Mini, Micro Family DC-DC Converters and Configurable Power Supplies
Maxi, Mini, Micro Design Guide
Rev 4.9
vicorpower.com
Page 45 of 88
Apps. Eng. 800 927.9474
800 735.6200
9. Modular AC Front-end System (ENMod)
Bus OK (BOK) Pin. (Figure 9–12) The Bus OK pin
is intended to provide early-warning power fail infor-
mation and is also referenced to the SR pin.
CAUTION: There is no input-to-output isolation in
the ENMods. It is necessary to monitor Bus OK via
an optoisolator if it is to be used on the secondary
(output) side of the converters. A line-isolation
transformer should be used when performing
scope measurements. Scope probes should never
be applied simultaneously to the input and output
as this will damage the module.
L, N Pins. Line and neutral input.
+ / – Pins. Positive and negative outputs.
SR Pin. Signal return for BOK and EN outputs.
FOR MINIHAM MODULE PIN CONNECTIONS
(Figure 9–1a)
Filter. (Figure 9–1b) The input EMI filter consists of dif-
ferential and common-mode chokes,Y-capacitors (line-
ground), and X-capacitors (line-line). This filter configu-
ration provides sufficient common-mode and differen-
tial-mode insertion loss in the frequency range
between 100 kHz and 30 MHz to comply with the
Class B conducted emissions limit, as illustrated in
Figures 9–10a thru 9–10c.
Hold-up Capacitors. Hold-up capacitor values should
be determined according to output bus voltage ripple,
power fail hold-up time, and ride-through time.
(Figure 9–13) Many applications require the power
supply to maintain output regulation during a
momentary power failure of specified duration, i.e.,
the converters must hold-up or ride-through such an
event while maintaining undisturbed output voltage
regulation. Similarly, many of these same systems
require notification of an impending power failure in
order to allow time to perform an orderly shutdown.
The energy stored on a capacitor which has been
charged to voltage V is:
ε
= 1/2(CV
2
)
(1)
where:
ε
= stored energy
C = capacitance
V = voltage across the capacitor
Energy is given up by the capacitors as they are
discharged by the converters. The energy expended
(the power-time product) is:
ε
= P
∆t = C(V
12
– V
22
) / 2
(2)
where: P = operating power
∆t = discharge interval
V
1
= capacitor voltage at the beginning of
∆t
V
2
= capacitor voltage at the end of
∆t
Rearranging Equation 2 to solve for the required
capacitance:
C = 2P
∆t / (V
12
– V
22
)
(3)
The power fail warning time (
∆t) is defined as the
interval between Bus OK and converter shutdown (EN)
as illustrated in Figure 9–13. The Bus OK and Enable
thresholds are 205 V and 190 V, respectively. A simplified
relationship between power fail warning time, operating
power, and bus capacitance is obtained by inserting these
constants in Equation (3):
C = 2P
∆t / (205
2
– 190
2
)
C = 2P
∆t / (5,925)
It should be noted that the series combination (C1, C2,
Figure 9–1a) requires each capacitor to be twice the calcu-
lated value, but the required voltage rating of each
capacitor is reduced to 200 V.
Allowable ripple voltage on the bus (or ripple current in
the capacitors) may define the capacitance requirement.
Consideration should be given to converter ripple rejection
and resulting output ripple voltage.
Equation 3 is again used to determine the required
capacitance. In this case, V1 and V2 are the instantaneous
values of bus voltage at the peaks and valleys (Figure
9–13) of the ripple, respectively. The capacitors must hold
up the bus voltage for the time interval (
∆t) between
peaks of the rectified line as given by:
∆t = (π – θ) / 2πf
(4)
where: f = line frequency
θ = rectifier conduction angle