Design requirements – Vicor Micro Family of DC-DC Converter User Manual
Page 16
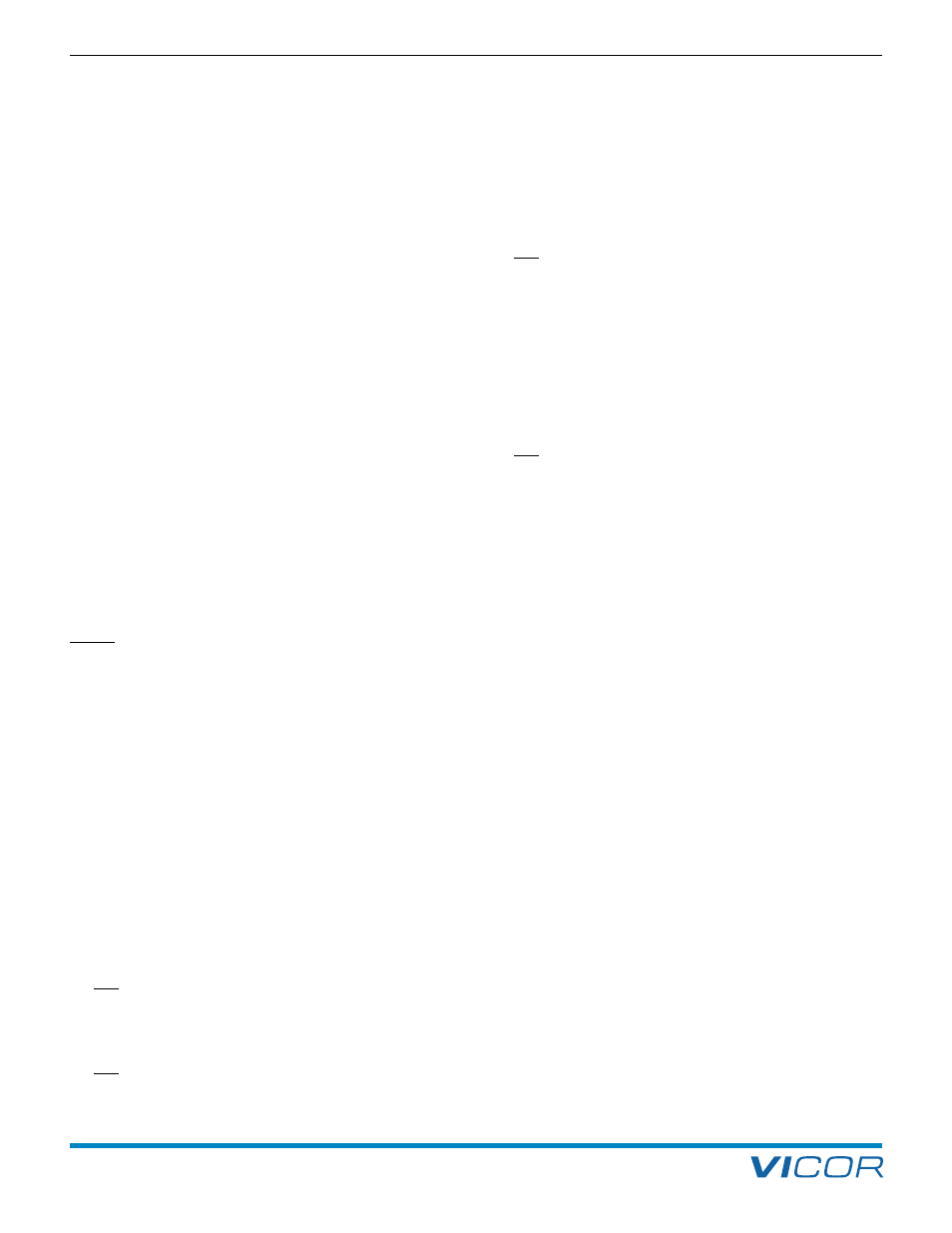
Design Guide & Applications Manual
For Maxi, Mini, Micro Family DC-DC Converters and Configurable Power Supplies
Maxi, Mini, Micro Design Guide
Rev 4.9
vicorpower.com
Page 15 of 88
Apps. Eng. 800 927.9474
800 735.6200
3. Design Requirements
To calculate the required source impedance, use the
following formula:
Z = 0.1(V
LL
)
2
/ P
in
where: Z is required input impedance
V
LL
is the low line input voltage
P
in
is the input power of the module
Filters, which precede the module, should be well damped
to prevent ringing when the input voltage is applied or
the load on the output of the module is abruptly changed.
INPUT TRANSIENTS AND SURGES
The voltage applied to the input of the module must not
exceed the ratings outlined in the data sheet. Protection
devices such as Zener diodes and MOVs should be used
to protect the module from short-duration transients.
These shunt protection devices are effective only if the
source impedance is high relative to the impedance of
the protection device when it is conducting. For voltage
surges where the abnormal voltage is present for a long
period of time, shunt protection devices can easily be
damaged by the power dissipated. For this type of
condition, a voltage limiter in series with the input of
the module may be the best solution. Vicor Applications
Engineering can assist in recommending the appropriate
type of protection for the module.
NOTE: Do not allow the rate of change of the
input voltage to exceed 10 V/µs for any input
voltage deviation.
SENSE LEADS (Mini and Maxi only)
The sense leads of the module must always terminate
either directly to the output pins (local sense) or at the
load (remote sense). When remote sense is used, the
output wiring impedance in combination with the load
impedance can cause significant loss of phase margin and
result in oscillation and possible damage to the module,
poor transient response, or activation of the output
overvoltage protection. Long sense leads may require a
compensation circuit for stability.
Protection circuitry is required if the possibility of reversed
sense leads can occur. Please contact Vicor Applications
Engineering for specific recommendations.
Do not exceed 1 V between –S and –Out leads. This is
an important consideration if the converter is used in a
Hot-Swap application. ORing diodes, if used, should be
located in the +Output lead to avoid exceeding this rating.
Do not exceed the rated power of the converter. The total
of the power consumed by the load plus the power lost in
conductors from the converter to the load must be less
than the output power rating of the converter.
OUTPUT CONNECTIONS
For systems designed to charge batteries, subject the
module output to dynamic loading, or loads that have
large reactive components, please contact Vicor
Applications Engineering to discuss your application
in detail.
Do not externally drive the output of the module 10%
above its nominal setpoint voltage.
Modules, that are used to charge batteries should be
applied with a diode in series with the output of the
module. The charge current must be externally controlled
to ensure that the module is not operated in excess of its
power or current rating.
Current-carrying conductors should be sized to minimize
voltage drops.
Do not use output ORing diodes with parallel arrays of
the Micro Family converters.
Output Overvoltage Protection (OVP). The OVP detection
circuitry within the converter is highly resistant to false
tripping. For the converter to shut down due to an OVP
condition two conditions must be satisfied (logical AND);
1. The voltage at the output terminals must be greater
than the OVP set point.
2. The secondary control IC within the converter must be
requesting a power conversion cycle from the internal
primary control IC.
By using this logic, false tripping of individual converters
due to externally induced OVP conditions such as load
dumps or, being driven by external voltage sources at the
output terminals is minimized. The user should not test
the OVP circuit by back driving the output terminals or by
any other means as the OVP circuitry is fully tested as part
of the inline manufacturing process.
OVERCURRENT PROTECTION
The Maxi, Mini, Micro converters incorporate a straight-
line type current limit. (Figure 3–1) As output current is
increased beyond Imax, the output voltage remains
constant and within its specified limits up to a point, I
KNEE
,
which is typically 5 – 25% greater than rated current,
Imax. Beyond I
KNEE
, the output voltage falls to Ishortcircuit.
Typically, modules will automatically recover after the over-
current condition is removed.