Zeroing the transducer interface, Zeroing the transducer interface 93, Zeroing the transducer – MTS SWIFT 10 MC Sensor User Manual
Page 93: Interface, For fixed mode, Spinning mode
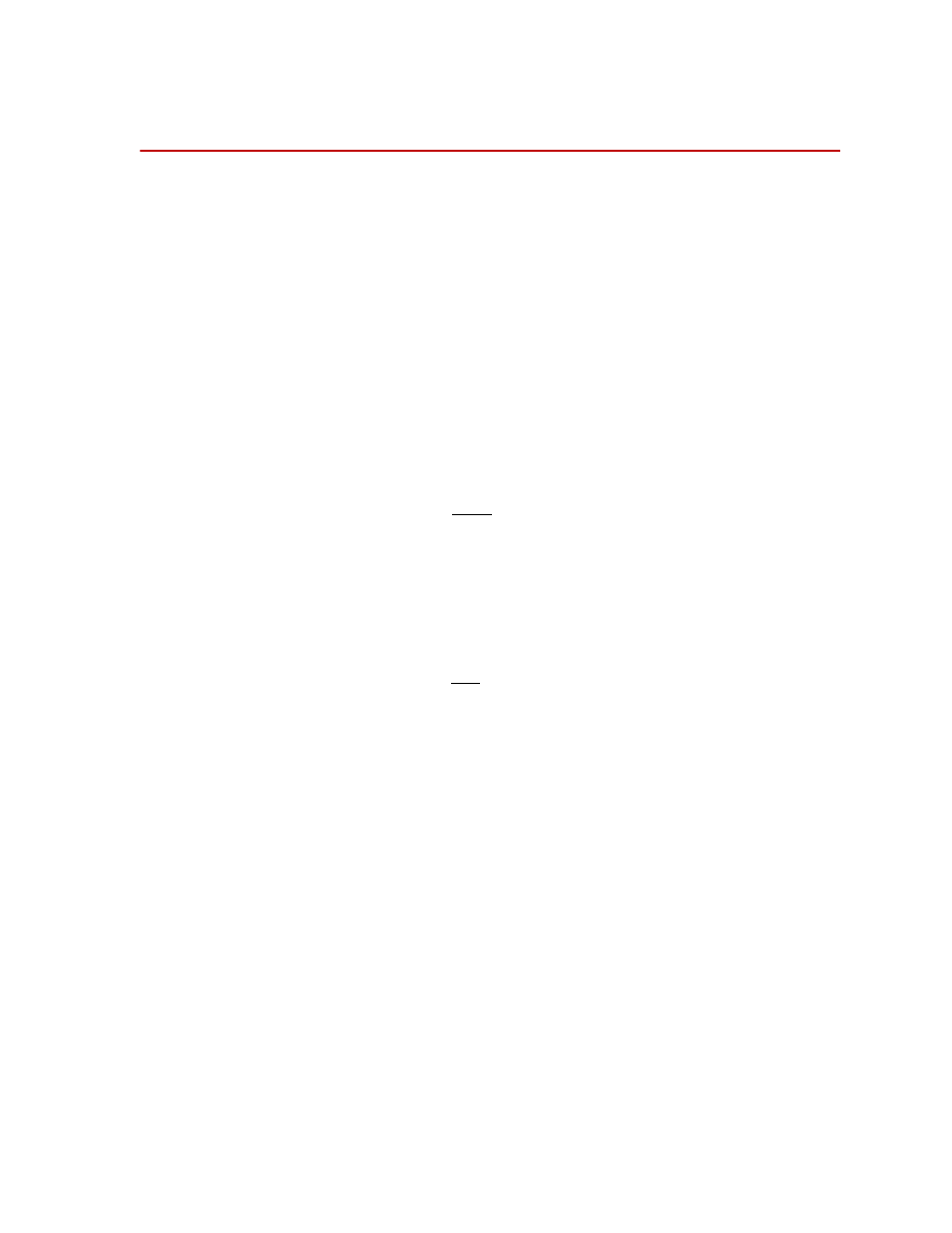
Zeroing the Transducer Interface
SWIFT 10 MC Sensors
Installing the Transducer
93
Zeroing the Transducer Interface
For fixed mode
For the non-spinning (fixed) zero mode, use the TI2Xfer to download the fixed
calibration file (serialnumberf.ca)l to the appropriate TI box. The angle mode in
the file should be:
AngleMode=1
Rotate the transducer such that the orientation labeling is consistent with the
reference orientation. In most cases, this means rotating the transducer so the
labels are upright.
If an additional angle correction is required after installation, you will need to
measure the angle from zero, and then enter the new value for the AngleFixed in
the TI calibration file (see earlier instructions
, “Edit the Calibration File,”
Zeroing the transducer in fixed mode can be performed before or after connecting
the adapter plate to the spindle housing.
•
Perform zero before connecting the adapter plate to the spindle housing if
you want to zero the transducer without the effects of the vehicle load on the
transducer.
With the transducer oriented as described above, press Zero on the TI Box.
Repeat for each transducer.
Return to Step 17 of the procedure,
Attaching SWIFT Components to the
Fixturing
to complete the installation.
•
Perform zero after connecting the adapter plate to the spindle housing if you
want to apply the vehicle load to the transducer before you zero the
transducer.
Return to Step 17 of the procedure,
Attaching SWIFT Components to the
Fixturing
to complete the installation.
With installation complete and the vehicle load on the transducers, press the
Zero button on each TI Box.
For spinning mode
For the spinning zero method, use the TI2Xfer to download the spinning
calibration file (serialnumbers.cal) to the appropriate TI box. The angle mode in
the file should be:
AngleMode=0
This zero method samples all active bridges at four 90° intervals (that is at 0°,
90°, 180°, and 270°). After the data is taken, all active channels are analyzed for
signal offsets, and the X and Z input channels are analyzed to determine the
angular zero point.
1. Rotate the adapter plate with the transducer attached one full revolution so
that the encoder can find the zero index mark.