MTS SWIFT 10 MC Sensor User Manual
Page 108
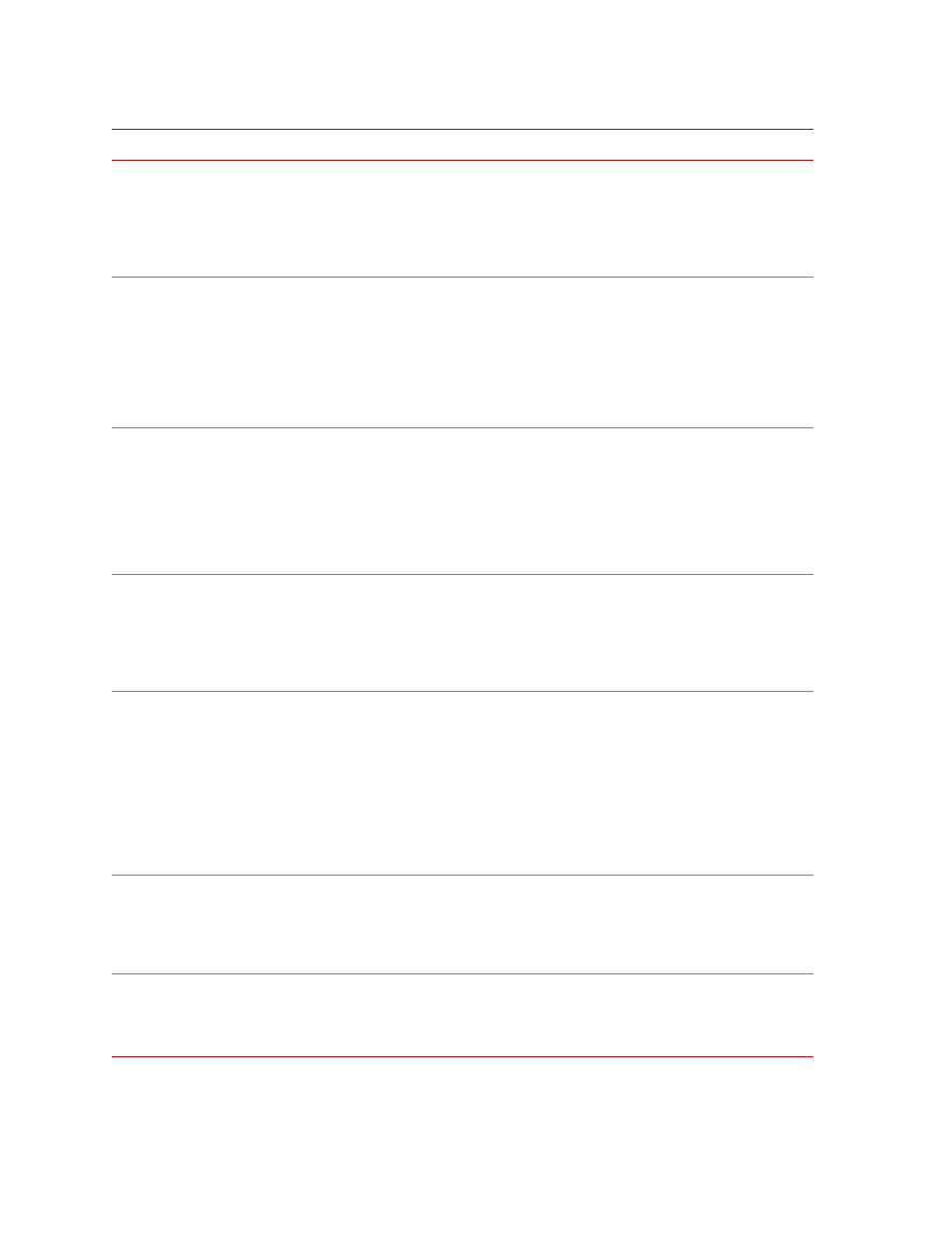
SWIFT 10 MC Sensors
108
Troubleshooting
The shunt reference values
were changed.
Use the TI2XFER program to upload the
current calibration file. Check the file to verify
that the variables ShuntDeltaRef are the same
as shown on the original calibration file
provided by MTS. The eight ShuntDeltaMeas
values should read approximately 0.85 V.
The shunt tolerance is not
set correctly.
Use the TI2XFER program to upload the
current calibration file. The ShuntTolerance
value should be set at 2, indicating an allowable
shunt variation of 2%. If this value is changed to
zero or a very small number, the difference
between the reference and the current shunt
measurement may fall outside of this tolerance
and be read as a shunt failure.
Transducer cable problems.
If the ShuntDeltaMeas values are not the same
as (or within tolerance of the ShuntDeltaRef
values), note which shunt values are not the
same.
If all values are not correct, check the signal
cable and power supply connections to ensure
the cables are undamaged and fastened securely.
Shunt mapping may be
incorrect that is, the wrong
calibration file is loaded in
the TI box or the shunt
mapping information in the
loaded file was changes
Use the TI2XFER program to upload the
current calibration file. Check the file to verify
that the variables Shunt#Bridge= are the same
as shown on the original calibration file
provided by MTS.
Shunt Calibration as
Recorded by External Data
Acquisition is incorrect or
inconsistent. (The internal
shunt check in the TI
electronics verifies each of
the eight individual
bridges, but it is the six
bridge 10 V output that you
can record if desired.)
The gains have been
changed in the calibration
file.
As the bridges are shunted, the raw bridge
outputs pass through the TI box and have the
calibration gains applied to them. If the
calibration file has been changed or modified,
the bridge 10 V outputs will reflect this. Use the
TI2XFER utility to verify that the calibration
settings portion of the calibration file matches
the original, and download the original to TI if
needed.
Data acquisition
configuration, settings,
offset, or scaling is
incorrect, changed, or
inconsistent
Investigate the data acquisition system to verify
that it is configured properly.
The output signal polarity
is incorrect
The Polarity setting for one
or more axes is incorrect
Check the polarity for each axis in the
calibration file and compare it with the desired
configuration as described in the
Troubleshooting Guide (part 7 of 10)
S
YMPTOM
P
OSSIBLE
C
AUSES
S
OLUTION