MTS SWIFT 10 MC Sensor User Manual
Page 103
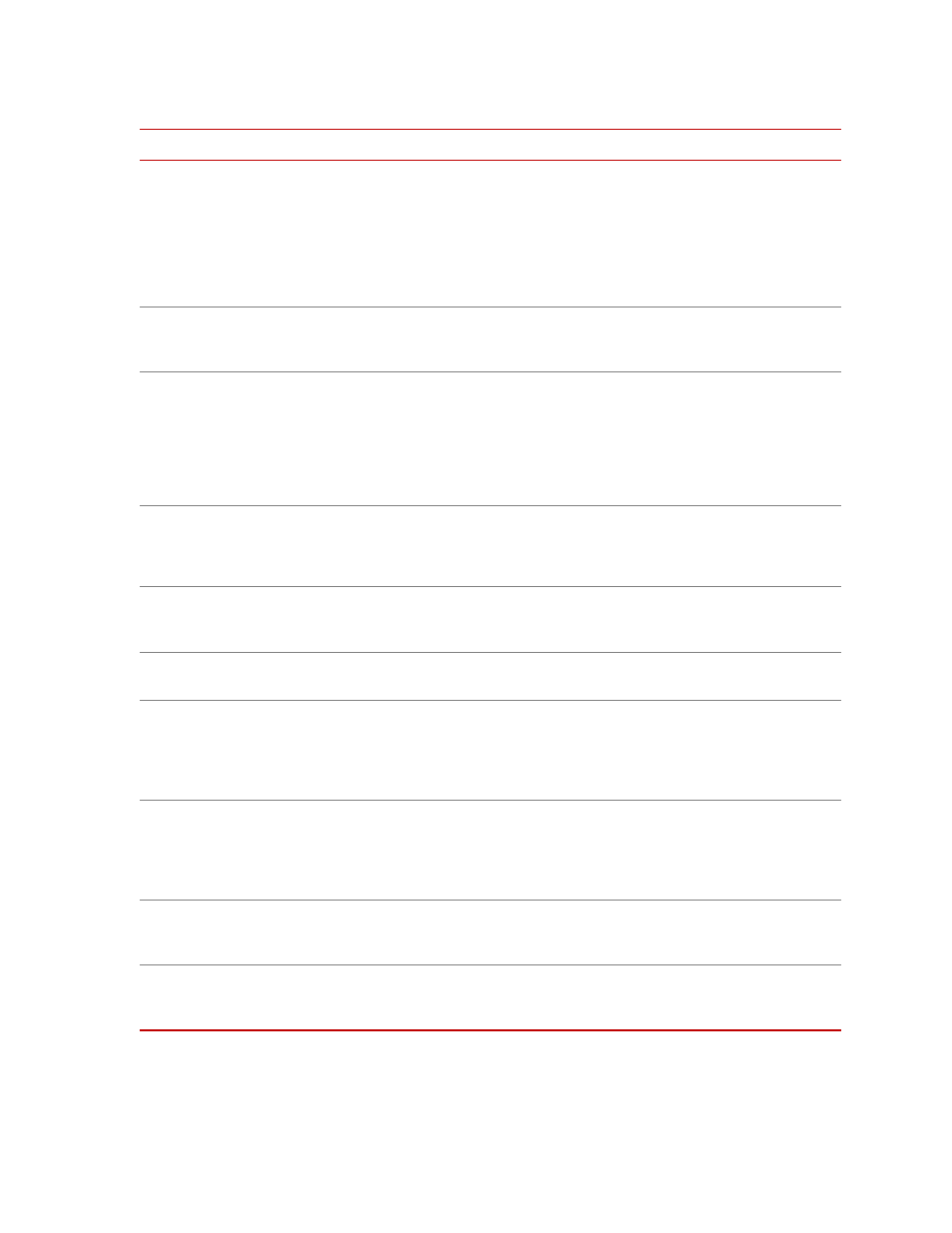
SWIFT 10 MC Sensors
Troubleshooting
103
Zero Procedure: The Zero
indicators stay on too long,
or they continue to blink
slowly, even after the wheel
has rotated twice.
The angular output signal is
not reaching the TI. If the
encoder signal is not
reaching the TI, it may
eventually time out and red
fail indicator will light.
Check that all cables are attached and
undamaged. In particular, check the main signal
cable from the transducer to the TI.
Check that the encoder output is present. The
angle output signal from the TI should be a 0–5
V sawtooth output while the transducer is
spinning at a constant velocity.
The EncoderSize parameter
in the calibration file is set
incorrectly.
Check that the EncoderSize parameter is set
properly for the slip ring (EncoderSize=2048).
The red fail indicator will
stay lit if there is no encoder
signal. If the encoder is
disconnected after data
collection has started, the
data collection will time out
and blink slowly.
If this signal is not present, check that the slip
ring/encoder assembly has not been damaged. If
you suspect encoder damage, swap the slip ring
assembly with a known functioning unit to
verify it. If the slip ring/encoder assembly is
damaged, call MTS or replace it with a spare
slip ring assembly.
Some or all transducer
output signals read 0 volts
at the TI output even when
a load is present.
The TI is not turned on.
Check that TI is turned on and the green power
indicator is lit.
The transducer signal cable
is not connected.
Check that the cable is connected between the
TI box and the slip ring (or connector housing
for a road simulator).
Output cables are not
connected.
Check that the output connectors are securely
fastened to the data acquisition device.
Cables or connectors are
damaged.
Check all cables and connectors, particularly the
power and transducer cable. Cables must be free
of nicks or cuts, and all connector pins shown
on the cable drawings must be present and not
bent.
Data acquisition
configuration, cabling, or
input ports are incorrect or
damaged.
Verify that the data acquisition is configured
correctly. While the TI is turned on and the
cable from the transducer to the TI is connected,
use a handheld DVM to verify output on
individual channels while they are being loaded.
The wrong calibration file is
loaded in the TI box
Verify the correct calibration file and if
necessary, download the correct file to the TI
box.
Grounding problem.
Check that there is a good signal-to-ground
connection between the TI power cable and the
negative terminal on the battery
Troubleshooting Guide (part 2 of 10)
S
YMPTOM
P
OSSIBLE
C
AUSES
S
OLUTION