3 frequency pilot control – Lenze 8615E User Manual
Page 76
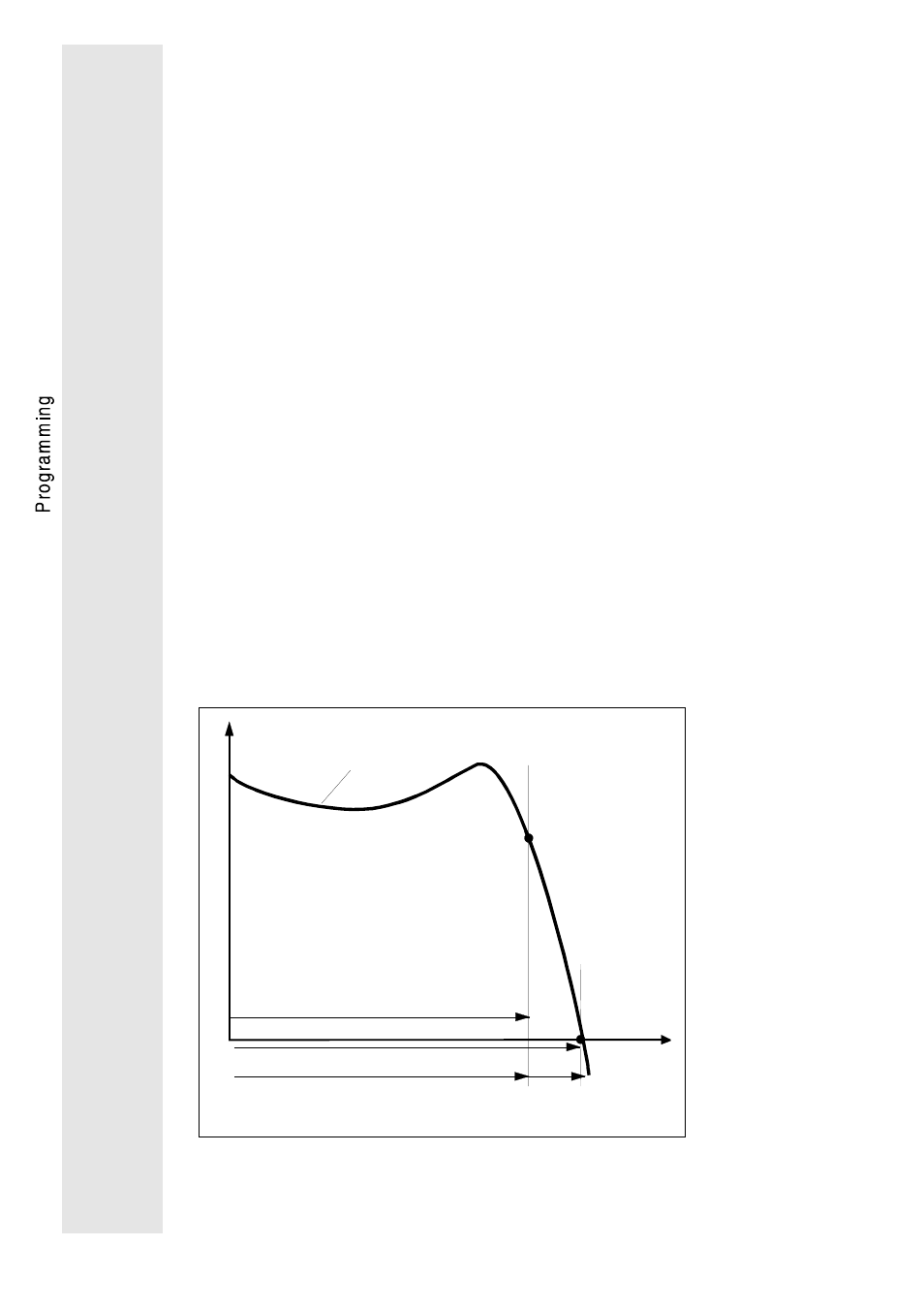
74
4.3
Frequency pilot control
For applications where the feedback signal is directly proportional
to the speed of the drive (actual speed) it is advantageous to pilot-
control the output frequency with the set-value or feedback. The
influence of the PI controller can be limited such that only the
maximum machine slip to be expected is controlled.
Set-value pilot control
A pilot control of the output frequency with the set-value offers the
advantage that the drive cannot accelerate unexpectedly if the
feedback signal fails (tacho failure). The ramp generator for the set-
value must be set correspondingly so that the drive is able to follow
set-value changes. (T
ir
-, T
if
setting as for frequency control).
Actual value pilot control
When the output frequency is pilot-controlled using the feedback,
the machine is supplied with the synchronous frequency which
corresponds to the actual speed, without the influence of the PI
controller (output signal = 0). The PI controller is only activated
effective if set-value and feedback are not identical. When the PI
controller increases or decreases the output frequency, a torque is
generated in the machine so that the drive accelerates in the
desired direction.
The advantage of feedback pilot control is that the set-value slew
rate does not have to be limited (T
ir
, T
if
= 0) and that the drive can
run through a large speed setting range with the set torque
−
according to the set influence of the PI controller.
A disadvantage is that the drive may accelerate unexpectedly in
the case of inadequate gain of the actual value.
If you want to use the feedback pilot control, first adjust the
feedback gain with set-value pilot control. After successful
adjustment you can then change to feedback pilot control.
M
Torque characteristic of the motor
f
d
Output frequency
Set-value=feedback
Pilot control of set-value/feedback
PI controller
signal
Stationary
operation