11 defining the cycle time of the plc project – Lenze EtherCAT Controller-based Automation User Manual
Page 161
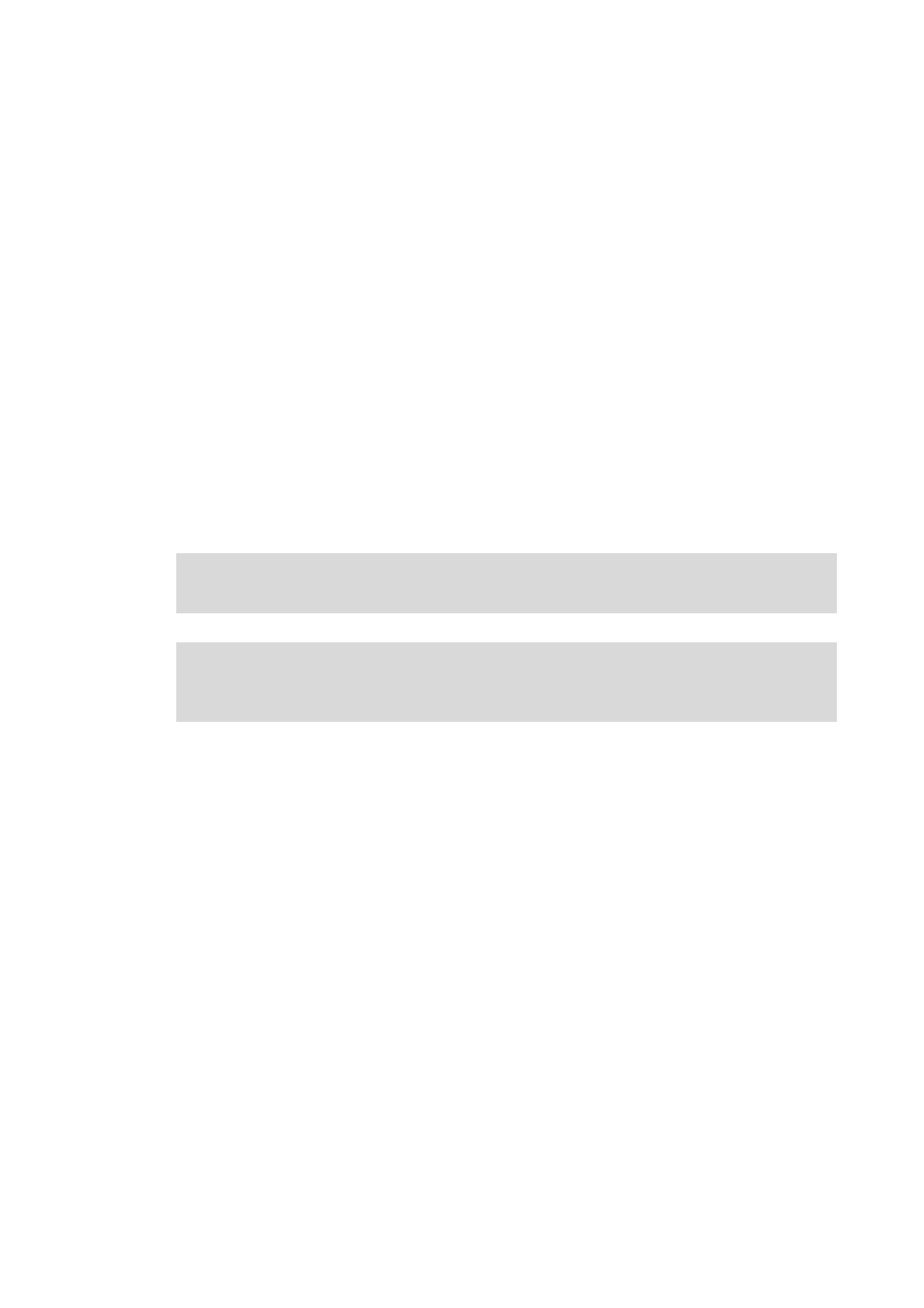
Lenze · Controller-based Automation · EtherCAT® Communication Manual · DMS 6.4 EN · 04/2014 · TD17
161
11
Defining the cycle time of the PLC project
11.1
Determining the task utilisation of the application
_ _ _ _ _ _ _ _ _ _ _ _ _ _ _ _ _ _ _ _ _ _ _ _ _ _ _ _ _ _ _ _ _ _ _ _ _ _ _ _ _ _ _ _ _ _ _ _ _ _ _ _ _ _ _ _ _ _ _ _ _ _ _ _
How to determine the task utilisation:
Initial situation: A complete project, e.g. with a EtherCAT task and 2 lower priority tasks has
been created.
1. For a first measurement of the task utilisation, set the cycle times of all cyclic tasks
available in the PLC system "high" (e.g. EtherCAT task = 10 ms, all other cyclic
tasks = 20 ms).
2. Use the menu command Online Login, or log in on the Lenze Controller with
• For this, the PLC program must be error-free.
• With the log-in, the fieldbus configuration and the PLC program are loaded into the
Controller.
3. Reset the values displayed on the Monitor tab of the Task Configuration to 0 after the
complete run-up of the system.
Execute the Reset command from the context menu of the task name field.
4. Read the displayed maximum computing time of the task with the highest priority.
In the illustration above, the max. cycle time of the EtherCAT task is 647 μs.
The minimum cycle time (T
min
) for a system can be calculated by means of the formula:
T
min
= Task utilisation x safety factor
Note!
A safety factor of 1.5 should be included in the calculation.