4 rear view mirrors – SkyTrak 6036 Service Manual User Manual
Page 44
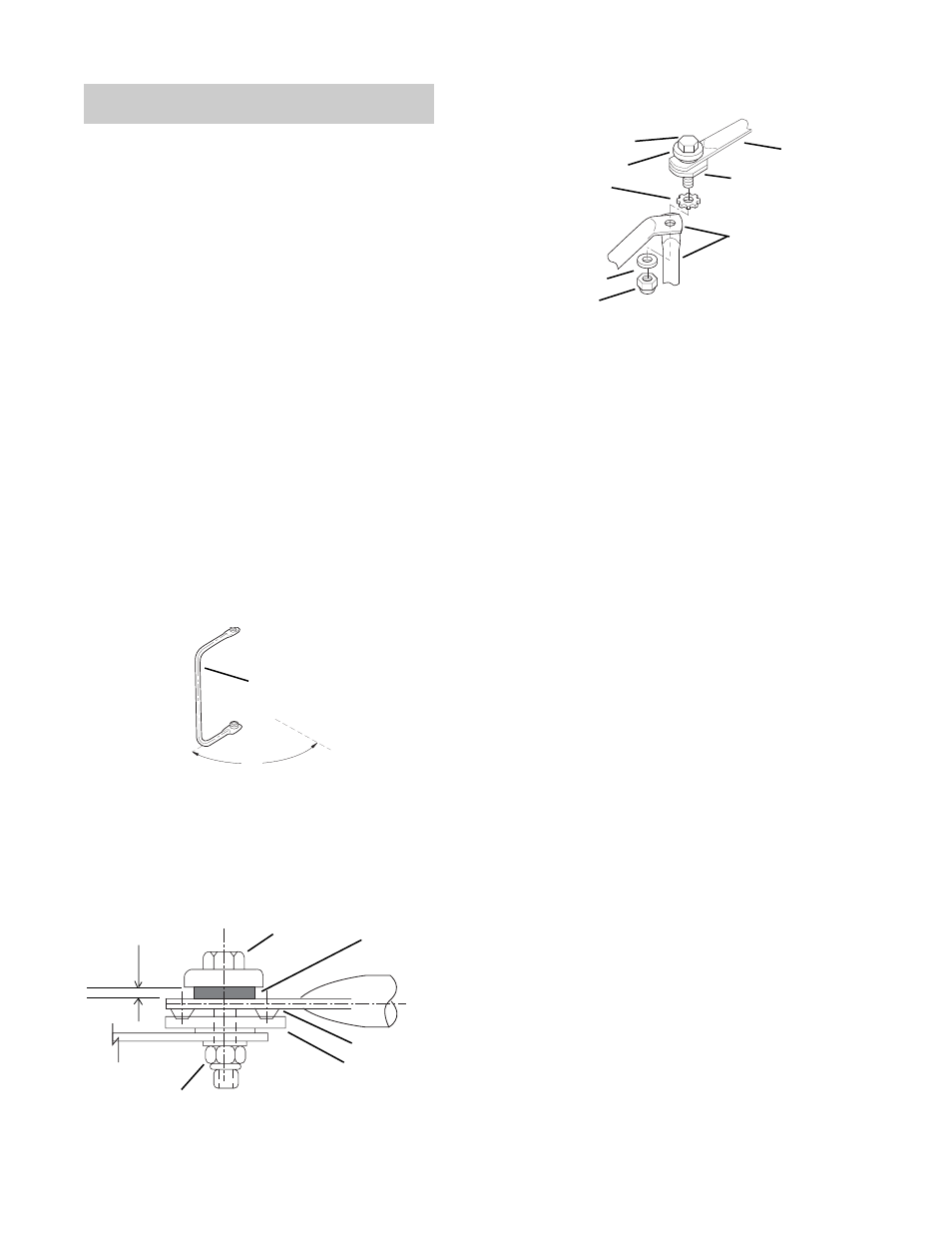
4-8
Model 6036 S/N 9B0499 and Before
Section 4.
Operator's Cab
3/16" (5 mm) GAP
PIVOT BOLT
TENSION
WASHER
LOCK PINS
BOTTOM NUT
LOCKPLATE
4.4
REAR VIEW MIRRORS
The forklift has two rear view mirrors.
• A 6-1/2 by 10" flat glass mirror on the cab
frame to the left of the operator.
• A 6-1/2 by 6" convex glass mirror on the
forklift frame to the right of the operator.
The mirrors have an outer gasket for edge shock
protection. If a mirror shatters, a replacement
mirror can be installed in the mirror head.
4.4.1 Mirror Head Adjustment
A “preset” locates the “home” position for each
mirror. When you swing a mirror outward a detent
locks the mirror in your preset viewing position.
This reduces the need for frequent mirror adjust-
ment.
You can swing the mirror assembly inboard to
reduce overall vehicle width for parking in tight
areas; the mirror will also pivot inboard upon
impact.
Adjust mirror “preset” as follows:
IMPORTANT: Before attempting to reposition a
mirror on a forklift which has just been received
from the factory, loosen the bottom nuts to permit
loop and mirror adjustment.
Fig. 4.10 Position Loop 90° from Side of Forklift
1.
Position the loops so they extend from the
side of the forklift, Fig. 4.10.
2. Adjust mirror heads for proper view. Evaluate
view from operator’s seat; change loop angle
and readjust each mirror if necessary.
3.
Tighten “preset” pivot bolt to a 3/16" (5 mm)
gap as shown in Fig. 4.11.
Fig. 4.12 Tighten Bottom Nut While Holding Pivot
Bolt Stationary
4.
Be sure lock pins are seated in lock plate as
shown in Fig. 4.12. Tighten bottom nut while
holding pivot bolt stationary. Then torque
bottom nut 250 to 300 lb-inch (28 to 34 N m).
This will lock the “preset” to its “home” posi-
tion. The effective torque value for your mirror
could vary slightly. The nut must be tight
enough to prevent the lock plate from rotating;
it must hold the mirror assembly in position
under forklift operating conditions and allow
the mirror to pivot freely when moved by hand.
5.
Check “preset” function by rotating loop back
and forth. A definite click will be heard and felt
as the loop is rotated past the “home” position.
6.
Return loop to “home” position. The loop
should snap firmly into place and the lock pins
should be firmly located in the holes of the
lock plate.
NOTE: Use all weather grease periodically on the
lock pins to maintain smooth operation.
4.4.2 Mirror Cleaning and Inspection
1.
The mirrors must be properly adjusted. They
must be kept free from condensation, frost,
ice, snow, dust and dirt. Rinse heavy grit from
mirror before you clean it with glass cleaner
and dry it with a soft cloth.
2.
Be especially careful when removing ice from
mirror to avoid breaking or scratching mirror.
You can use a nonmetallic scraper, heat or an
approved chemical to lower the freezing point
of the ice to aid in ice removal.
3.
Return each mirror to “home” position after
cleaning.
4.
Replace mirror glass if broken, damaged or
missing (the concave surface of the convex
mirror has a 21" radius).
5.
Replace mounting hardware if damaged or
missing.
Fig. 4.11 Tighten Pivot Bolt to
Provide a 3/16" (5 mm) Gap
LOOP
MA1470
MA1460
BOTTOM NUT
FLAT WASHER
LOCKPLATE
TUBING SUPPORT
BRACKETS
LOCK WASHER
PIVOT BOLT
RETAINING CAP
LOOP
MA1480
90°