SkyTrak 6036 Service Manual User Manual
Page 102
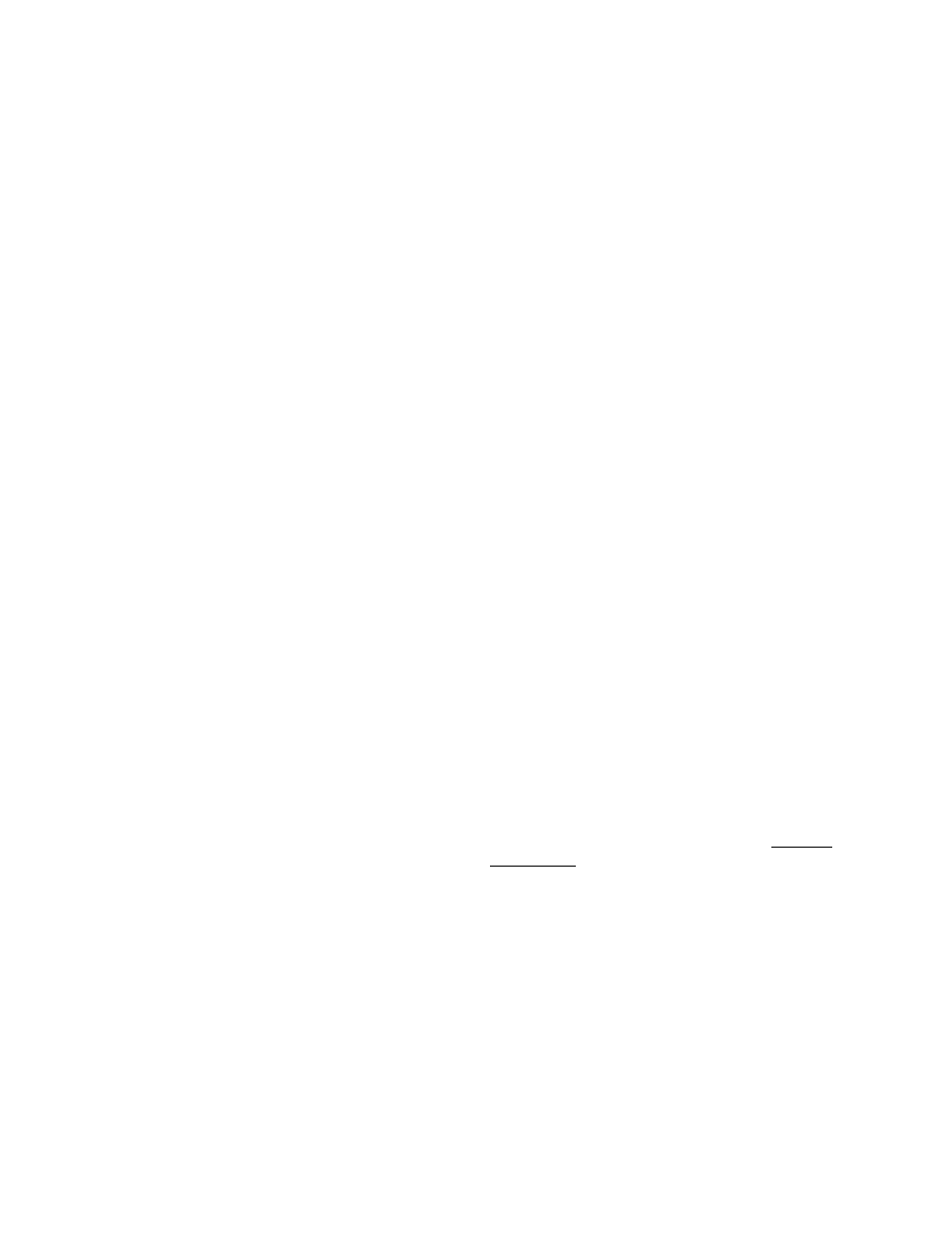
Section 8.
Engine
8-16
Model 6036 S/N 9B0499 and Before
e.
Fuel Injection Pump Installation
IMPORTANT: Instructions and specifications in
the Perkins Workshop Manual for the Perkins 4.236
Series Engine are required for fuel injection pump
installation. Do not remove pump from engine
unless you have this information which is essential
to correct fuel injection pump installation.
f.
Maximum Engine Speed Setting
IMPORTANT: The maximum speed screw seal of
the original fuel pump must not be broken or
tampered with in any way unless authorized by
JLG. Failure to do so may void engine and forklift
warranties.
When installing a replacement fuel injection pump
(refer to paragraph 8.4.7.e) or in the event of the
maximum speed screw having been moved, check
and reset the maximum no load speed.
The maximum no load speed will vary according to
application. For details, refer to code number
stamped on fuel injection pump data plate. The
last four numbers in the code indicate the speed
required. In the case of the following example, this
would be 3130 rev/min.
Code Example: AS62/800/0/3130
NOTE: If the fuel pump data plate is damaged or
defaced so as to make it impossible to read the
code, or if the code is not stamped on the plate,
contact your nearest Perkins Distributor or C.A.V.
dealer to obtain the correct setting.
IMPORTANT: Under no circumstances should the
engine be allowed to operate at a higher speed than
specified or severe damage to the engine may
result.
8.4.8 How to Bleed the Fuel System
See paragraph 8.1.5 - 500 Hour Intervals, Bleeding
Fuel System, for procedures to remove air from the
fuel system.
8.4.9 Atomizers (Fuel Injectors)
Atomizers should be taken out for examination at
regular intervals (refer to paragraph 8.1.7).
When replacing atomizers in the cylinder head it is
essential that a new, correct type copper washer is
installed between the nozzle cap and cylinder head.
Earlier engines have a one piece collar-type dust
seal; later engines have an improved two-piece
arrangement which consists of a soft rubber sealing
ring or sleeve and a rigid plastic spacer which
presses down onto the rubber sealing ring. The
rubber sealing ring is always installed below the
8.4.7 Fuel Injection Pump
The fuel injection pump, Fig. 8.22, is a distributor
type pump with a mechanical flyweight type
governor. The pump is flange mounted and is
driven from the engine timing case.
IMPORTANT: Unless the necessary equipment
and experienced personnel are available, disman-
tling of the fuel injection pump should not be
attempted.
a.
Fuel Injection Pump Removal
IMPORTANT: Instructions and specifications in
the Perkins Workshop Manual for the Perkins 4.236
Series Engine are required for fuel injection pump
installation. Do not remove pump from engine
unless you have this information which is essential
to correct fuel injection pump installation.
1.
Remove the high and low pressure pipes from
the fuel pump.
2.
Disconnect the stop and throttle controls and
remove return springs.
3.
Disconnect wiring to the fuel run solenoid.
4.
Remove the timing case front cover inspection
plate.
5.
Remove the three screws which secure the fuel
pump gear to the fuel pump.
6.
Remove the fuel pump from the timing case
ensuring that when the fuel pump gear leaves
the shaft it stays in mesh with the idler gear;
otherwise fuel pump timing will be affected.
b. Fuel Injection Pump Disassembly
IMPORTANT: Unless the necessary equipment
and experienced personnel are available, disman-
tling of the fuel injection pump should not be
attempted.
Refer to your Perkins Engine Distributor for disas-
sembly and servicing of your fuel injection pump.
c.
Cleaning and Drying
Clean the exterior of the fuel injection pump with an
approved solvent and dry with a clean lint-free
cloth.
d. Inspection and Replacement
Refer to your Perkins Engine Distributor if fuel
injection pump requires component replacement or
repair.