Dynaflow, User manual - maintenance – Ransburg DynaFlow User Manual User Manual
Page 72
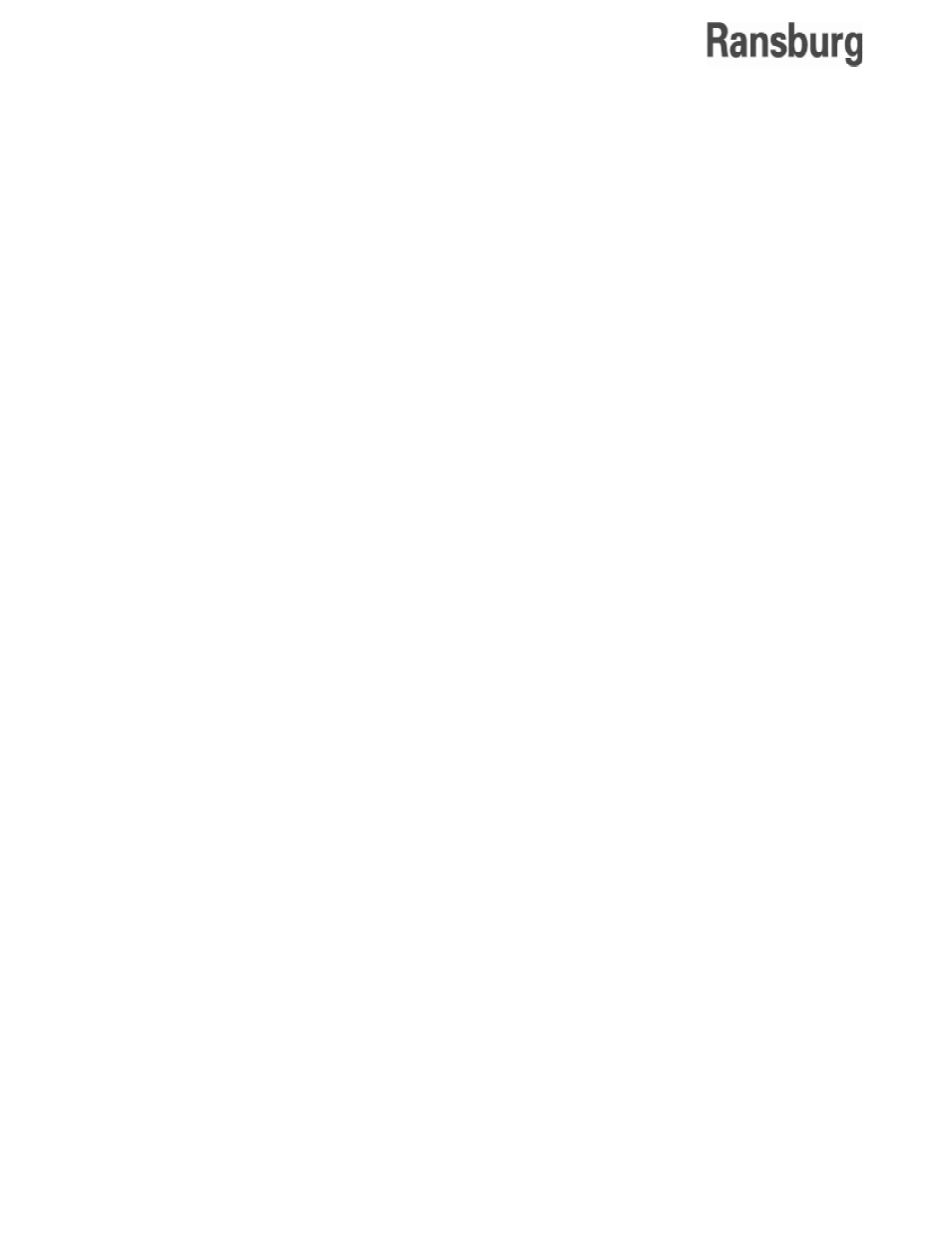
LN-9400-00.9
68
DynaFlow
TM
User Manual - Maintenance
forced ON. If the desired flow is achieved while
in this mode of operation, the fluid restriction is
located further downstream to the applicator.
4. Flow Meter Feedback
- Is flow being indicated on the controller?
If it is obvious that material is flowing through
the system (from the GUN or calibration ports if
used), but the controller indicates no flow, then
this indicates that the controller is not detecting
flow meter pulses. This could be caused by one
of the following:
•
Flow meter gear stuck
•
Bad flow meter sensor
•
Disconnected or damaged fiber-optic
cable
•
Bad fiber-optic receiver
•
Bad input on the CHANNEL MODULE
•
Fiber-optic flow meter transmitter battery
has expired. Life expectancy is two years
minimum.
Corrective Action:
Flow Meter: Disassemble, clean, and inspect
the flow meter. Refer to instructions supplied with
the meter.
Try connecting the flow meter in question to a fiber-
optic cable from a properly functioning CHANNEL.
If fluid flow is now observed, then the flow meter
and pickup sensor are functioning properly.
Fiber-Optic Cable: Simply shine a light into one
end of the cable and have someone observe the
opposite end. If light is visible through the cable
then it is probably good, although it is possible
that the cable is damaged and will not conduct
enough light to operate properly.
Fiber-Optic Detector: With fluid flowing, observe
the LED located on the fiber-optic receiver. The
LED is an indication that fluid is flowing and pulses
are being received from the flow meter. If the LED
is not ON, then replace or swap the fiber-optic
receiver and try again.
If everything checks good but no fluid flow is dis-
played, replace the CHANNEL MODULE. Make
sure that the hardware settings located on the
module are configured identically to the one be-
ing replaced.
5. Transducer Failure
Corrective Action:
Perform the following with the GUN OFF and
calibration valves closed. Place a pressure gage
(if one does not already exist) in the pilot line be-
tween the transducer and the fluid regulator. Make
sure that the air supply pressure to the transducer
is at least 100 psi. Go to the FORCE I/O menu for the
CHANNEL in question. Force Control Output volt-
age (or 4-20 ma) to several different values and
observe the pressure gauge. Reference "Analog
Sealing" chart in this section for correct values.
If the transducer does not produce the proper
pressures, check for air leaks in the air pilot tube,
transducer and fluid regulator. The transducers
are very low volume devices and are designed
for non-flow, or dead-headed operation. Also,
observe the pressure gauge for oscillation and
listen to the transducer for fluttering sounds. These
are other indications that there may be air leaks
in the system.
Another method for isolating small air leaks is to
spray or dab a small amount of a soap and water
solution around the fittings or valves and look for
the continuous formation of air bubbles.