Dynaflow, User manual - introduction – Ransburg DynaFlow User Manual User Manual
Page 16
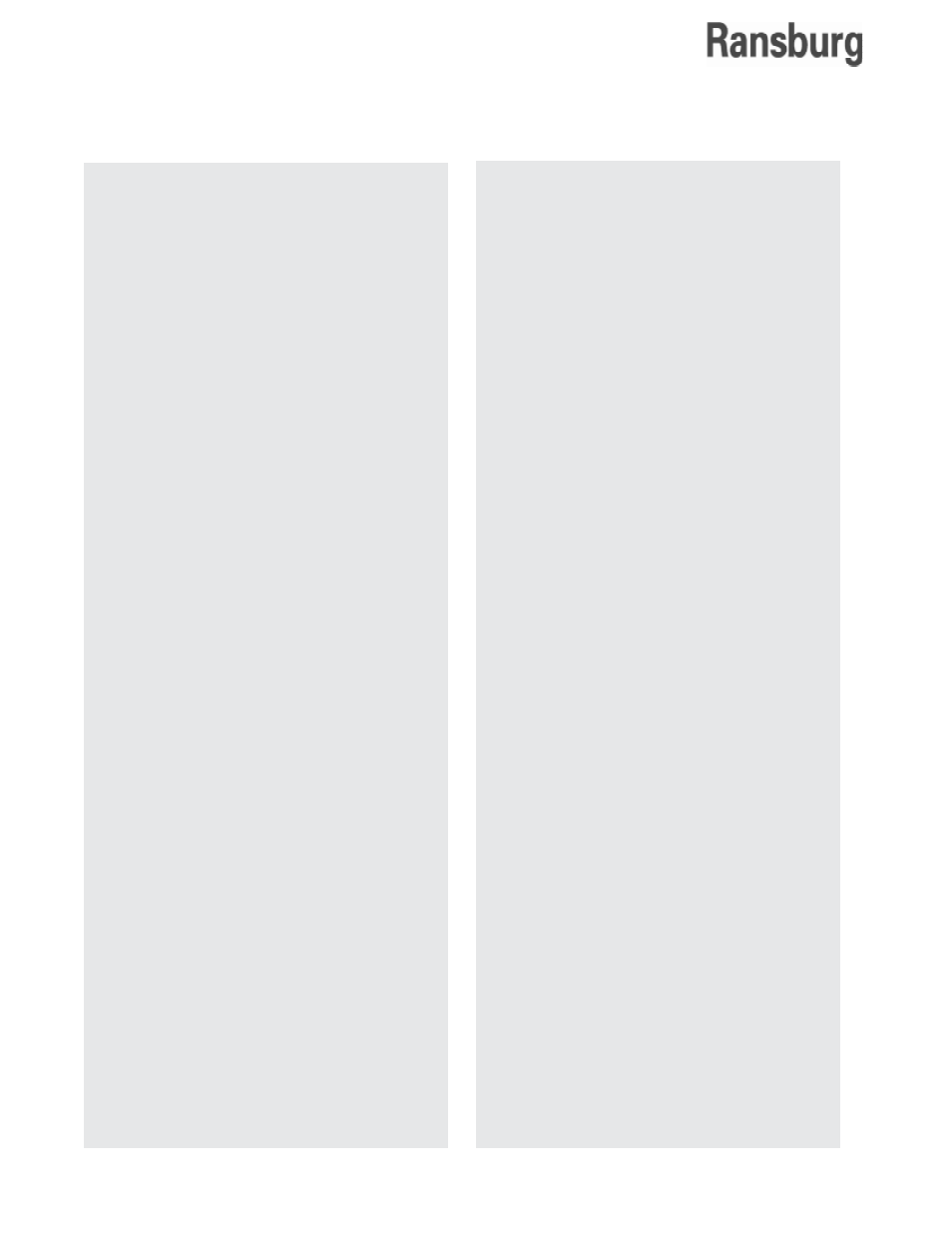
LN-9400-00.9
DynaFlow
TM
User Manual - Introduction
12
General:
Each Channel Module is responsible
for processing channel specific dis-
crete I/O and performing all of the
necessary PID closed loop control
functions. Data and control I/O other
than discrete is communicated
through Ransburg CAN Bus located
on the Motherboard.
Dimensions:
3U (130.5mm) H x 7H (35.2mm) W
standard 19" rack module
24 Digital Inputs
(2 Channels):
24 VDC at 2.3 ma typical per input
(optically isolated, source by default,
sink selectable)
Trigger (level): Automatic mode only - For
manual mode, fluid starts with fluid
flow on master channel.
Halt (edge): Stops current JOB # (no effect on
next JOB # in queue)
Clean (edge): Forces regulator full on for
cleaning
Run (edge): Gets next JOB # - used in conjunc-
tion with JOB # and Toggle select
bits
Gun Mask (edge): Used in conjunction with
JOB # select bits
Total Reset (edge): Resets all totals
Total Hold (level): Holds present total value
regardless of fluid flow
Transparent/PID (level): When active directs
the external analog input directly to
the transducer output
Analog Hold (level):
Freezes PID and holds cur-
rent analog control output
Load (edge): Loads fluid with controlled mix ratio
for GUNs operating in MANUAL
Mode
External Fault/
Enable (level): Enable signal input. Must
be active for fluid to be delivered by
GUN regardless of the operating
mode.
Spare:
Not used presently
Channel Module Hardware
Specifications
Channel Module Hardware
Specifications (Cont.)
12 Digital Outputs
(2 Channels):
24 VDC sourced at 300 ma max-
imum per output (Solid state relay
contacts)
Ready:
Everything is ready for operation,
configured correctly and I/O logic
OK
Active:
CHANNEL is active and controlling
Fault:
Fault has occurred
Pot Life Timer: Pot life timer expired
Clean/Load/Calibrate: Indicates Clean, Load, or
Calibrate mode is active
MVR Enable: Used to control trigger valve for
CHANNEL in fast trigger applica-
tions with Analog Hold enabled
4 Analog Inputs
(2 Channels):
Jumper selectable 0-10 VDC (de-
fault) or 4-20 ma, op-amp buffered,
10-bit A/D.
Set Point Control #1: Used for external analog
control. When used, offset and full
scale need to be set. This is
accomplished through the
MAXIMUM FLOW RATE and
MINI-
MUM FLOW RATE JOB
parameters.
Set Point Control #2: Used for external analog
10-bit A/D control. When used, off-
set and full scale need to be set.
This is accomplished through the
MAXIMUM FLOW RATE and
MINIMUM FLOW RATE JOB
parameters.
Spare #1: Not used presently
Spare #2: Not used presently
4 Analog Outputs
(2 Channels):
Jumper selectable 0-10 VDC (de-
fault) or 4-20 ma, op-amp buffered,
12-bit D/A.
Transducer Control #1: Output to proportional
E/P 12-bit D/A controller
Transducer Control #2: Output to proportional
E/P controller
Flow Rate #1: Flow Rate (scaled between MINI-
MUM FLOW RATE and MAXI-
MUM FLOW RATE
JOB param-
eters)
Flow Rate #2: Flow Rate (scaled between MINI
MUM FLOW RATE and MAXIMUM