Automatic gun applications, Error log (f11), Dynamic flow rate set point control – Ransburg DynaFlow User Manual User Manual
Page 48: Dynaflow, User manual - operation
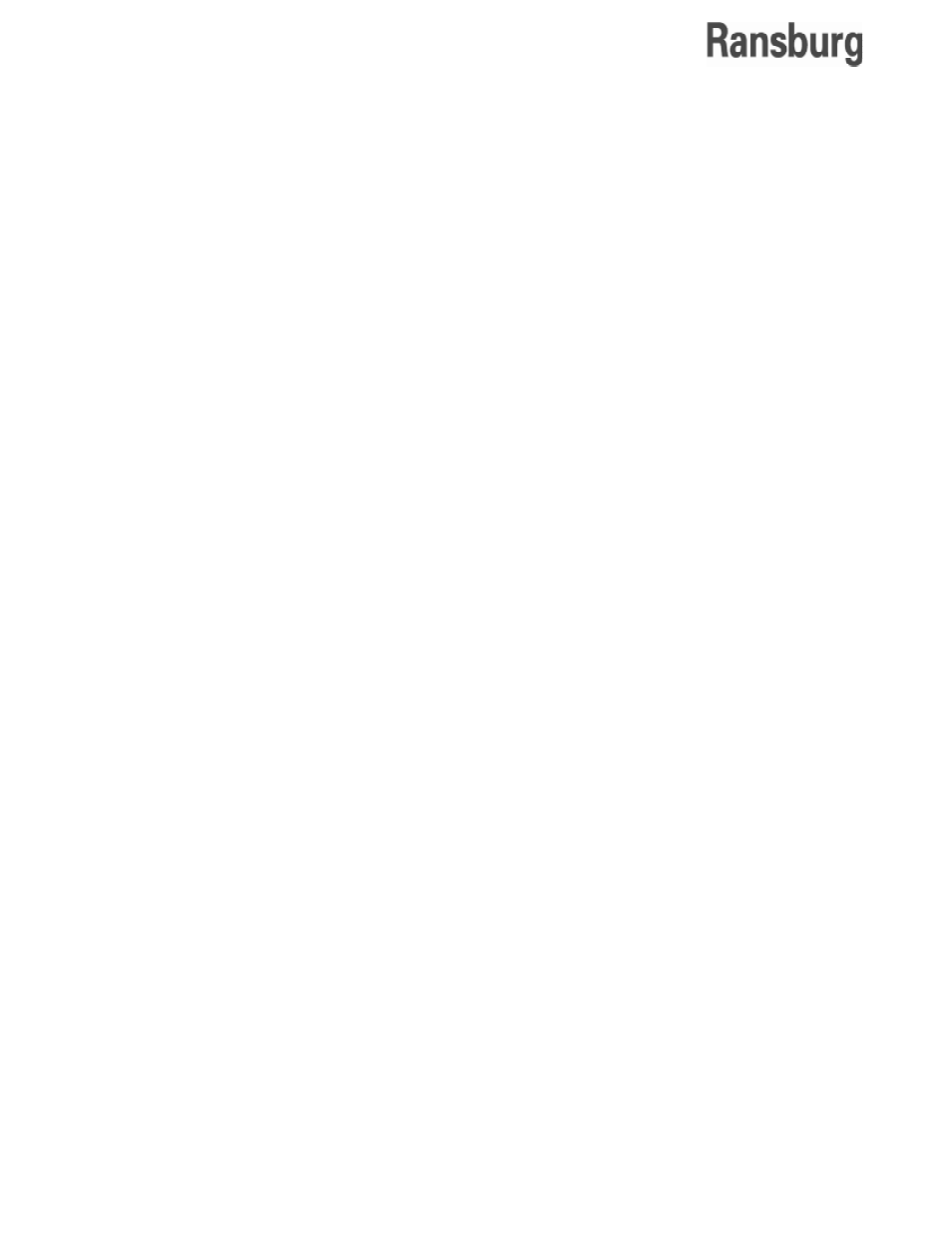
LN-9400-00.9
ERROR LOG (F11)
- Also See Section on Error Codes
Each ERROR CODE can represent a CHANNEL,
GUN or system error. See the Troubleshooting
section for list of error codes. It is possible for
more than one code to be issued at the same time.
The Interface Module stores ten (10) previous
error codes until they are read by the Local
Operator Interface program at which time they
are automatically purged from its log. The Local
Operator Interface program stores one hundred
(100) previous error codes until they are manu-
ally cleared by the operator. The operator may
also save the error codes to a floppy diskette for
later analysis.
A PLC may obtain the current error conditions via
RIO at any time, but it must maintain its own log.
AUTOMATIC GUN
APPLICATIONS
Automatic applicators use automatic means to
vary the fluid flow through the use of transducers
and material regulators. When used with single-
component materials and an automatic spray
applicator, the DynaFlow controller regulates total
material flow.
When used with two-component materials, the
DynaFlow controller regulates both the total fluid
flow rates to the applicator and the mixing ratios.
Each CHANNEL of the two-component material
is programmed with predetermined values.
The following conditions must be met in order for
the GUN to allow fluid flow:
1. There must be no system faults or GUN
faults active.
2. There must be valid GUN configurations.
3. The proper inputs must be supplied.
When a GUN is placed in the RUN MODE, the
controller sends a signal to the transducer to open
to the MVR LOW setting (default = 0 VDC). On the
first receipt of a trigger signal, the master channel
immediately starts its closed loop (PID) control
and updates the information to the transducer at
a rate determined by the PID Update Time (default
= 30ms) to adjust the actual flow rate to match
the target flow.
At the same time, in a two-component system, the
slave channel (catalyst) also closes its PID control
loop and matches the actual flow rate to the target
flow rate as determined by the requested flow rate
ratio of the Master CHANNEL (resin) and slaved
CHANNEL (catalyst).
Both channels run closed loop, independently
of each other. If either CHANNEL is not able to
achieve the required target flow rate, a FLOW TOO
LOW or FLOW TOO HIGH fault will be issued by
the controller for the offending channel.
After an amount of material has passed through
the Master CHANNEL (set by the TOLERANCE
VOLUME parameter), the DynaFlow controller
compares that volume with the volume of the
catalyst that flowed during that volume interval. If
the ratio is outside of the tolerance as set by the
FLOW TOLERANCE parameter, the DynaFlow
controller will issue an OUT OF TOLERANCE
fault for the offending GUN.
Dynamic Flow Rate Set Point Control
Dynamic Flow Rate Set Point Control is useful
for changing flow rates of a material to achieve
different coating thickness over different areas of
the same part. Several examples are shown in
the "Analog Control Settings chart" in this section.
In automatic GUN applications, the total flow rate
set point for the GUN may be varied in real time
using either of two methods; Remote I/O (RIO)
or Analog Input. If the RIO Set Point is zero and
Analog Input Set Point is less than 0.25 volts, the
Total Flow Rate set point comes from the JOB.
DynaFlow
TM
User Manual - Operation
44