Ransburg DynaFlow User Manual User Manual
Page 37
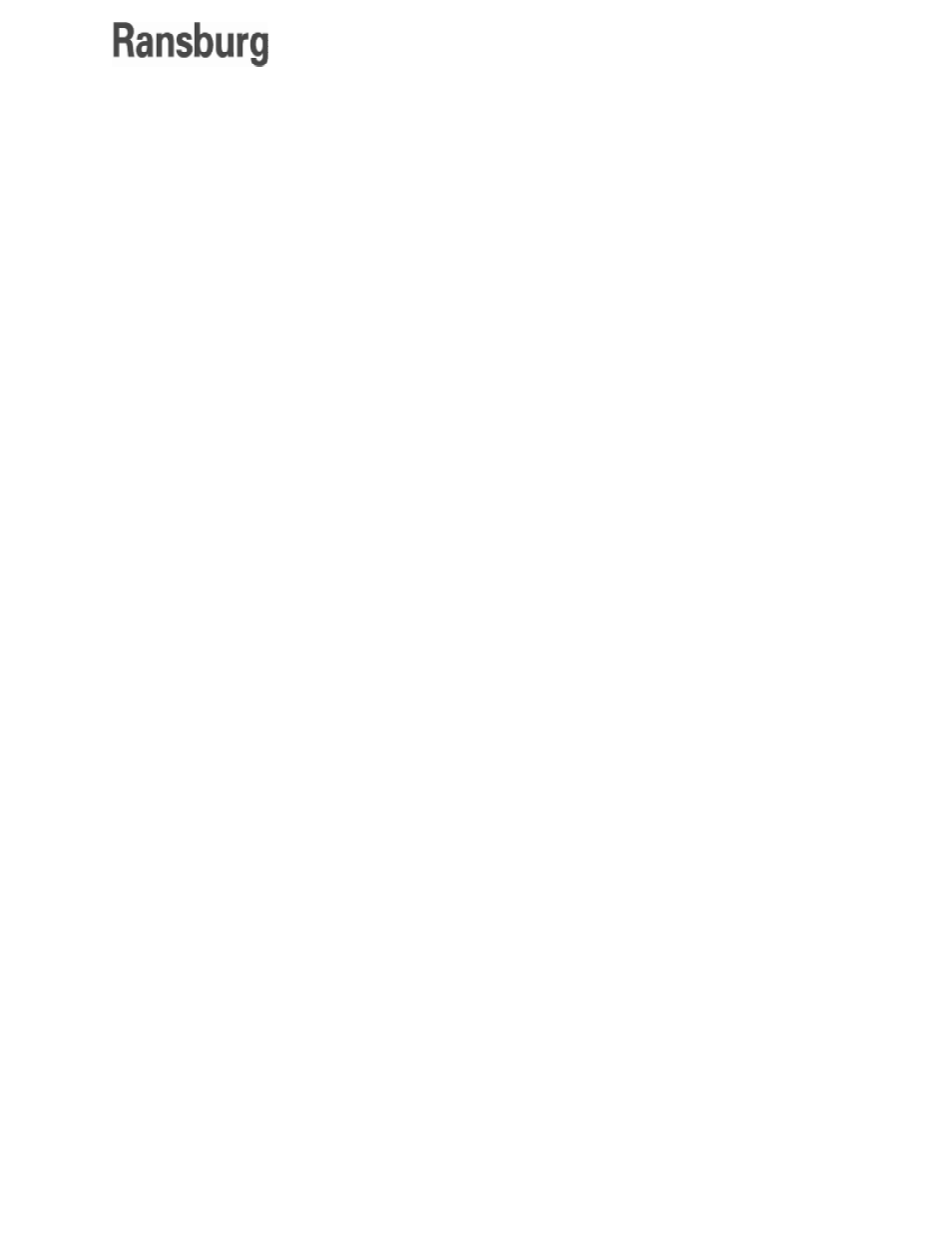
LN-9400-00.9
Trigger OFF Delay
For automatic GUNs only. This parameter has two
uses, depending on the position of DIP SW1-2 (or
SW1-6) on the Channel Module.
In applications where the trigger off pneumatic
action is slow, DIP switch SW1-2 (or SW1-6) on
the Channel Module should be turned off so that
when the GUN trigger signal is removed, the PID
loop for the CHANNEL will continue to control the
output of the MVR valve for the CHANNEL based
on the measured flow rate until the end of the
Trigger OFF Delay.
In applications where the trigger off pneumatic
action is fast, DIP switch SW1-2 (or SW-1-6) on
the Channel Card should be turned on so that
when the GUN trigger signal is removed, the PID
loop for the CHANNEL holds at the last output
value until the end of the Trigger OFF Delay. In
this case, it is recommended that a trigger valve
(color control valve) be installed at the inlet of
the MVR valve. This valve should be driven by a
solenoid controlled by the MVR Enable signal for
the CHANNEL. In this way, the fluid line will not
pressurize to the material supply pressure while
the GUN is not triggered and there will be no
delay in initiating flow when the trigger is turned
on again, since the MVR valve is already at the
position last commanded by the PID loop for the
CHANNEL. If a triger valve is not installed at
the inlet of the MVR valve, then the Trigger OFF
Delay should not be set greater than perhaps 0.5
seconds to avoid pressurization of the fluid line
during the Trigger OFF Delay. If the delay is too
long in this situation, excessive material may be
released when the trigger is turned on again due
to the higher pressure in the fluid line.
In either case, the CHANNEL output returns to
the MVR LOW value at the end of the Trigger
OFF Delay.
Trigger ON Delay
For automatic GUNs only. This parameter allows
the user to create a delay between the time when
the controller receives a trigger ON signal from a
remote device to when it actually starts the flow
of material. This parameter should be used only
in special situations where pneumatic delays
present a problem.
Master and Slave Regulator Type
The channel hardware configuration is stored as
this parameter. It is necessary for the controller
to know which fluid regulator type is being used
so that the proper default PID control parameters
can be loaded (Kp, Ki, Kd).
Reverse Flow Volume
The amount of fluid which is allowed to flow back-
wards in the GUN before the controller faults.
Reverse flow could cause catalyzed material to
backup into either fluid line if a check valve fails.
Keep this value small to minimize that possibil-
ity. If the GUN is configured for two-component
operation, than the Reverse Flow value will apply
to each of the CHANNELs assigned to the GUN.
Reverse flow rate is displayed on the main screen
of the Local Operator Interface as a flow rate bar
colored red, instead of green for normal flow rate.
Bar Chart Maximum Flow Rate
This parameter determines what flow rate is in-
dicated at the top of the bar-graphs on the main
screen and determines the maximum values dis-
played on the plot graph screens.
Flow Rate Tolerance Time
This parameter allows the user to program how
long the flow rate can continue to operate outside
of the programmed flow tolerance percentage be-
fore the unit fualts and stops flow. It is expressed
in seconds. If this number is too small, nuisance
flow out of tolerance faults may occur and if too
large, improper film builds could result.
Master Pot Volume
This is the volume of material that a pressure pot
will be filled with each time it is refilled. There is a
pot-volume reset button on the Job Totals screen
that allows the user to preset these volumes when
the pots are filled. This value is incremented
downwardly as material in the pot is consumed
and pot empty fault will occur if the volume ever
reaches the value of 0, warning the operator to
refill the pot(s).
Slave Pot Volume
See "Master Pot Volume" information.
33