Dynaflow, User manual - operation – Ransburg DynaFlow User Manual User Manual
Page 40
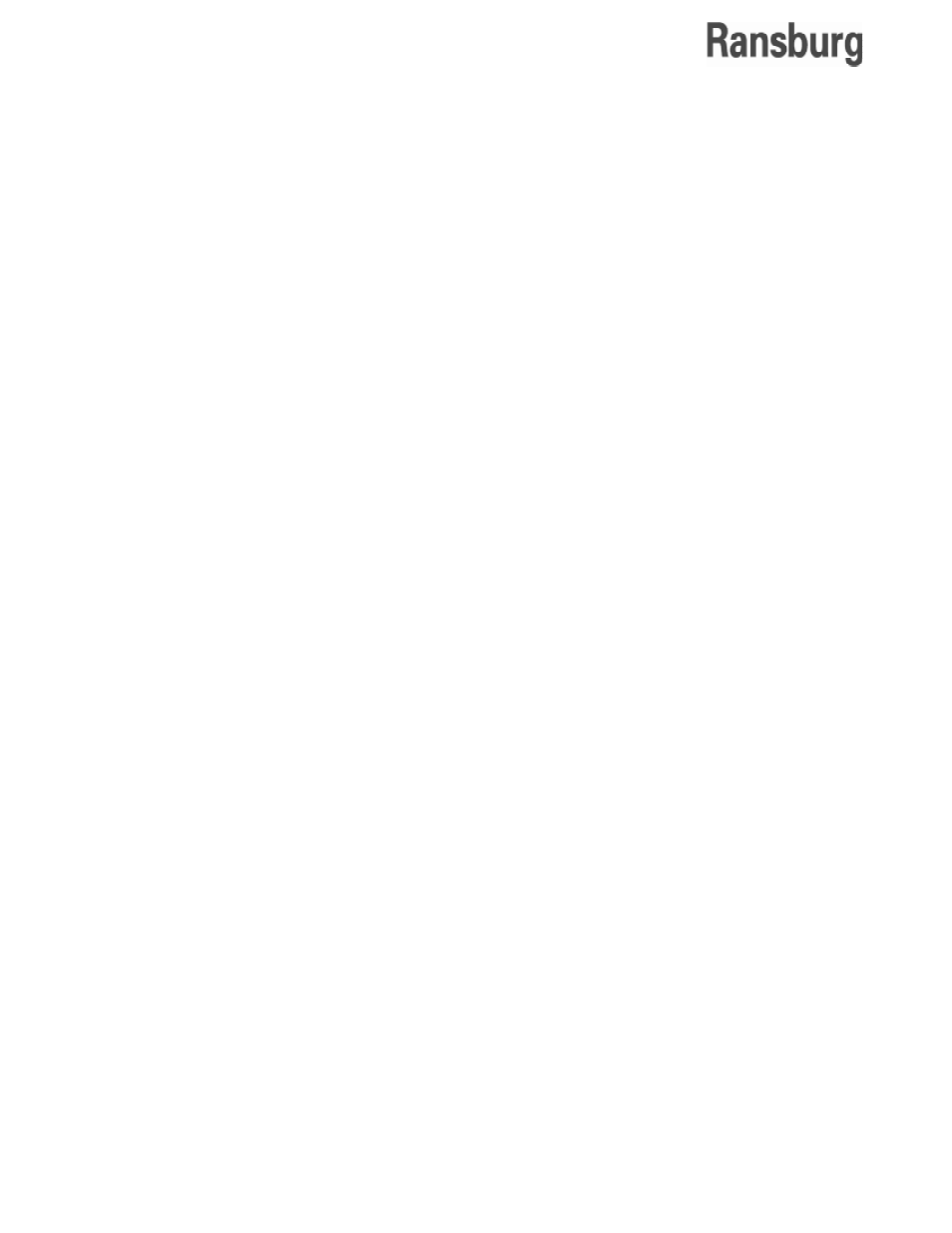
LN-9400-00.9
DynaFlow
TM
User Manual - Operation
36
Deadband would be between 95 and 105 cc/min.
The PID controller would therefore be suspended
whenever the actual flow rate is within this range.
This parameter should normally be set to 1 cc/min.
Proportional Gain (Kp) (Master and
Slave)
The proportional PID controller gain mainly affects
the response of the DynaFlow system to distur-
bances. The DynaFlow system may operate with
Kp at zero, however response to material supply
and delivery pressure disturbances will be poor.
The value of Kp is divided internally by a factor
of 1,000 and is used as a multiplier for the flow
rate error term. The flow rate error term is the
difference between the set point and actual flow
rate for the CHANNEL.
Integral Gain (Ki) (Master and Slave)
The integral PID controller gain mainly affects the
steady-state (non-transitional) response of the
DynaFlow system. The DynaFlow system must
have a non-zero value for Ki to operate properly.
The valve of Ki is divided internally by a factor of
100,000 and is used as a multiplier, along with a
factor of 3, for the sum of the error term over the
time the trigger has been turned on.
Derivative Gain (Kd) (Master and Slave)
The differential PID controller gain mainly affects
the response of the DynaFlow system to distur-
bances caused by disturbances that are slow in
nature. Normally, the DynaFlow system may op-
erate with a Kd value of zero. The value of Kd is
divided internally by a factor of 1,000 and is used
as a multiplier, along with a factor of 1/3, for the
rate of change in the error term.
MVR Low Pressure (Master and Slave)
This parameter allows the operator to set the low
limit on the pressure sent to the fluid regulator
while in the Run or Load modes. It can be used
to cause a faster response by the transducer/
regulator system. It should be adjusted so that
the regulator valve is just short of opening. With
a standard MVR valve, this value should never
exceed 30 psi. If this value is too high, continuous
FLOW TOO HIGH faults will occur.
When a GUN is configured for two-component
operation and the Ratio is 99.0:1, or greater, the
GUN is said to be operating in pseudo single-
component mode. In this case, the slave (catalyst)
CHANNEL is NOT set to MVR LOW when the GUN
is placed in either Run or Load modes. However,
if the slave (catalyst) CHANNEL is specified as
a clean CHANNEL, it will be turned on to MVR
HIGH in Clean mode.
MVR High and MVR Low Effect On PID
Operation
The PID will only output transducer pressures
between MVR LOW and MVR HIGH.
Pulses/Liter (Master and Slave)
The number of pulses sent from the flow meter to
the controller for each unit of fluid flow. Each pulse
represents a volume of fluid and is dependent
on flow meter size. This value can be verified or
adjusted during a calibration process to achieve
the best accuracy (See "Calibration Mode" in
the "Operation" section of this manual). The cali-
bration of all flow meters should be periodically
checked. The rheology of some fluids may effect
the calibration values, therefore a different value
for pulses per liter may be used for each material
and is entered into the JOB data tables.
Deadband (Master and Slave)
This represents a flow rate range divided equally
above and below the set point flow rate in which the
PID controll is suspended. This keeps the control
output from continually changing and produces
stability when close to the requested value. For
example, if the Deadband is set for 5 cc/min and
flow rate set point is set for 100 cc/min, the