Dynaflow, User manual - maintenance, Flow too low -or- flow too high – Ransburg DynaFlow User Manual User Manual
Page 71
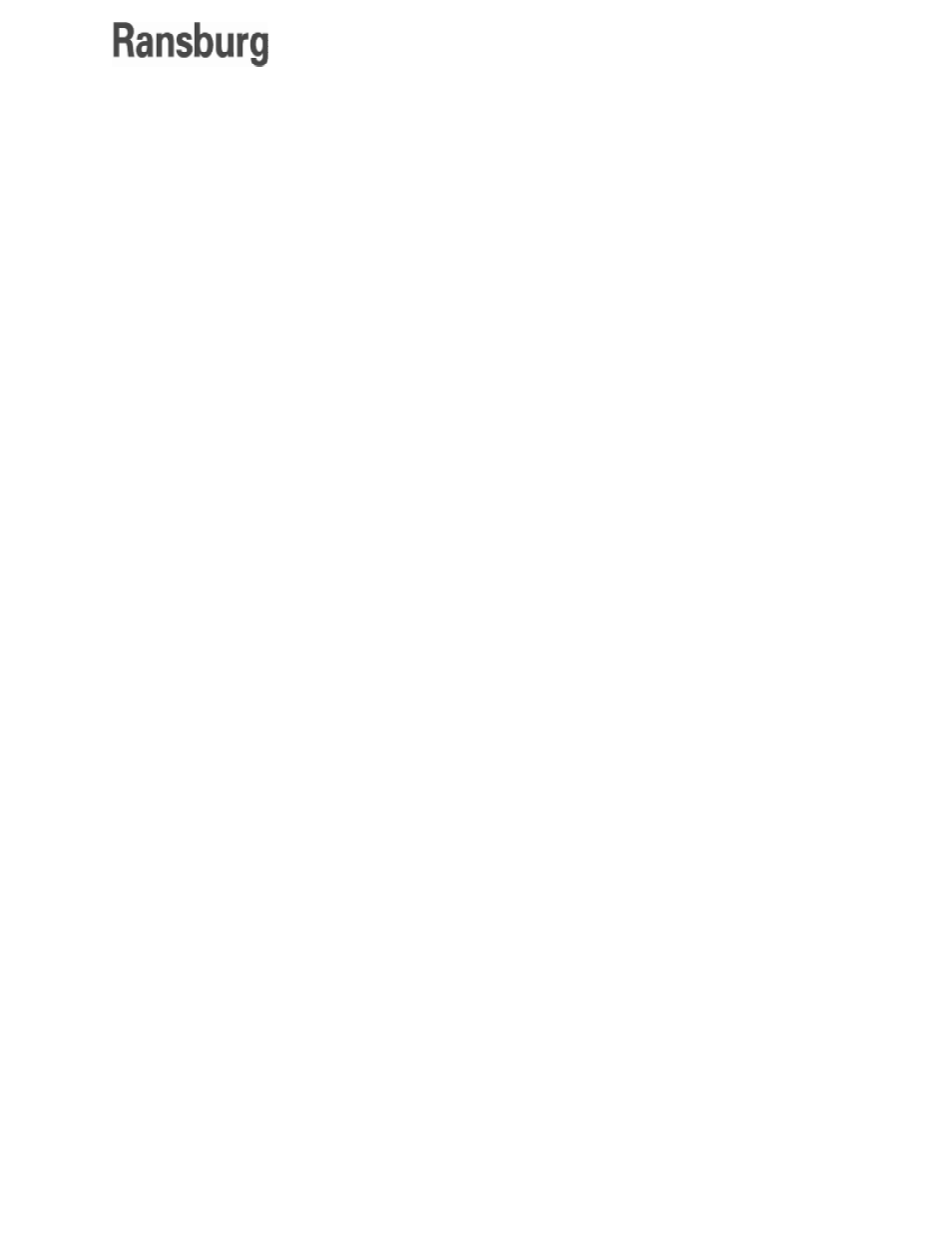
LN-9400-00.9
DynaFlow
TM
User Manual - Maintenance
67
Flow Too Low -or- Flow Too High
Explanation: These are CHANNEL specific faults.
FLOW TOO HIGH and FLOW TOO LOW faults
are issued if the requested fluid flow cannot be
obtained. This typically means that there is a setup
problem, maintenance issue, or mechanical failure.
These types of faults can be caused by numer-
ous problems. Most of the more common causes
are listed below. Keep in mind that the controller
senses that either too little or too much material is
getting to the applicator and that this is based on
JOB parameter settings and fluid flow feedback
from the flow meters. This troubleshooting section
assumes that the system was previously operat-
ing successfully and then a problem developed.
The following is not meant for initial system setup,
however, many of the troubleshooting procedures
described can be used in either case.
1. Material Supply Pressure
- Has the material supply pressure changed?
- What was the supply pressure when the
system was operating properly?
- Is the pressure gauge accurate or reliable?
- Has the fluid delivery system been
changed?
- Are there any air leaks in the fluid regulator
pilot line?
- Are there any leaks in the fluid lines?
The controller can compensate for small changes
in supply pressure, but changes such as seen with
piston pumps without surge chambers or pressure
drop regulators can be a definite problem.
2. Material Viscosity
- Has the material properties such as
viscosity or temperature changed?
Changes in viscosity alter the way in which it
passes through the fluid metering and control
components (regulator, flow meter, check valves,
Y-Block, spiral mix tube, etc.). Typically, an in-
creased viscosity will require more pressure to
achieve the same flow rate. However, in some
cases, as with thixotropic materials, the viscosity
will actually change as the pressure varies or as
the material passes through the fluid regulator
or flow meter. Additionally, the material may be
broken down into smaller particles as it passes
through the fluid delivery system which can also
cause some materials to change their properties
as they flow.
The temperature of the fluid can also greatly im-
pact the flow properties. Make sure that the fluid
heaters are functioning correctly if temperature
control is being used. If temperature control is not
being used, then evaluate how ambient tempera-
ture may effect the fluid, as it is stored including
the paint kitchen. Also, consider the length of the
recalculating system and how long the material
takes to travel to the applicators.
The amount in which the control response is
effected by changes in fluid properties is also
determined by how aggressive the control param-
eters are set (Kp, Ki, Kd). The fluid flow response
can be observed as discussed in the "Operator
Interface" manual. Also, refer to the "PID Control"
in the "Operation" section of this manual under
3. Fluid Line Restriction
- Has a restriction formed somewhere in
the fluid line?
This could be a pinched paint tube, contamination
in the fluid regulator, spiral mix tube blockage,
a sticking check valve, or a Y block blockage to
name a few.
Corrective Action:
An easy way to verify that the system is capable
of flowing at the desired rate is to place the GUN
in CLEAN MODE and trigger the applicator. The
CLEAN MODE supplies maximum control pressure
to the fluid regulator. Watch the flow rate. If the
desired flow rate cannot be achieved or surpassed
in CLEAN MODE, it is obvious that it will not be
achievable in control mode. This tests all fluid
lines from the material supply to the applicator.
If calibration ports (valves) are available, such
as on 2K fluid panels, try operating the controller
with the calibration valves open. Place containers
under the calibration ports and put the controller in
RUN mode. If operating in AUTO-MATIC MODE,
the TRIGGER signal has to be