Dynaflow, User manual - introduction, Interface module – Ransburg DynaFlow User Manual User Manual
Page 11: Local operator interface
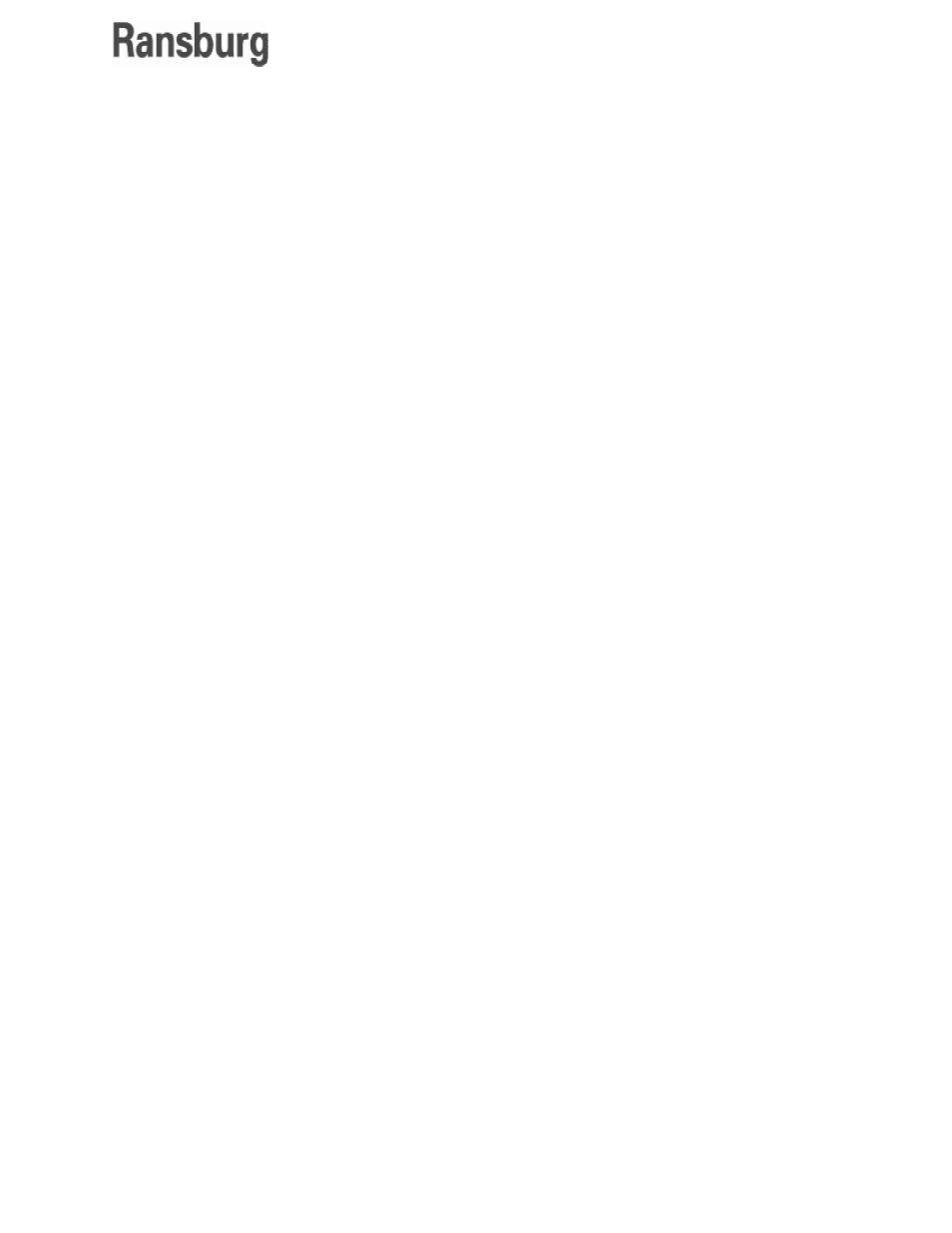
LN-9400-00.9
DynaFlow
TM
User Manual - Introduction
7
Located on the front panel of the Channel Mod-
ule are several status indicator lights (LEDs).
These are:
1. CPU - Is ON when the microprocessor is op-
erating normally.
2. ACTIVE - Is ON when communication is taking
place to the Interface Module.
3. FAULT - Is ON when there is a problem with
the module.
Interface Module
The Interface Module performs the following:
•
Stores system configuration and data
tables.
•
Acts as an interpreter for communication
with an external Host computer, PLC and/
or the local Operator Interface. Communi-
cates through a high speed Ransburg CAN
Bus data link to each Channel Module.
•
Responsible for system specific inputs and
supplying the necessary system specific
outputs for control and status.
Located on the front panel of the Interface Mod-
ule are several status indicator lights (LEDs).
These are:
1. CPU - Is ON when the microprocessor is op-
erating normally.
2. ACTIVE - Is ON when RIO communication
is taking place to an Allen-Bradley PLC.
3. FAULT - Is ON when there is a problem with
the module.
Local Operator Interface
Supplied as part of the DynaFlow Stand-Alone
Control Cabinet, Model# 77376 and A12233.
•
Permits total control of the system.
•
Displays system configuration and data to
the operator.
•
Computes and displays text and graphic di-
agnostic information.
•
Organizes, formats, and reports all data
and configuration tables.
The DynaFlow fluid flow control system achieves
real-time closed loop control through the use of
CHANNELs and GUNs. A CHANNEL consists
of an electrical-to-pneumatic (E/P) transducer,
material regulator and fluid flow meter combina-
tion through which a single material is controlled.
A GUN represents a single applicator through
which one or more materials are delivered. One
or more CHANNELs are configured for each GUN.
Two-component delivery systems (referred to as
2K systems) have two CHANNELs assigned to
a single GUN. The materials are statically mixed
before being delivered to the GUN.
Each CHANNEL operates independently of, and
simultaneously with all the other CHANNELs. This
lets the DynaFlow controller provide accurate dy-
namic regulation for each CHANNEL, regard-less
of minor system wear or changes in system vari-
ables. With a single-component coating material,
the DynaFlow controller detects changes from the
programmed flow rate and adjusts the output to
correct it. With two-component coatings (where
both the resin and catalyst are regulated and
monitored), the DynaFlow controller detects any
change in the total flow and makes the required
adjustments to maintain the programmed flow
and ratio. This holds the flow rates of the coating
components constant. Deviations from the desired
mix ratio are also immediately corrected using this
same closed loop process.
A detailed guide on PID control is supplied in this
manual to assist you should you want to adjust
the control parameters. There are many additional
features included in the DynaFlow Fluid Flow Con-
trol which reflect on the many years of experience
accumulated by Ransburg.
The control rack and OPERATOR INTERFACE
panels are consistent with and easily integrated
with other Ransburg control products into larger
custom system control panels. This optimizes
costs, space and functionality for control of multiple
applicator spray stations. Spray stations may also