Introduction, Features, Description – Ransburg DynaFlow User Manual User Manual
Page 10: Dynaflow, User manual - introduction, Channel module
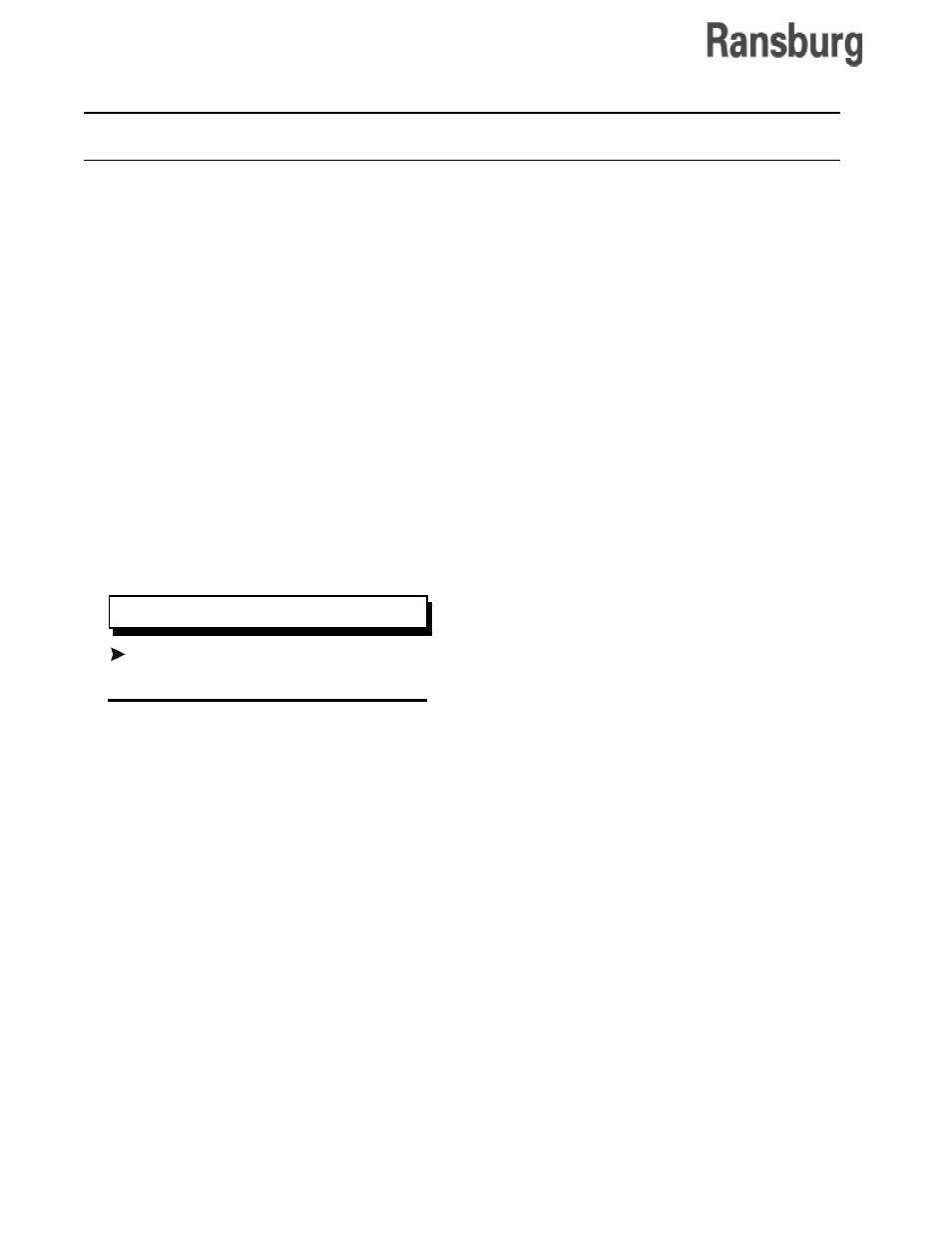
LN-9400-00.9
INTRODUCTION
DynaFlow
TM
User Manual - Introduction
6
FEATURES
• Configurable operating parameters (JOBs)
which can be saved and recalled on demand.
•
Graphic diagnostics for troubleshooting and
for achieving maximum system performance.
•
Comprehensive help information easily view-
ed on the OPERATOR INTERFACE.
•
Configurable manual and/or automatic GUN
applications.
•
Dynamic analog fluid control – the control of
flow rate while running a JOB.
•
Reverse fluid flow detection provides added
protection for system components.
DESCRIPTION
The ability to control the delivery of material greatly
increases the overall efficiency of the spray oper-
ating system and results directly in more uniform
and consistent paint finish quality and reduces the
amount of material waste. The ability of the fluid
flow controller to respond with quick, concise, and
repeatable control maximizes finish quality and
minimizes material waste.
The
DynaFlow
TM
Flow Controller design utilizes
a form of
distributed processing similar to many
of the industrial network architectures available
today. The entire task of fluid flow control is broken
up into parts. Each portion of the system is de-
signed for a specific purpose. Since each element
of the system is performing specialized functions,
and all elements are operating at the same time,
overall performance of the system is enhanced.
Functionality of the control system components
is as follows:
Channel Module
The Channel Module represents the core of the
system. Each Channel Module is responsible for:
•
Monitoring the CHANNEL specific inputs and
supplying the necessary CHANNEL specific
outputs for control and status.
•
Receiving and processing the flow meter
feedback pulses.
•
Determining the analog PID output control
signal by performing high-speed floating-
point math.
•
Receiving and interpreting commands from
the Interface Module through high speed
Ransburg CAN Bus communication.
•
Supplying data and status upon request to
and from the Interface Module.
NOTE
This feature requires flow meters that
provide reverse flow output.
•
Pot-life timer alarms.
•
Local and remote monitoring and control.
•
Discrete PLC interface capability for remote
control.
•
Remote I/O (RIO) communications link for
direct connection to Allen-Bradley PLCs.
•
Process and configuration error and fault de-
tection and reporting.
•
USB memory stick, backup of configuration
and operational data.
•
Versatile system integration.
•
Easy to use.
•
Help text and troubleshooting guide available
on screens.