KROHNE OPTIMASS with MFC 05x EN User Manual
Page 14
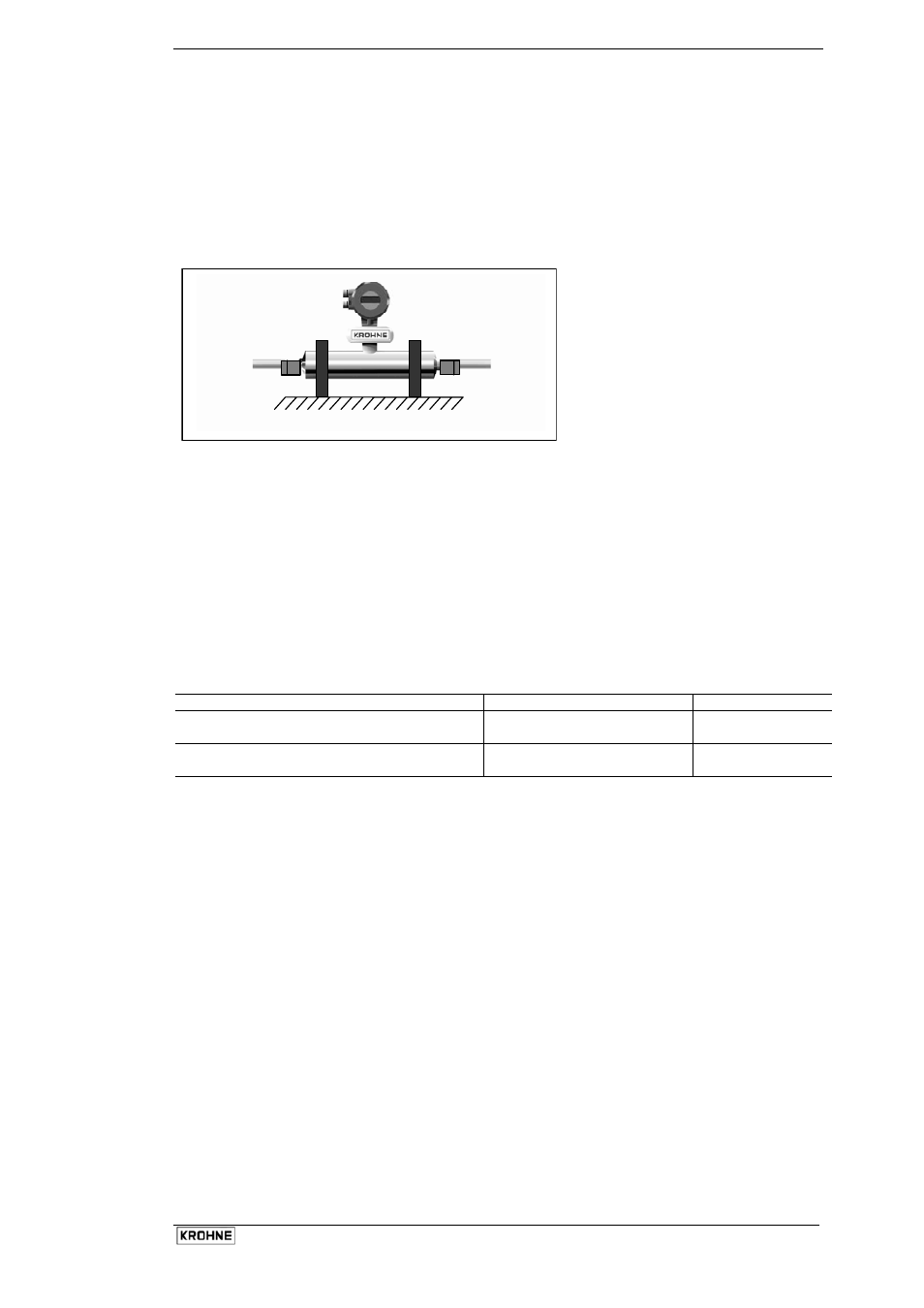
Installation and Operating Instructions OPTIMASS
13
1.2.6 Hygienic Applications
The OPTIMASS 7000 series is available with a variety of hygienic process connectors.
When using / installing meters with hygienic process connectors, care should be taken to ensure the
meter is well supported / clamped, as the meters are heavy and could injure when disconnected from
the adjacent pipe work.
The recommended method of installation is to mount the meter against a support / wall with the body of
the meter supported / clamped. The process pipe work can then be supported off the meter. The meter
is too heavy to be supported from the thin walled piping usually associated with the hygienic industry.
Meter supported from its body
Installation lengths
For installation lengths, please see section 1.2.10
Please check with KROHNE if you are unsure of the installation length. Many meters are built to
customer requirements / specifications especially where special hygienic process connectors have been
adapted to the meter. As these are normally non-standard, the installation length will not be given in the
technical data.
It is also recommended that the seals be replaced regularly to maintain the hygienic integrity of the
connection.
Hygienic Connection Materials
Version
Titanium Meter
SS 318 Meter
All welded DIN 11864
All welded Tri-Clamps
Titanium Grade 2
SS 318
Adaptor versions
316L Stainless Steel
316L Stainless Steel
EPDM seals
EPDM seals
Unless specifically requested, internal surfaces are not polished and no warranty is made as to the
surface finish. If polishing option and /or EHEDG, ASME Bio-Processing or 3A approvals was selected
at time of order, all product contact surfaces are polished 0.5 micrometer Ra (Ra 20) finish or better.
Use of OPTIMASS 7000 SS sensors above 100°C – Hygienic Connections only
Sizes 25S, 40S, 50S and 80S sensors with hygienic connections may be exposed to temperatures
above 100°C up to a maximum of 130°C for a maximum of 2 hours (e.g. for steam cleaning purposes).
The maximum temperature shock permitted either from cold to hot or from hot to cold is 110°C.
E.g. A meter measuring a product at 20°C can be immediately steam cleaned at 130°C, but a meter
measuring a product at 5°C can only be immediately steam cleaned at 115°C. Conversely, after steam
cleaning at 130°C the minimum allowed temperature of the product introduced immediately afterwards is
20°C.
Operation outside of these guidelines may cause shifts in the mass flow and density calibration.
Repeated shocking may also cause premature failure of the meter.