FEC DSP1500 (SAN3) User Manual
Page 95
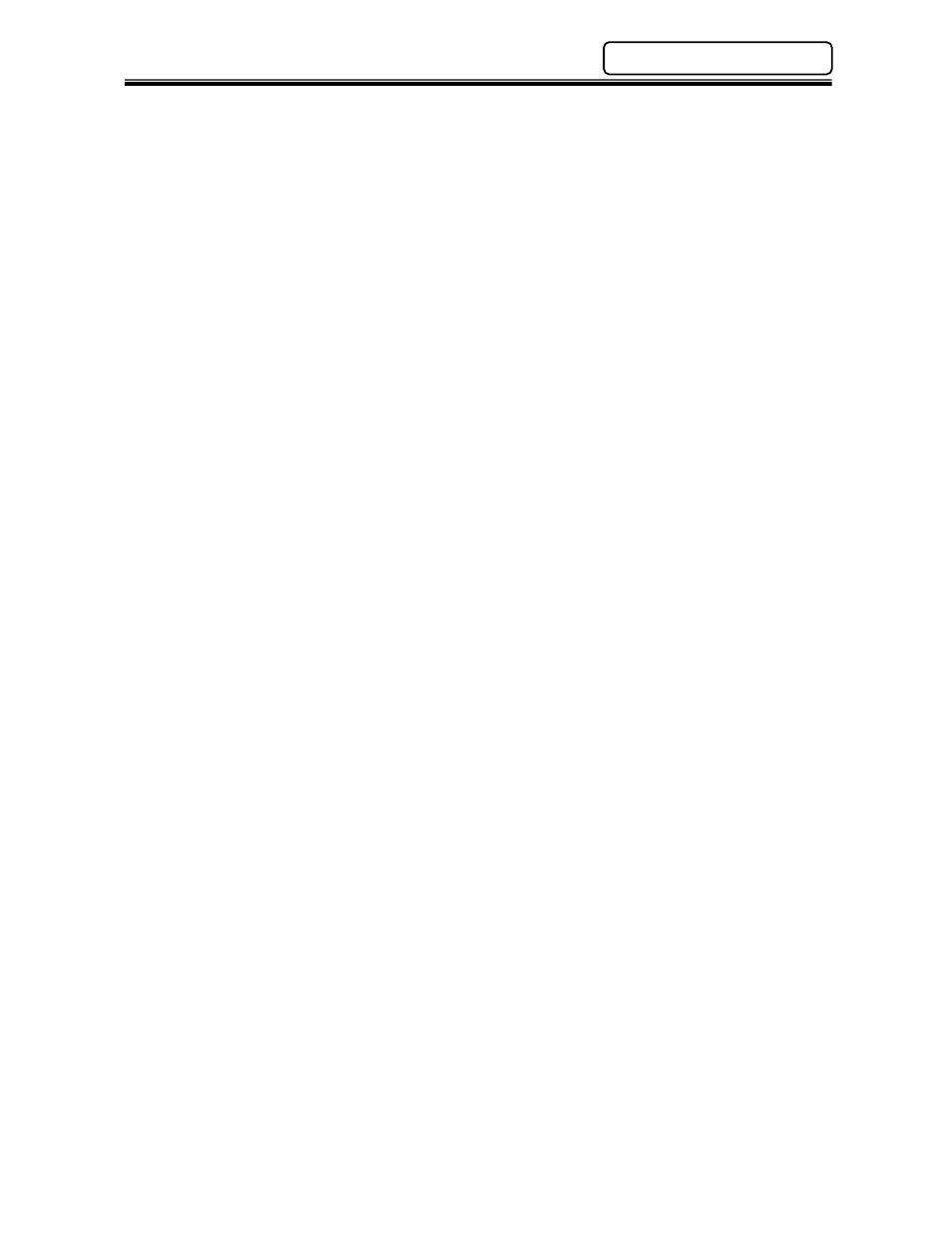
enFORCE
DSP1500 SAN Unit Operation Manual
PAGE 6-19 (Rev
4)
Chapter 6: System Operation
¾
Data number
04
Off Set Load [-(Calibration Load x 0.1) ~ Calibration Load]
This setting is used when there is heavy tooling attached to the tool that would require
added load for the press operation.
If it requires 5KN to move the tooling, set at 5. The press will see the 5KN as 0 and
control the operation accordingly
*Do not use if the tooling is free hanging and pulling on the press ram. Negative
values are not allowed, use “9” to depict negative
The setting is normally 0.
Setting Example: DPT-501R4H-25FS
-4.9KN ~ 49.0KN, so range setting is 904.9 ~ 49.0KN
¾
Data number
05
Distance Compensation [0 ~ 9.999mm]
This setting is used to compensate for the target distance value shifting due to part
movement or bending when a load is applied. The value to be entered reflects the
maximum movement/bend measured when the rated load of the press is applied to the
part/fixture. When set, the target distance will be adjusted proportionate to the load being
applied.
This is effective when you want to accurately control the distance in applications where
the fixture may deflect or part may bend when a load is applied.
¾
Data number
06
No Load Current Limit [0 ~ 1023]
This sets the current limit of the Servo when operating without load.
This softens the shocks caused from a crash at high speed by not raising the current
level more than is needed. If set correctly, any excessive load will cause the press motor
to stall.
*The normal setting is 250 ~ 500.
If the press seems to stall because of weight on the tip of the output shaft, set the value
higher.
¾
Data Number
07
Current Load Conversion Ratio [0 ~ 999%)
This data field sets the conversion ratio (as a percentage) of current control without the
load transducer.
*Normally it is set to 100(%).
¾
Data number
08
Home Position Offset [0 ~ 99.99mm]
This setting is for adjusting the Home Position after the “Home Position Search” has
been performed.
(Example: If 10 is set; after the Home Position Search has been performed and the zero
point set, the Home Position will be reset to 10mm from that zero point.)
Due to the fact that the Home Position is calculated from a proximity switch position, the
distance between Home and distance related data can also very between presses. So if
different presses are running the same operation or if a press needs to be changed out,
this setting is used to adjust for the difference between press units. In this case,
parameter settings can stay consistent for the part/operation.
¾
Data Number
09
Resolver Position [0 ~ 4095]
Offset adjustment for the resolver position value.
(Example: If the resolver position is 2816 and a value of 200 is input, then the controller
will see the resolver at position 2616)
*This only changes how the controller interprets the resolver position but does not
change the actual position of the resolver.
¾
Data number
10
Tool Number
This displays the tool number. No changes can be made.
¾
Data number
11
Tool Calibration Load
This displays the tool calibration load. No changes can be made.
¾
Data number
12
Tool Calibration Voltage
This displays the tool calibration voltage. No changes can be made.
¾
Data number
13
Tool Zero Load Voltage
This displays the tool zero load voltage. No changes can be made.
¾
Data number
14~ 1 A
In House Control Data
This displays in house control data. No changes can be made.