Dynasonics DXN Portable Ultrasonic Measurement System User Manual
Page 19
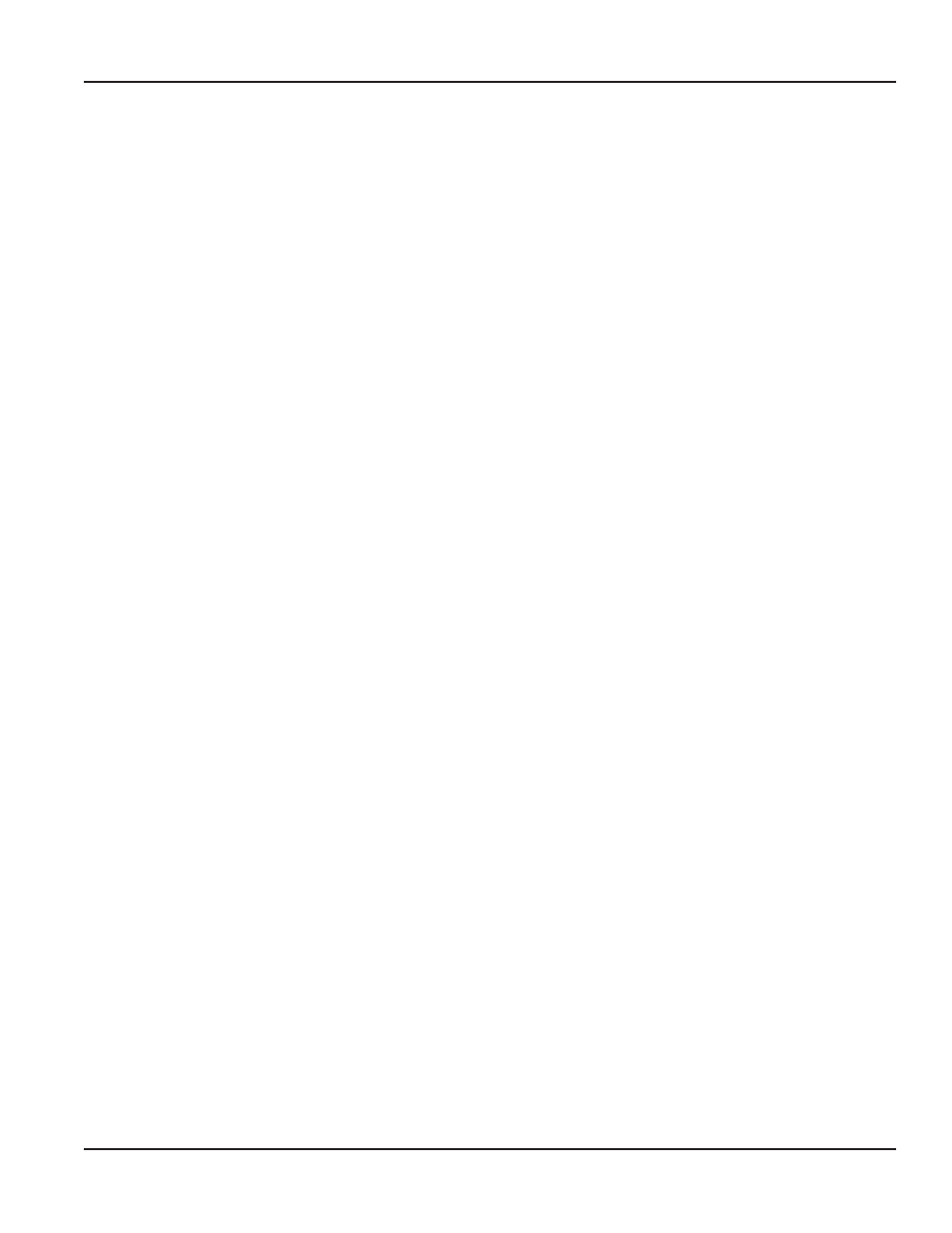
Pipe runs shorter than the minimums may sometimes be used with reduced accuracy. Unfortunately there is no way to
determine how much accuracy is sacrificed without doing in-field testing. For installations where the 10/5 pipe diameters rule
can’t be followed divide the total length of available straight pipe into thirds and mount the transducers with 2/3 of the pipe
upstream and 1/3 of the pipe downstream.
A full pipe is absolutely essential for making accurate flow measurements in either transit time or Doppler mode. The DXN has
no way to determine that the pipe is full or not. If the pipe is partially full the meter will over report the amount of flow by the
percentage of the pipe that is not filled with liquid.
An optimum transducer mounting location is defined as:
•
A piping system that is completely full of liquid when measurements are being taken. The pipe may become empty
during a process cycle – which will result in a Low Signal Strength error being displayed on the flowmeter while the
pipe is empty. This error code will clear automatically once the pipe refills with liquid. It is not recommended to mount
the transducers in an area where the pipe may become partially filled. Partially filled pipes will cause erroneous and
unpredictable operation of the meter.
•
A piping system that contains lengths of straight pipe such as those described in
Table 1
. The optimum straight pipe
diameter recommendations apply to pipes in both horizontal and vertical orientation. The straight runs in
Table 1
apply
to liquid velocities that are nominally 7 fps (2.2 mps). As liquid velocity increases above this nominal rate, the requirement
for straight pipe increases proportionally.
•
Mount the transducers in an area where they will not be inadvertently bumped or disturbed.
•
Avoid installations on downward flowing pipes unless adequate downstream head pressure is present to overcome
partial filling of or cavitation in the pipe.
Pipe Preparation
After selecting an optimal mounting location and successfully determining the proper transducer spacing the transducers
may now be mounted onto the pipe.
Before the transducers are mounted onto the pipe surface, an area slightly larger than the flat surface of each transducer must
be cleaned of all rust, scale and moisture. For pipes with rough surfaces, such as ductile iron pipe, it is recommended that the
pipe surface be wire brushed to a shiny finish. Paint and other coatings, if not flaked or bubbled, need not be removed. Plastic
pipes typically do not require surface preparation other than soap and water cleaning.
Signal Quality
When the DXN is in Hybrid Mode switching between transit time and Doppler is controlled by the signal quality. For any
mode setting selected from the Meter>Flow the signal quality must be at least 10% to obtain any readings.
Above a signal quality of 10% but below 40% the DXN will use the mode that develops the highest signal quality. If for
example the DXN sees 38% Doppler signal quality and 33% transit time signal quality Doppler mode will be automatically
selected.
Above 40% signal quality the DXN will use transit time.
Transit Time Transducer Installation
In transit time mode the flowmeter uses two transducers that function as both ultrasonic transmitters and receivers. The
transducers are clamped on the outside of a closed pipe at a specific distance from each other. The transducers can be
mounted in V-Mount where the sound transverses the pipe two times, W-Mount where the sound transverses the pipe four
times, or in Z-Mount where the transducers are mounted on opposite sides of the pipe and the sound crosses the pipe once.
The selection of mounting method is based on pipe and liquid characteristics which both have an effect on how much signal
is generated. The flowmeter operates by alternately transmitting and receiving a frequency modulated burst of sound energy
between the two transducers and measuring the time interval that it takes for sound to travel between the two transducers.
The difference in the time interval measured is directly related to the velocity of the liquid in the pipe.
Installation & Operation Manual
Page 19
February 2013