3 t y pes of digitizing – HEIDENHAIN TNC 426B (280 472) Touch Probe Cycles User Manual
Page 144
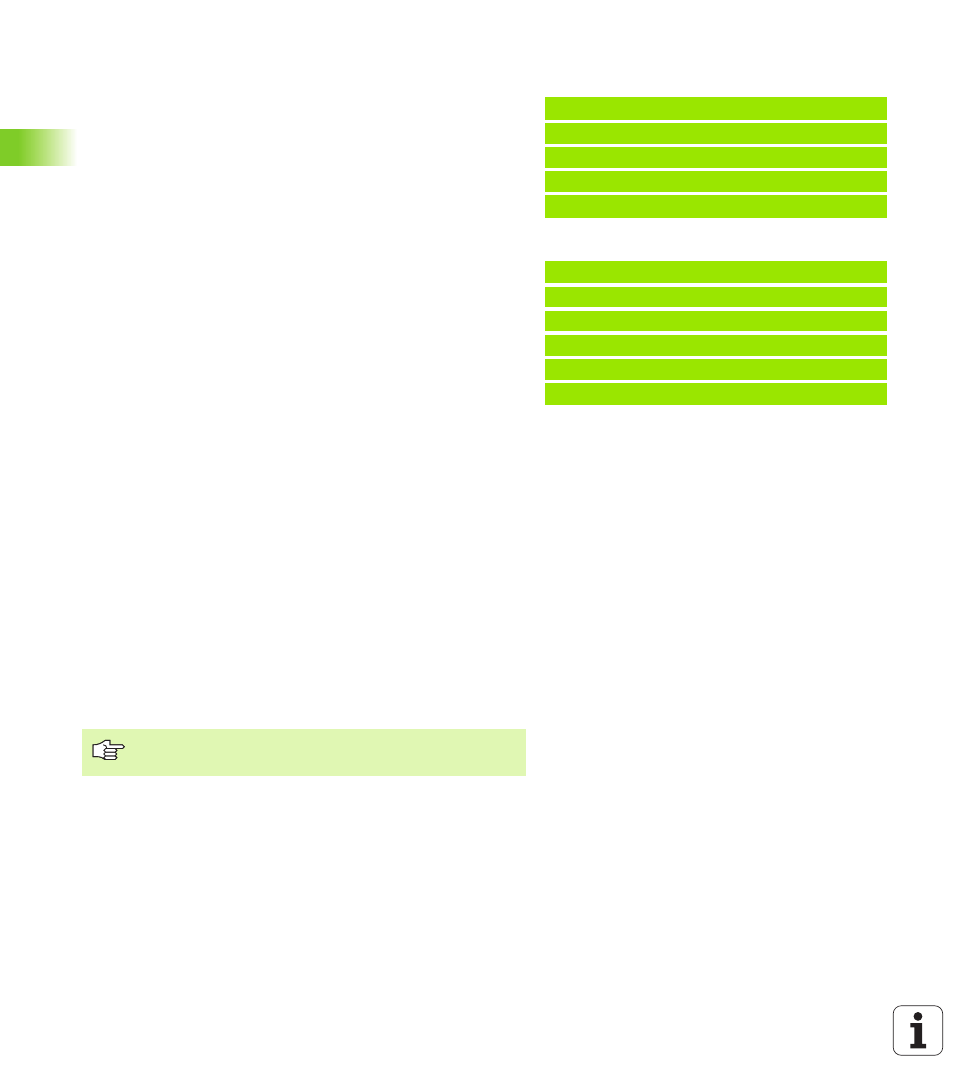
132
5 Digitizing
5.3 T
y
pes of Digitizing
Digitizing parameters
The parameters marked with an (M) apply to measuring touch probes,
those marked with an (S) apply to triggering touch probes:
U
U
U
U
Time limit
(M, S): Time within which the touch probe must orbit
the model and reach the first touch point. You can define a
maximum distance from the end point to the starting point with
machine parameter MP 6390. If the entered time limit is exceeded,
the TNC interrupts the digitizing process. Input range: 0 to 7200
seconds. The input value 0 means there is no time limit.
U
U
U
U
Starting point
(M, S): Coordinates of the starting position in the
working plane.
U
U
U
U
Axis and direction of approach
(M, S): Coordinate axis and
direction in which the touch probe approaches the model.
U
U
U
U
Starting probe axis and direction
(M, S): Coordinate axis and
direction in which the probe begins scanning the model. Defining
the direction at the same time determines whether the subsequent
machining operation is performed by up-cut or climb milling.
U
U
U
U
Feed rate F
(M): Enter the digitizing speed. Input range: 1 to 3 000
mm/min. Note that the higher the digitizing speed, the less accurate
the resulting data will be.
U
U
U
U
MIN. feed rate
(M): Probe feed rate for the first line. Input range: 1
to 3000 mm/min
U
U
U
U
Min. line spacing
(M): If you enter an input value that is smaller
than the programmed line spacing, the TNC decreases the spacing
between the scanned lines to the programmed minimum for
digitizing flat sections of a contour. This ensures that the density of
digitized positions remains constant even if complex surface
structures are scanned. Input range: 0 to 20 mm (M), 0 to 5 mm (S)
U
U
U
U
Limit in normal lines direction
(S): Distance by which the touch
probe lifts off the model after each deflection of the stylus during
scanning. Input range: 0 to 5 mm. Recommended input value: Enter
an input value between 50% and 100% of the probe point interval.
The smaller the ball-tip radius, the larger the Limit in Normal lines
direction should be programmed.
U
U
U
U
Line spacing and direction
(M, S): The offset by which the touch
probe moves to start a new contour line after completing the
previous one. The algebraic sign determines the direction in which
the probe is offset. Input range: -20 to +20 mm (M), -5 to +5 mm (S)
U
U
U
U
Max. probe point interval
(M, S): Maximum spacing between
consecutive digitized positions. The TNC also accounts for
important points that define the contour of the model, for example
at inside corners. Input range: 0.02 to 20 mm (M), 0.02 to 5 mm (S)
Example: NC blocks for triggering touch probes
60 TCH PROBE 7.0 CONTOUR LINES
61 TCH PROBE 7.1 TIME: 0 X+0 Y+0
62 TCH PROBE 7.2 ORDER: Y- / X-
63 TCH PROBE 7.3 TRAVEL: 0.5 L.SPAC: +0.2
PP.INT: 0.5
Example: NC blocks for measuring touch probes
60 TCH PROBE 17.0 CONTOUR LINES
61 TCH PROBE 17.1 TIME: 0 X+0 Y+0
62 TCH PROBE 17.2 ORDER: Y- / X-
63 TCH PROBE 17.2 F1000 FMIN500
MIN.L.SPAC: 0.2 L.SPAC: +0.5
PP.INT: 0.5 TOL: 0.1 DIST: 2
If you only want to digitize a single contour line, enter zero
for both the min. line spacing and the line spacing.