Safety reaction time, Considerations for safety ratings – Rockwell Automation 21G PowerFlex 750-Series AC Drives Reference Manual User Manual
Page 20
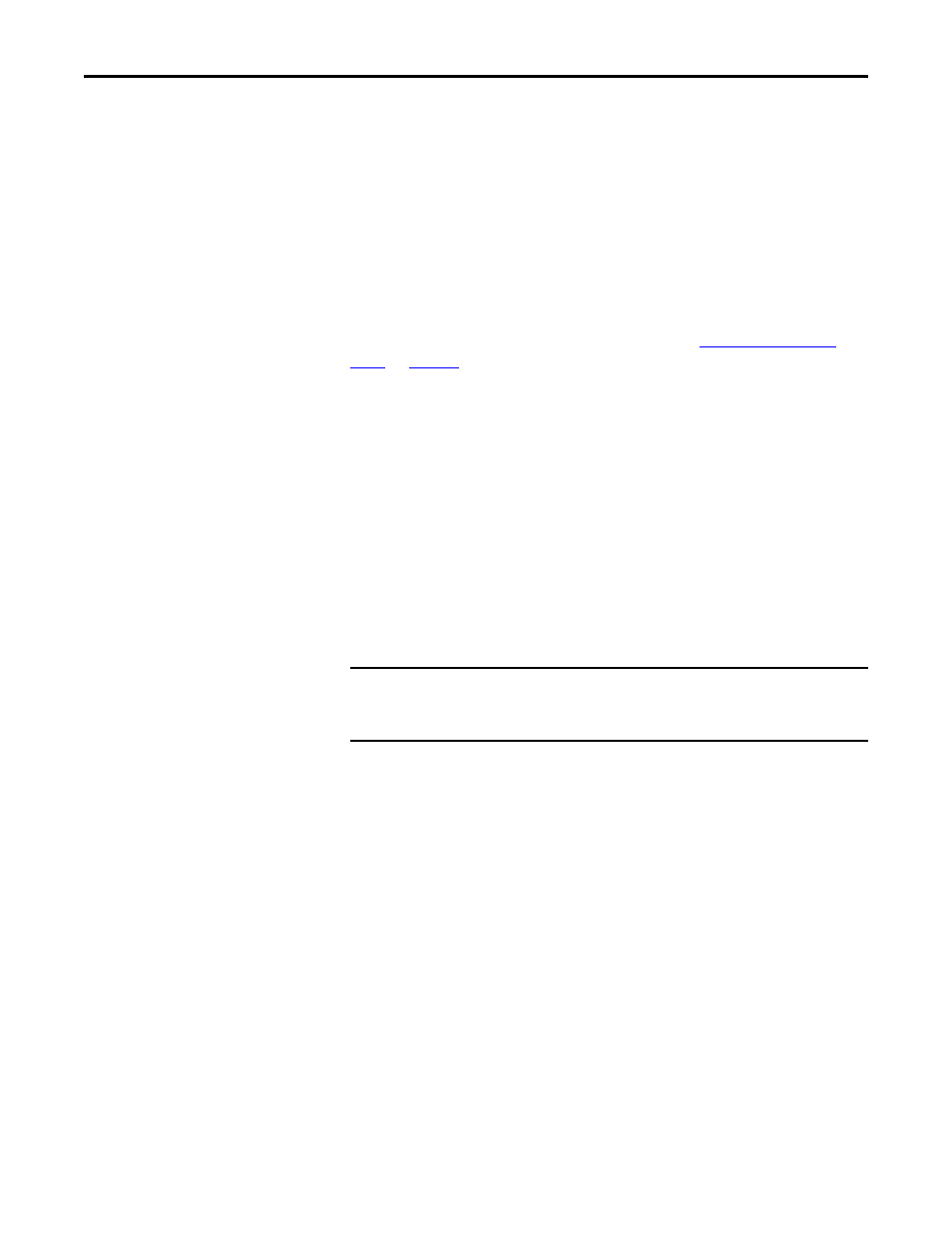
20
Rockwell Automation Publication 750-RM001F-EN-P - February 2012
Chapter 1
Safety Concept
Safety Reaction Time
The safety reaction time is the amount of time from a safety-related event as
input to the system until the system is in the Safe State.
The safety reaction time from an input signal condition that triggers a safe stop,
to the initiation of the configured Stop Type, is 20 ms (maximum) for drive
Frames 1…10.
The safety reaction time from an overspeed event that triggers a safe stop, to the
actual initiation of the configured Stop Type, is equal to the value of the P24
[OverSpd Response] parameter.
For more information on overspeed response time, see
Considerations for Safety
Ratings
The achievable safety rating of an application that uses the safety option installed
in PowerFlex 750-Series drives is dependent upon many factors, including the
encoder setup, drive options, output pulse testing, and the type of motor.
When using two independent encoders to monitor motion and when installed in
a manner to avoid any common cause dangerous failure, the PowerFlex safety
option can be used in applications up to and including SIL CL3, PL e, and CAT
4.
For applications that rely on commutation to generate torque and motion, a
safety rating up to and including SIL CL3, PL e, and CAT 4 can be achieved.
IMPORTANT
Some of the diagnostics performed on the encoder signals require motion to
detect faults. You must make sure that motion occurs at least once every six
months.