11 open and closed loop control, Function library – Lenze LDECBBF1xxxxxxHx User Manual
Page 73
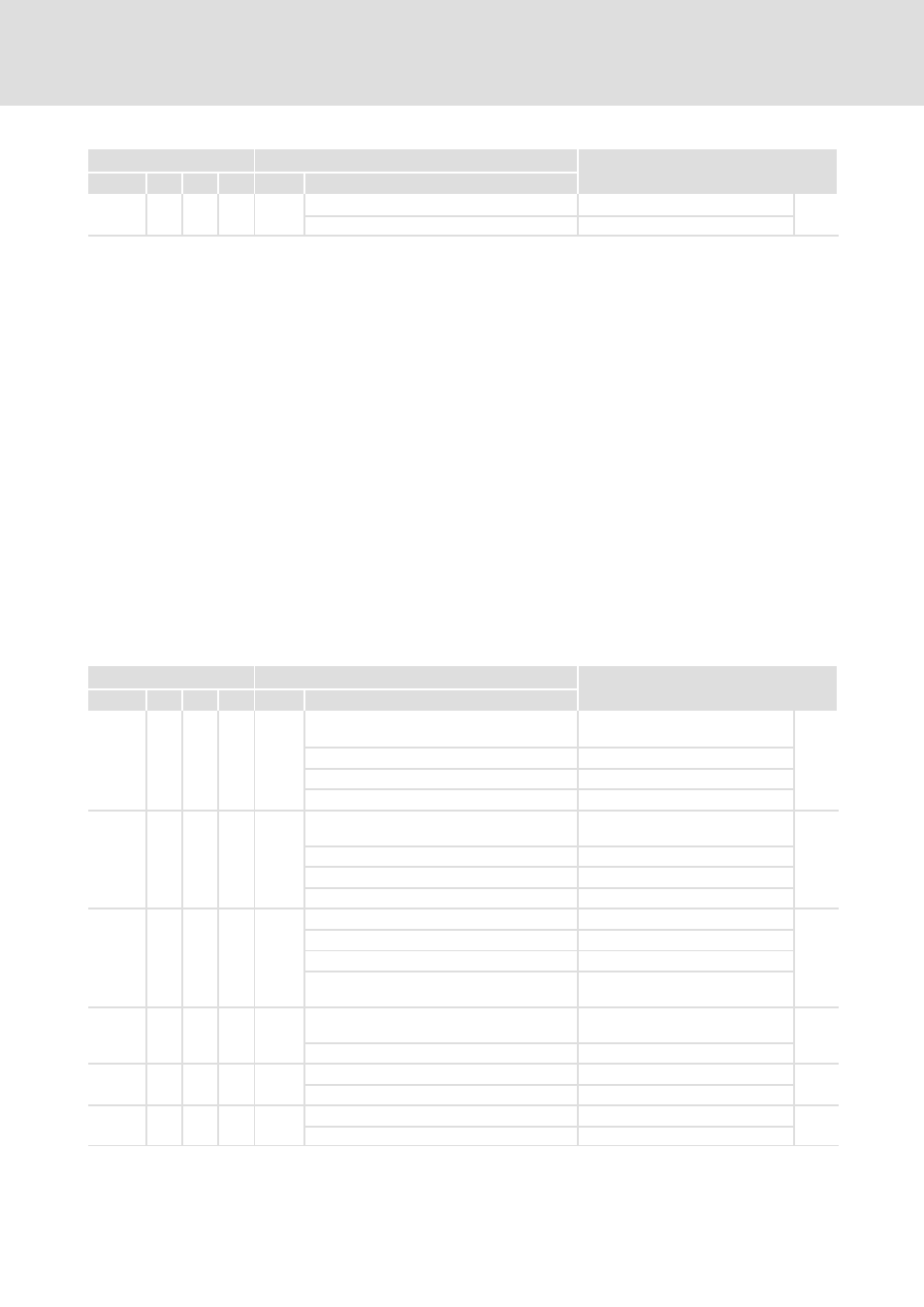
Function library
Open and closed loop control
l
73
LDEDS−CCU210B EN 4.0
Description
Possible settings
Code
Selection
Lenze
Byte
<
ñò
No.
C0605
R
1
Status of current HWC command
^ 70
0
201
8.11
Open and closed loop control
A virtual set position is continuously calculated from the setpoint frequency specified,
which is usually determined via HWC code range. This set position is compared to the
actual position, which is determined by means of an actual value encoder (e.g. incremental
encoder), and is compensated correspondingly. It is attempted to reach the rated slip of the
motor by reducing the boost voltage and to compensate greater system deviations by
adapting the actual frequency.
For setting the control, only the encoder constant [Inc/m], the gearbox factor [mm/min],
and the control limitation [Hz/10] have to be parameterised.
For monitoring, an error message can be generated when a parameterisable maximally
permissible system deviation is exceeded. Furthermore a corresponding error message for
the event that the control is active and the feedback (e.g. defective pulse encoder) is not
working is output.
Codes for parameter setting
Code
Possible settings
Description
No.
ñò
< Byte Lenze
Selection
C0129
RW
EXT
4
0
Configuration of encoder error
monitoring
^ 70
0
Off
1
Error
2
Warning
C0130
RW
EXT
4
0
Configuration of error monitoring
system deviation
^ 70
0
Off
1
Error
2
Warning
C0250
RW
EXT
1
0
HWC code range control mode
^ 70
0
No control
1
Control active
2
Control with pick−up after stop
function
C0257
RW
EXT
4
5.0
HWC control limitation (± of
setpoint frequency)
^ 70
1.0
{Hz}
10.0
C0258
RW
EXT
2
200
HWC maximum system deviation
^ 70
2
{mm}
5000
C0261
RW
EXT
2
1000
Encoder constant
^ 70
50
{inc/m}
5000