Despatch P1400+ Temperature Controller User Manual
Page 80
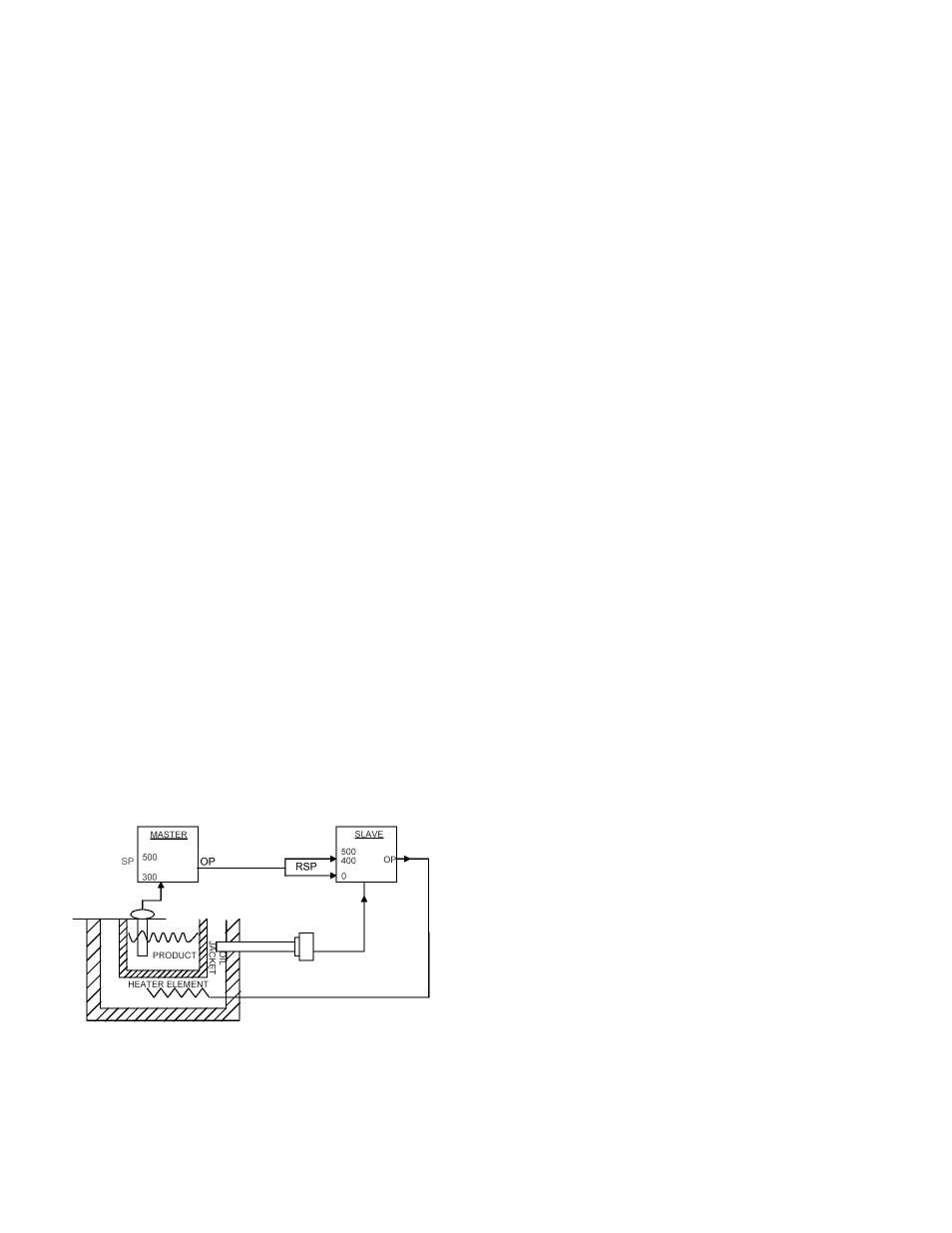
74
Bias (Manual Reset)
Type: Controller Tuning Parameter
Used to manually bias the proportional output(s) to compensate for process load variations. Bias is
expressed as a percentage of output power and is adjustable in the range 0% to 100% (for Primary
Output alone) or -100% to +100% (for both Primary and Secondary Outputs). This parameter is not
applicable if the Primary output is set to ON/OFF control mode. If the process settles below setpoint
use a higher Bias value to remove the error, if the process variable settles above the setpoint use a
lower Bias value. Lower Bias values will also help to reduce overshoot at process start up.
Display code =
biAS
, default value = 25%.
Also refer to
ON/OFF Control
and
PID
.
Bumpless Transfer
Type: Controller Definition
A method used prevent sudden changes to the output power level when switching between
Automatic and Manual control modes. During a transition from Automatic to Manual, the initial
Manual Power value will be set to equal the previous automatic mode value. The operator can then
adjust the value as required. During a transition from Manual to Automatic, the initial Automatic
Power value will be set to equal the previous manual mode value. The correct power level will
gradually applied by the control algorithm at a rate dependant on the integral action resulting from
the Automatic Reset time. Since integral action is essential to Bumpless Transfer, this feature is not
available if Automatic Reset is turned off.
Also refer to
Automatic Rest
and
Manual Mode
Cascade Control
Type: Controller Definition
Applications with two or more capacities (such as heated jackets) are inherently difficult for a single
instrument to control, due to large overshoots and unacceptable lags. The solution is to cascade two
or more controllers, each with its own input, in series forming a single regulating device. The product
setpoint temperature is set on the master controller. This is compared to the product temperature,
and the master’s PID output (mA or VDC) is fed into a remote setpoint input on the slave. The RSP
is scaled to suit any expected temperature. The slave loop’s natural response time should ideally be
at least 5 times faster than the master.
In the example, the maximum input represents 400ºC, thus restricting the jacket temperature. At
start-up the master compares the product temperature (ambient) to its setpoint (300ºC) and gives
maximum output. This sets the maximum (400ºC) setpoint on the slave, which is compared to the
jacket temperature (ambient) giving maximum heater output.
As the jacket temperature rises, the slave’s
heater output falls. The product temperature
also rises at a rate dependant on the transfer lag
between the jacket and product. This causes the
master’s PID output to decrease, reducing the
‘jacket’ setpoint on the slave, effectively
reducing the output to the heater. This continues
until the system becomes balanced.
When tuning a cascade system, first set the
master to manual mode. Tune the slave
controller using proportional control only (I & D
are not normally required) then return the master to automatic mode before tuning the master. The
result is quicker, smoother control with minimum overshoot and the ability to cope with load
changes, while keeping the jacket temperature within acceptable tolerances.
Also refer to
Manual Mode
,
Master & Slave
,
PID
,
Remote Setpoint
,
Remote Setpoint Lower Limit
,
Remote Setpoint Upper Limit
,
Setpoint
,
Setpoint Select
and
Tuning
.