IAI America ACON-PO User Manual
Page 86
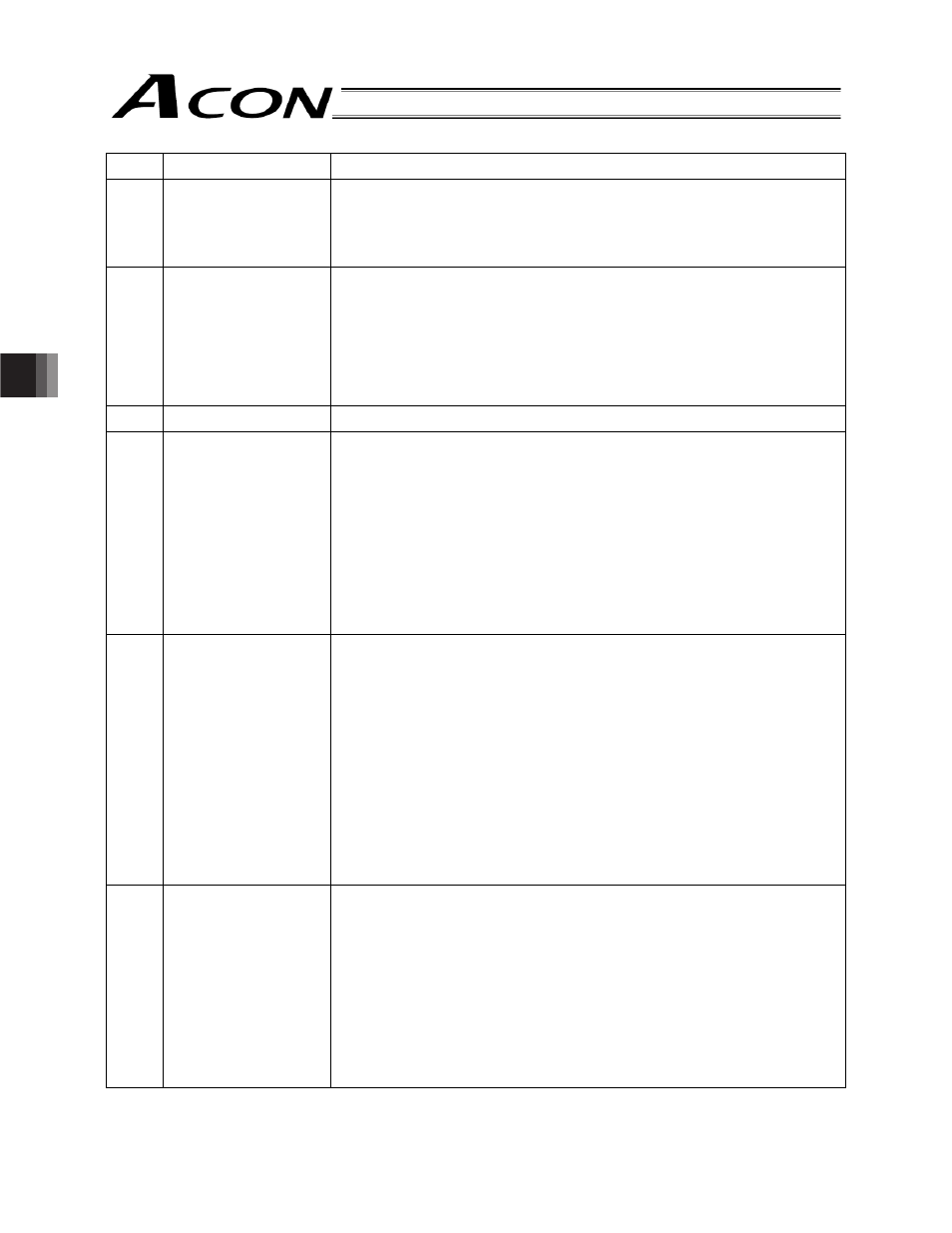
76
6. T
roubleshooting
n
o
i
t
c
a
/
e
s
u
a
C
r
o
r
r
E
e
d
o
C
0D8
Deviation overflow
The position
0D2
deviation counter has overflowed.
Cause:
[1] The work hit a surrounding object during movement and the impact
caused the speed to drop.
[2] The specified acceleration is too high for the transferred mass.
[3] The brake is improperly engaged and cannot be released correctly.
Action:
[1] Check the mechanisms around the work and make sure the work
does not receive any strong external force.
If [3] is suspected as the cause, contact IAI.
0D9
Software limit over
This alarm indicates that a soft limit was reached.
0ED
Absolute encoder error
(1)
Cause:
[1] When the power was reconnected following the completion of an
absolute reset, the current position changed due to an external
factor, etc., while the ABS unit was communicating.
[2] When an absolute reset was performed, the current position
changed due to an external factor, etc., while the controller was
communicating with the simple absolute unit.
Action:
[1] Detail code = H’0001
Turn on the power and then turn it back on in a condition where the
actuator does not receive vibration, etc.
[2] Detail code = H’0002
Perform an origin return operation again in a condition where the
actuator does not receive vibration, etc.
0EE
Absolute encoder error
(2)
Cause:
[1] The power was turned on for the first time after connecting the
battery of the simple absolute unit.
[2] Detail code = H’0001
The battery voltage dropped to a level at which the encoder counter
in the simple absolute unit could no longer retain the count.
[3] Detail code = H’0002
The encoder connector was unplugged or encoder cable suffered a
broken wire during power outage.
[4] Detail code = H'0003
The parameter was changed.
Action:
If [1], [2] or [4] is the case, perform an absolute reset according to the
specified procedure by referring to the operation manual for your
simple absolute unit (5.2, “How to Perform Absolute Reset”).
[2] Supply the power for at least 48 hours to fully charge the battery and
then perform an absolute reset.
0EF
Absolute encoder error
(3)
Cause:
When the power was cut off, the current value changed at a speed equal
to or above the set value of rotational speed due to an external factor,
etc.
Action:
Change the value set in the simple absolute unit and take an appropriate
action to prevent the actuator from moving at a speed equal to or above
the set speed.
If the battery backup time has enough allowance to do so, increase the
setting of motor speed.
Refer to: 5.1.1, “Piano Switch Settings” in the operation manual for your simple
absolute unit.
If this error has generated, perform an absolute reset according to the
specified procedure (5.2, “How to Perform Absolute Reset”).
Cause:
This error occurs when overvoltage of motor power has been detected
(38V or more)
Action:
Check the motor power input voltage (MPI terminal).
In case there is no fault found in voltage, malfunction of controller can
be considered. Please contact us.
Excessive motor
power-supply voltage