Ransburg, Appendix n: improving the accuracy of the rcs-2, Rcs-2 user manual - appendix – Ransburg RCS 2 Ratio Control System User Manual
Page 78
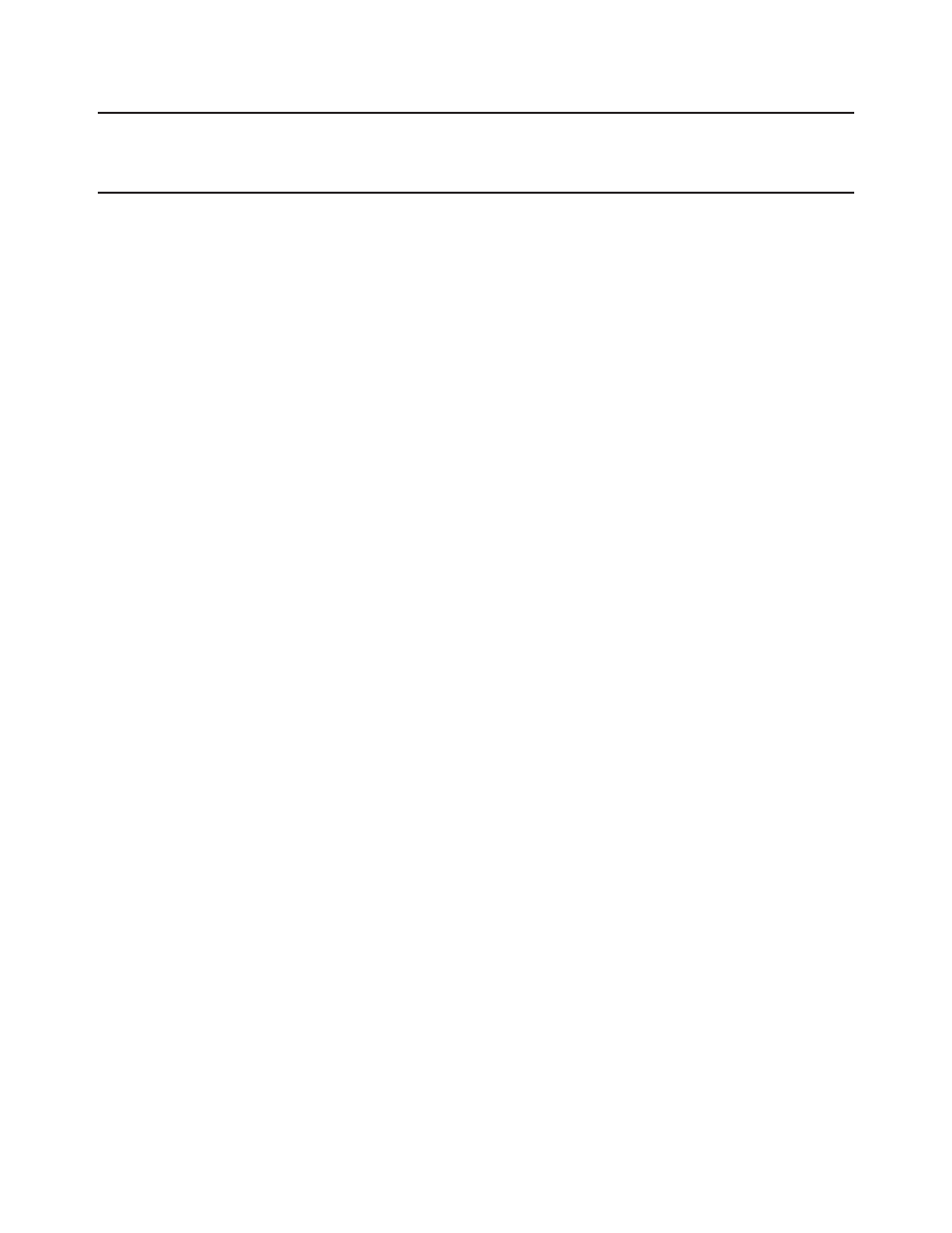
There are many ways that the accuracy of the
RCS-2 system can be improved. This article
presents three things that can and should be ex-
amined if it is necessary to improve the accuracy
of the machine.
Differential Pressure Control:
One of the first things that should be examined
is the differential pressure across the pumps. It
has been found that by keeping this differential
pressure to a minimum (5 psi or less), the pumps
act more as metering devices than pumps and
this allows them to be extremely accurate. If the
inlet pressure is too high, the material will tend to
“blow by” the pump gears (slippage) and more
material than desired will pass through the pump
If the inlet pressure is too low, the pump may be
starved and “cavitate” thus delivering too low of a
volume of material. (Cavitation is rarely a problem
as long as the supply tubing is of adequate size.)
The software in the RCS-2 is designed to auto-
matically control this differential pressure as long
as pressure transducers are installed at both the
inlet and outlet of the pumps and pilot-operated
fluid regulators (such as the Ransburg DR-1) are
provided on the inlets of the pumps. (The air pi-
lots must be controlled by the voltage to pressure
transducers in the RCS-2 motor amplifier panel.)
Since the outbound pressure of the pumps var-
ies based on fluid flow rate, fluid viscosity, hose
lengths, hose diameters, applicator orifices, etc.
the inlet pressure must be dynamic, as well. Note
that slippage is rarely a problem if the viscosity
of the material is 25 cps or greater and cavitation
issues can be minimized by insuring that the flu-
id delivery tubing is of adequate size. Inlet fluid
regulators are seldom required when supplying
fluid from pressure pots.
Pump Volume per Revolution and Flow Rate:
Note that the channel cards in the RCS-2 do not
perform closed loop control of the motor RPM
based on a comparison of the desired RPM and
the speed feedback from the motor amplifier. The
channel card commands the motor amplifier to
APPENDIX N: IMPROVING THE ACCURACY OF
THE RCS-2
spin the motor at the desired RPM and the motor
amplifier has its own closed loop control with the
motor. If the motor is not able to run at the desired
RPM, the motor amplifier generates a fault, which
is then fed back to the RCS-2 channel card. The
RCS-2 channel card does confirm that the motor
is running at the desired RPM (within the tolerance
programmed on the Configure Gun screen) but
it does not try to compensate for over or under
speed conditions by modifying the analog signal
to the motor amplifier.
On the Configure Channel screen of the RCS-2
user-interface software there is a value named
Pump Size. It is expressed in cc’s/revolution of
the pump. This value is normally obtained from
the pump manufacturer and is accurate enough in
almost all applications. There are cases, however,
(especially after a pump has been used for quite
some time) when accuracy can be improved by
modifying this value slightly. The way that the
RCS-2 channel card determines how fast to spin
the pump is based simply on two values, the target
flow rate of the material and the value entered
for Pump Size on the Configure Channel screen.
For example, if the pump is programmed as a
10 cc/rev. pump and the desired flow rate is 300
cc’s/min, the software can easily determine that it
has to run the pump at 30 RPM. Since the motor
amplifier has been programmed to spin at 0 RPM
with a 0 volt input and at 150 RPM with a 10 volt
input, the software can then determine it must
send exactly 2.000 volts to the motor amplifier to
obtain the desired 30 RPM. However, because of
very minor inaccuracies in the pump, the analog
output of the channel card, the analog input of the
motor amplifier, cable and connector resistances,
etc. the desired 300 cc’s/min could be off slightly.
By making very minor adjustments to the Pump
Size value on the Configure Channel screen,
these minor variations can be accounted for and
the channel’s accuracy improved significantly.
Calibration of the pumps can be performed in the
following manner: Program the RCS-2 controller to
RCS-2 User Manual - Appendix
75
LN-9407-00.2
Ransburg