Ransburg, Appendix g: catalyst flow sensor, Description & operation – Ransburg RCS 2 Ratio Control System User Manual
Page 60: Specifications
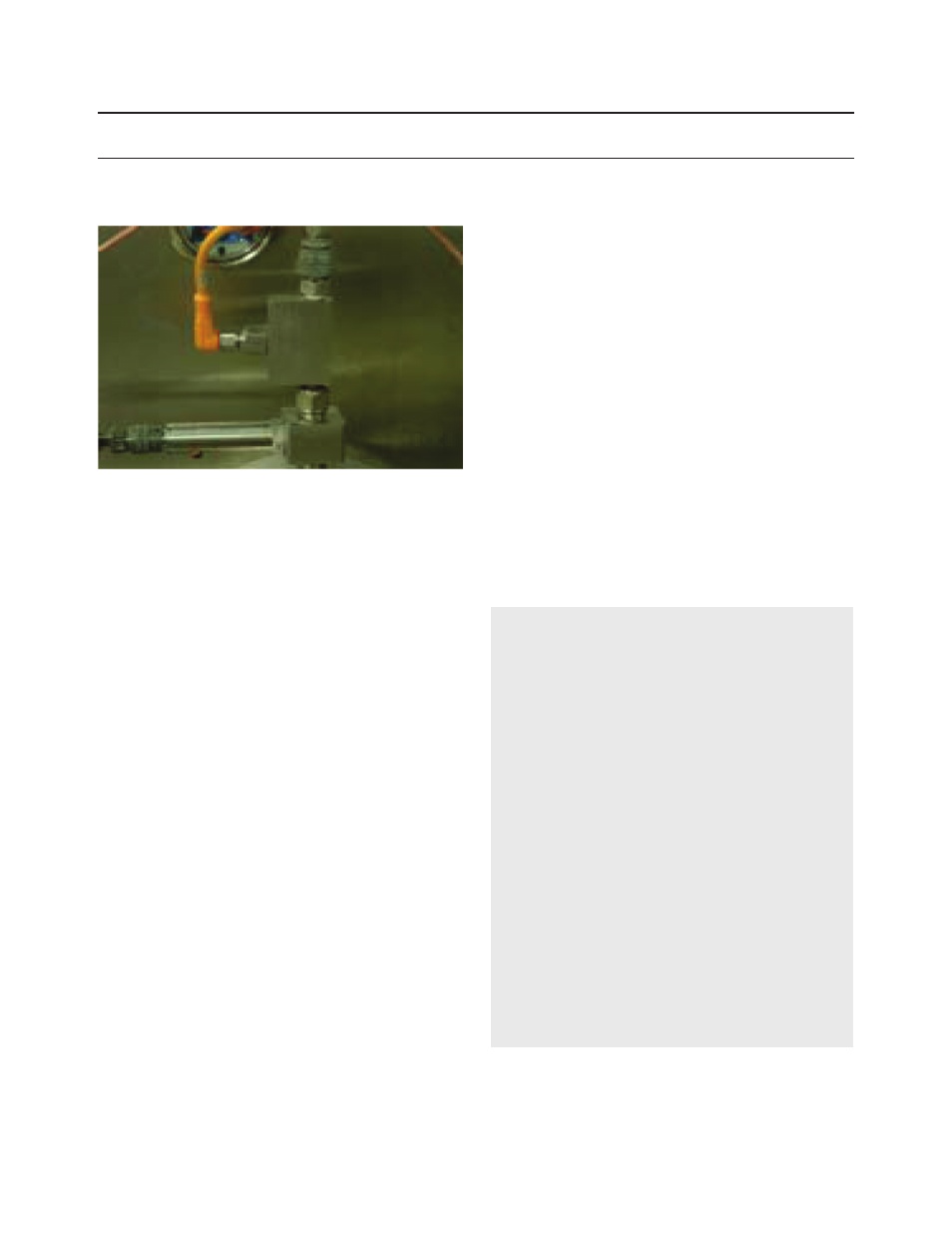
APPENDIX G: CATALYST FLOW SENSOR
CATALYST FLOW SENSOR
DESCRIPTION &
OPERATION
The FLOW MONITOR control system used to de-
tect no-flow in the hardener fluid system consists of
three components, a sensor, the control amplifier,
and the analog output amplifier. The sensor is a
thermal shedding type that uses the principle of
thermal conductivity. The temperature compensat-
ed sensing head is inserted into the fluid stream
via a manifold and is heated up a few degrees
higher than the medium. The control amplifier
provides all of the necessary electronics to provide
heater current, temperature comp-ensation, level
adjustment for the sensor and a low level analog
output signal which is a function of flow. The third
component is the analog output amplifier which
provides a 4-20ma control signal to the micropro-
cessor on the channel board. The operation of the
flow monitor system is as follows… The sensor
is heated up a few degrees above the ambient
temperature of the fluid. If the fluid is moving, the
heat generated in the sensor is conducted away
from the sensor head and the sensor is cooled.
If the fluid is at rest or at a no-flow condition, the
temperature of the sensor head rises. Thermistors
are used in the sensor to convert the temperature
into an electrical signal which is processed by
the control amplifier. The control amplifier also
compensates for changes in fluid temperature at
a rate of up to 15° C/min. When there is flow, the
analog output voltage increases, and when there
is no flow, the analog output voltage decreases.
The analog output voltage is then fed into the
analog output amplifier which outputs a 4-20ma
signal that is used by the channel board to de-
termine flow status. The program in the channel
board determines whether there is flow or no-flow
by checking the slope of the analog signal and by
checking the programmable flow/no-flow levels.
The program also allows for the adjustment of the
flow-on and the no-flow levels via parameters in
the user interface software. Also, to allow for the
delay in the thermal sensor signal, a programmable
time delay is available to prevent nuisance faults.
SPECIFICATIONS
Input Power Requirements:
Voltage- +24vdc +/-10%
Current - 80ma (maximum)
Ambient Temperature Range: 0 - 55° C
Compensated Fluid
Temperature Range: -25 to 80° C
Minimum Flow Rate: 20cc’s/min
Operating Flow Rate Range: 20 - 600cc/min
Analog Output Signal: 4 - 20ma
Response Time: Flow Rate Dependent
Maximum Fluid Pressure: 200psi
Controls: (1) Zero Flow Adjust
RCS-2 User Manual - Appendix
57
LN-9407-00.2
Ransburg