Ransburg, Rcs-2 user manual - appendix – Ransburg RCS 2 Ratio Control System User Manual
Page 62
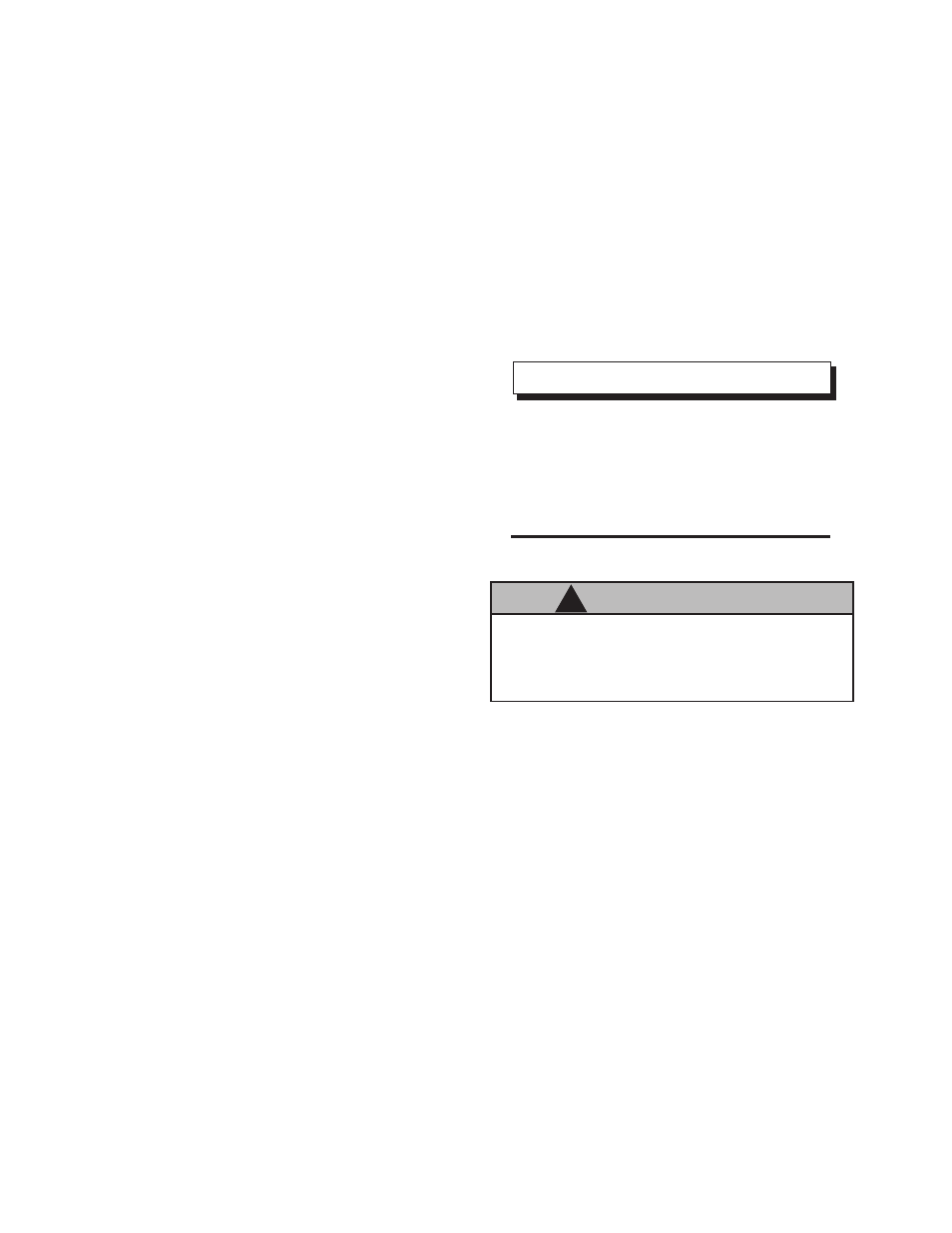
more nuisance errors can occur. If values larger
than the minimum spray-on time are programmed,
hardener flow errors will be detected because the
delay time accumulates every time the spray-on is
turned on and off without detecting a valid current
input level (i.e. positive slope at a level above the
value programmed for no-flow or a value above
the programmed flow-on level).
The no-flow and flow-on levels can now be
programmed to fit
the application. Current mea-
sured at the output of the analog output amplifier
provides information to the RCS-2 channel card.
Program-ming specific values can speed up or
slow down system response to given flow condi-
tions. Programming the no-flow value as low as
possible, will help minimize response time from
a no-flow to flow-on condition, but if it is too low,
fluid noise could periodically cause indications of
flow when, in reality, there is no flow.
Programming the flow-on value to the lowest
possible value will minimize response time to a
flow-on to no-flow condition, but in this case fluid
noise could cause nuisance errors when there is
actually flow. The best way to set up the no-flow/
flow-on values is to begin with the default values
indicated above. Monitor the output current from
the Analog I/O Screen with the system operating
normally. Set the flow-on value to about 1-2 mA
below the minimum measured current during
normal operation. (Note: Fluid must be flowing
to properly set this value.) To set the no-flow
value, turn the hardener supply off. Monitor the
output current from the analog output amplifier.
The current should begin to decrease and steadily
fall until it begins to approach a level of approxi-
mately 4.8 mA, (the no-flow zero reference value).
Note: In order to prevent system shutdown, go
to the Configure Alarm setup screen on the User
Interface Screen of the RCS-2 and temporarily
program the system for no shutdown on hardener
flow loss). This will allow the motor to continue to
run and provide a good indication of fluid noise at
the no-flow condition. Observe the output current
> Remember to reprogram the system
to shut down on Hardener Flow Loss
after completing this setup, if required.
C A U T I O N
!
>
The above should only be used as a
guide. the final parameters for the Hard-
ener flow Monitoring system will vary with
the requirements for each individual sys-
tem, and they will be the final determining
factors of these parameters.
NOTE
level under these conditions and program the
no-flow level to approximately 0.5 mA above the
peak current level measured. Best system per-
formance will vary depending upon the system
and setup accuracy.
RCS-2 User Manual - Appendix
59
LN-9407-00.2
Ransburg