Ransburg, Setup and adjustments, Rcs-2 user manual - appendix – Ransburg RCS 2 Ratio Control System User Manual
Page 61
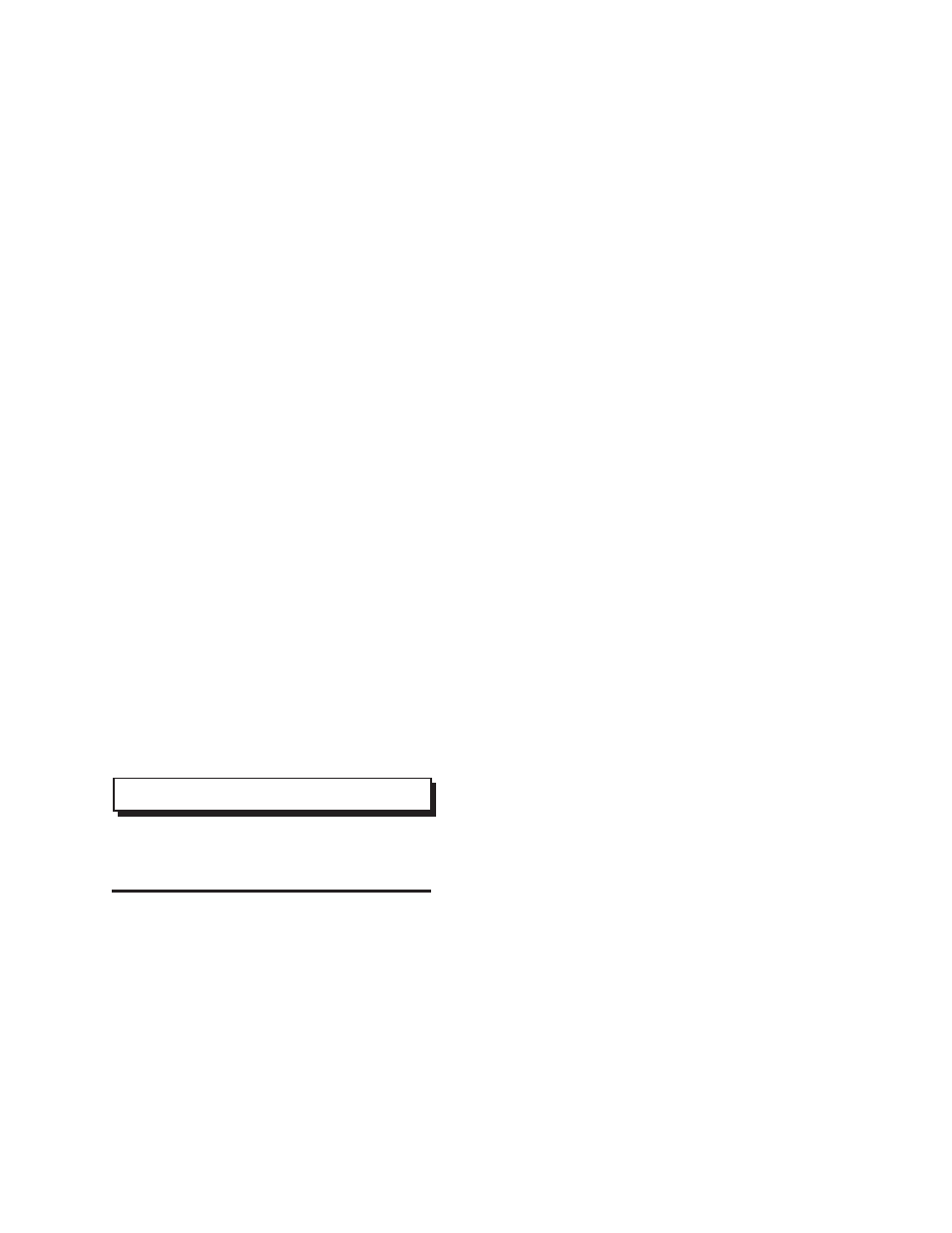
Since all catalysts are not the same and have
differing abilities to remove heat from this se sor,
the sensor must be calibrated prior to use.
Setup and Adjustments
Refer to the System Interconnect Diagrams in
the Maintenance/Troubleshooting manual before
proceeding with any of the following setup and
adjustment procedures.
Access the Digital/Analog I/O screen on the User
Interface Screen of the RCS-2. Select the Analog
I/O option. On this screen, the current coming
from the analog output amplifier can be monitored.
1. Fill the system to be monitored with the fluid
to be monitored (NOTE: YOU CANNOT USE AIR
AS THE FLUID!)
2. Monitor the output current from analog output
amplifier (P/N: 22-1050) on the User Interface
Analog I/O Screen.
3. Let the fluid stand in the line (NO Fluid Flow)
for a minimum of 60 seconds. (The longer you
can let the fluid stand, the better the accuracy
and response time of the Flow Monitor System.)
4. Make sure the switch on the control amplifier
(P/N: 22-1046) is set to position 1 (LIQUID).
User Interface Parameter Setup
There are three parameters that must be pro-
grammed for this feature to work correctly.
Hardener Flow On – This is the level (in milli-
amps) above which the hardener is considered
to be flowing.
Hardener No Flow - This is the level (in milliamps)
below which the hardener is considered as not
flowing.
(The Hardener Flow On parameter must always
be greater than the Hardener No Flow parameter.)
Note that if the current being sensed is between
the Hardener No Flow nad the Hardener Flow
On setpoint, as long as the flow is increasing, the
processor will assume that hardener is flowing.
If the flow being sensed is between these two
values and is not changing or is decreasing, the
processor will assume that there is no hardener
flow.
Hardener Sample Time – This is the time period
of no hardener flow that the hardener no flow timer
should accumulate to before generating a fault.
This time continues to accumulate as long as the
processor sees no hardener flow regardless of the
number of applicator triggers. The timer is reset
every time the flow meets or exceeds the value
programmed in for Hardener Flow On.
The initial setup for these parameters should be
set to the following values: delay time = 4 sec-
onds, no-flow = 6 mA, flow-on = 10 mA. After the
zero flow calibration has been done correctly, the
system can now be programmed to fit
the applica-
tion. The delay time is used to prevent nuisance
hardener flow errors. To properly set this time to
minimize delays and prevent nuisance errors, the
delay time should be set to a value which is less
than the minimum spray-on time of the system
being measured. The delay time is cumulative
to allow for short spray-on times used in some
applications. The smallest difference between the
delay time and the minimum spray-on time should
be 100 mSec. Smaller values can be used, but
>
If the current continues to vary after
you adjust the pot, you have not waited
long enough.
NOTE
5. Adjust the trim potentiometer on the control
amplifier until the output current displayed on
the User Interface Screen is equal to 4.80mA
+/- 0.10mA.
6. This completes the zero flow adjustment of the
hardener no-flow detect system.
RCS-2 User Manual - Appendix
58
LN-9407-00.2
Ransburg